maxon Inside
Wanneer alle andere materialen het laten afweten
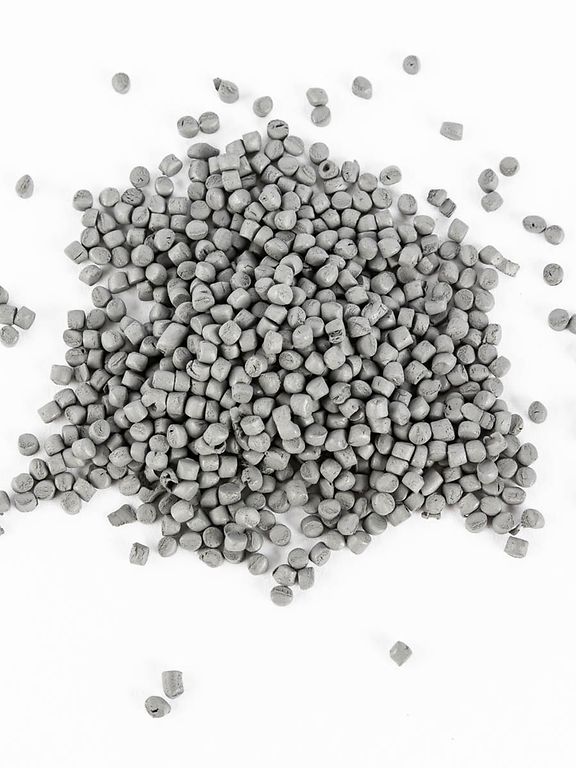
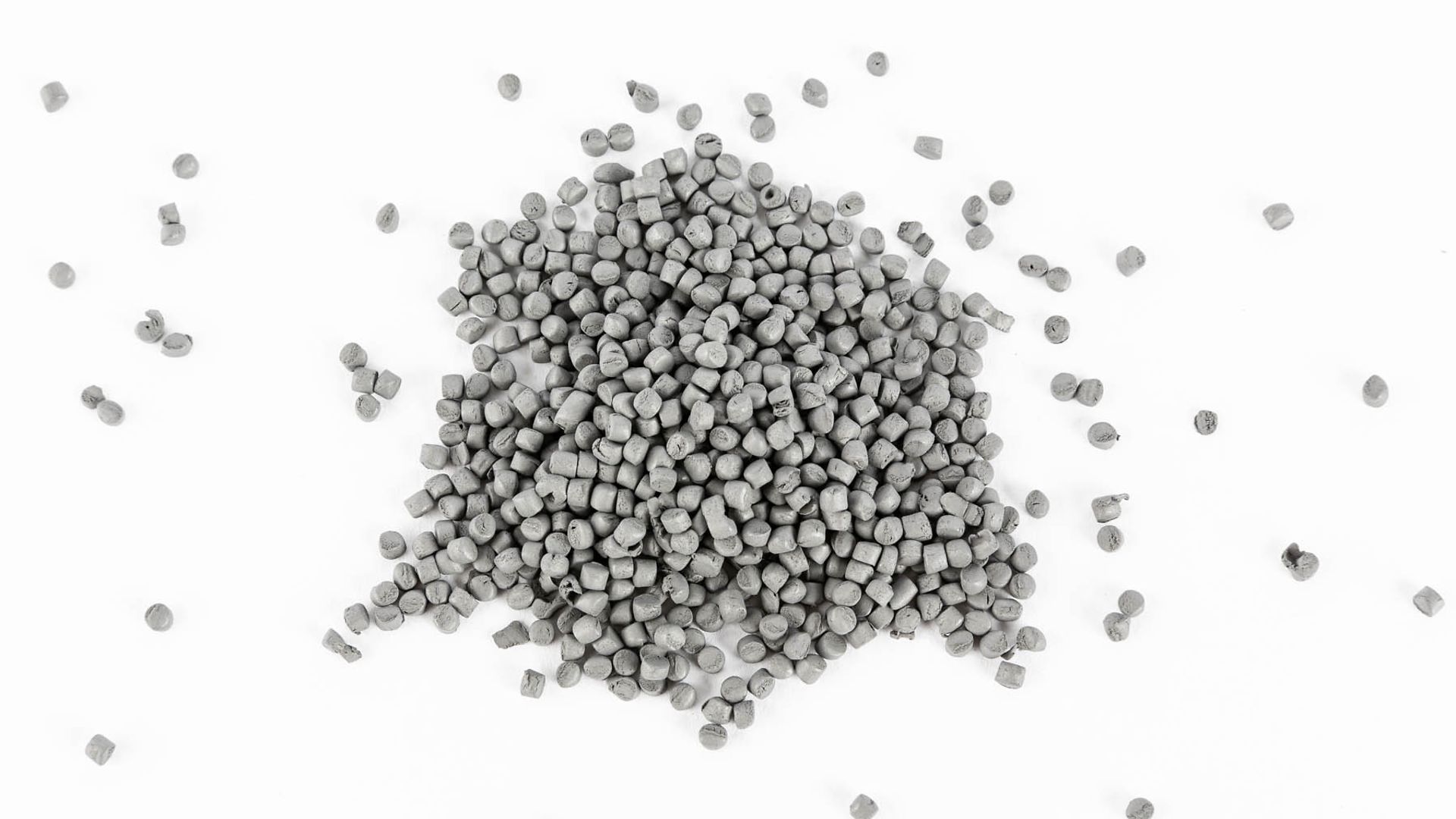
Over de hele wereld staat maxon bekend om zijn uiterst precieze aandrijvingen. Weinig mensen weten dat het bedrijf een eigen spuitgietafdeling heeft voor keramiek en metalen. Hier worden niet alleen keramische spindels gemaakt, maar ook speciale onderdelen voor horlogemakers en de muziekindustrie. Keramiek is een uitstekend materiaal voor het versterken van overbrengingen. Daarom richtte maxon 20 jaar geleden zijn eigen afdeling voor poederspuitgieten op. Tegenwoordig worden sommige keramische onderdelen die hier gemaakt worden zelfs gebruikt om de luisterervaring van muziekliefhebbers te verbeteren.
De grootste trots van de afdeling krijgt nu een eigen ruimte. Andreas Philipp, hoofd van maxon’s poederspuitgietafdeling, loopt naar de nieuw geplaatste wanden, opent de deur en wijst naar de enige machine in de kamer: een laserapparaat voor het bewerken van harde keramische onderdelen. Deze nieuwste aankoop kan keramiek snijden met een nauwkeurigheid van 2 micrometer, legt Philipp uit. Door veerelementen met een wanddikte van 17 micrometer te bewerken en tegelijkertijd nauwkeurige metingen uit te voeren, blijft de afdeling voorop lopen en kunnen nog sneller precisieonderdelen aan klanten worden geleverd.
Keramiek voor een langere levensduur
Waarschijnlijk weten niet veel mensen dat maxon een eigen spuitgietafdeling voor keramiek en metalen heeft. Het bedrijf is immers vooral bekend om zijn micromotoren die toepassingen zowel op Mars als hier op aarde draaiende houden; van chirurgische robots en laboratoriumautomatiseringssystemen tot tatoeagemachines.
Naast precisieaandrijvingen maakt maxon ook controllers, encoders en met name overbrengingen. Voor bepaalde toepassingen moeten deze onderdelen worden versterkt. Om precies te zijn gaat het hierbij om aparte overbrengingscomponenten zoals tandwielen, assen of planeetdragers. Keramiek is hiervoor bijzonder geschikt. Het materiaal is immers beter bestand tegen chemicaliën en temperatuurschommelingen dan staal, en bovendien zeer hard. Keramische assen verlengen de levensduur van een overbrenging aanzienlijk, vooral voor aandrijvingen die in start-stop-bedrijf worden gebruikt. Daarom is maxon ongeveer twintig jaar geleden begonnen met de productie van eigen keramische onderdelen. In de spuitgietafdeling werken momenteel ongeveer 45 medewerkers, waaronder ontwikkelaars, application engineers, kwaliteitsexperts en productiemedewerkers.
Van motor tot spindel
De experts op het gebied van poederspuitgieten maken deel uit van de gespecialiseerde productielocatie voor overbrengingen van maxon in Sexau, Zuid-Duitsland. Ongeveer de helft van de onderdelen die de afdeling maakt, wordt in maxon aandrijvingen gebruikt. Vooral de keramische spindels voor lineaire aandrijvingen zijn gewild, vanwege hun goede loopeigenschappen en slijtvastheid. “We zijn het enige bedrijf dat klanten een motor, overbrenging en keramische spindel uit één hand kan aanbieden,” aldus Andreas Philipp. De ontwikkeling en productie van keramische precisieonderdelen is niet goedkoop. De processen zijn complex en bewerkingen van harde materialen vereisen diamantgereedschappen of, zoals hierboven vermeld, lasermachines. Daarom wordt keramiek doorgaans alleen voor zeer specifieke toepassingen gekozen als andere, meer gebruikelijke materialen niet aan de vereisten voldoen. Anders gezegd: “Keramiek wordt gebruikt wanneer alle andere materialen het laten afweten.”
Twee dagen in de oven
Het productieproces begint met een granulaat, ook wel grondstof genoemd. Dat bevat een bepaalde hoeveelheid lijm, zodat het materiaal in eerste instantie in vormen kan worden geperst. Nadat de onderdelen de spuitgietmachine hebben verlaten, kunnen ze al licht worden bewerkt. Ze lijken dan echter nog niet op de afgewerkte keramische producten. Dit worden de ‘groenlingen’ genoemd. Ze zijn broos, gemakkelijk breekbaar en veel groter dan het eindproduct. Er zijn nog een paar stappen nodig voordat ze de uitstekende eigenschappen van industriële keramiek krijgen. Eerst wordt de lijm verwijderd in een chemisch proces. Vervolgens gaan ze naar de oven om gedurende twee dagen bij maximaal 1500 graden Celsius te sinteren. Tijdens dit proces krimpen ze tot 30 procent.
Dit volumeverlies is moeilijk te berekenen, vooral wanneer het doel is om de toleranties in het micrometerbereik te houden. Daarom worden veel onderdelen na het sinteren opgeschuurd om de vereiste toleranties te verkrijgen. Sommige onderdelen hoeven alleen maar te worden gepolijst voordat ze klaar zijn voor verzending.
Snelle productie van prototypes
De voordelen die de speciale eigenschappen van keramiek bieden, hebben tot gevolg gehad dat maxon veel meer produceert dan alleen delen voor overbrengingen. Zo worden er miniatuur spuitdoppen voor de industriële automatisering, pallen voor horloges en zelfs behuizingen voor koptelefoons gemaakt. maxon vervaardigt de behuizingen al jaren. Ze worden geacht een positief effect op de geluidskwaliteit te hebben. In tegenstelling tot metalen behuizingen zijn ze ook krasbestendig en houden ze lang hun mooie glans.
De basisprincipes van het poederspuitgieten zijn de afgelopen jaren grotendeels hetzelfde gebleven. Sommige dingen zijn echter veranderd. Volgens Andreas Philipp zal het gebruik van ‘groenlingen’ in de toekomst afnemen. In plaats daarvan worden eenvoudige basisvormen gegoten waarna deze met hightechapparatuur worden bewerkt tot ze de perfecte vorm hebben gekregen. “Zo krijgen klanten veel eerder een prototype,” zegt Andreas Philipp. Kleine partijen zijn dan ook sneller klaar voor verzending. Wat niet verandert, is de fascinatie voor poederspuitgieten die bij alle medewerkers aanwezig is. “Elke opdracht is anders, niets is routine. Keramiek is een extreem spannend materiaal. Dat maakt het zo interessant.”