maxon Inside
Keramiek op zijn best
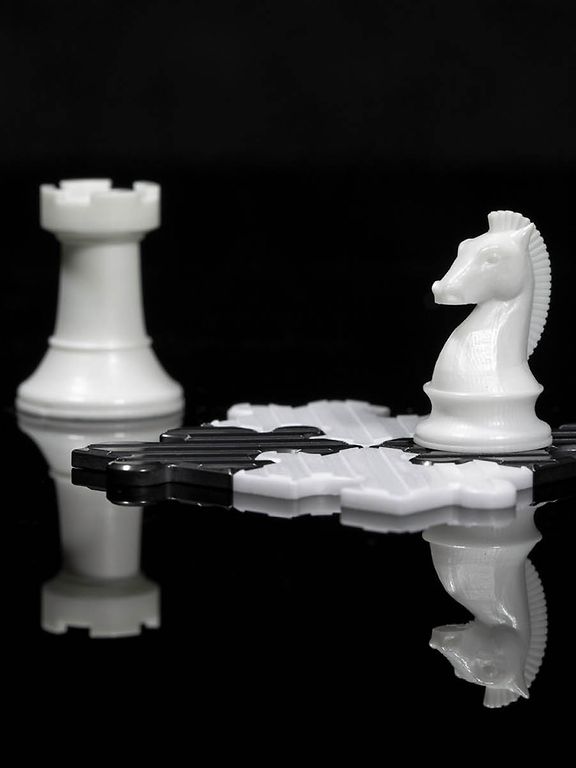
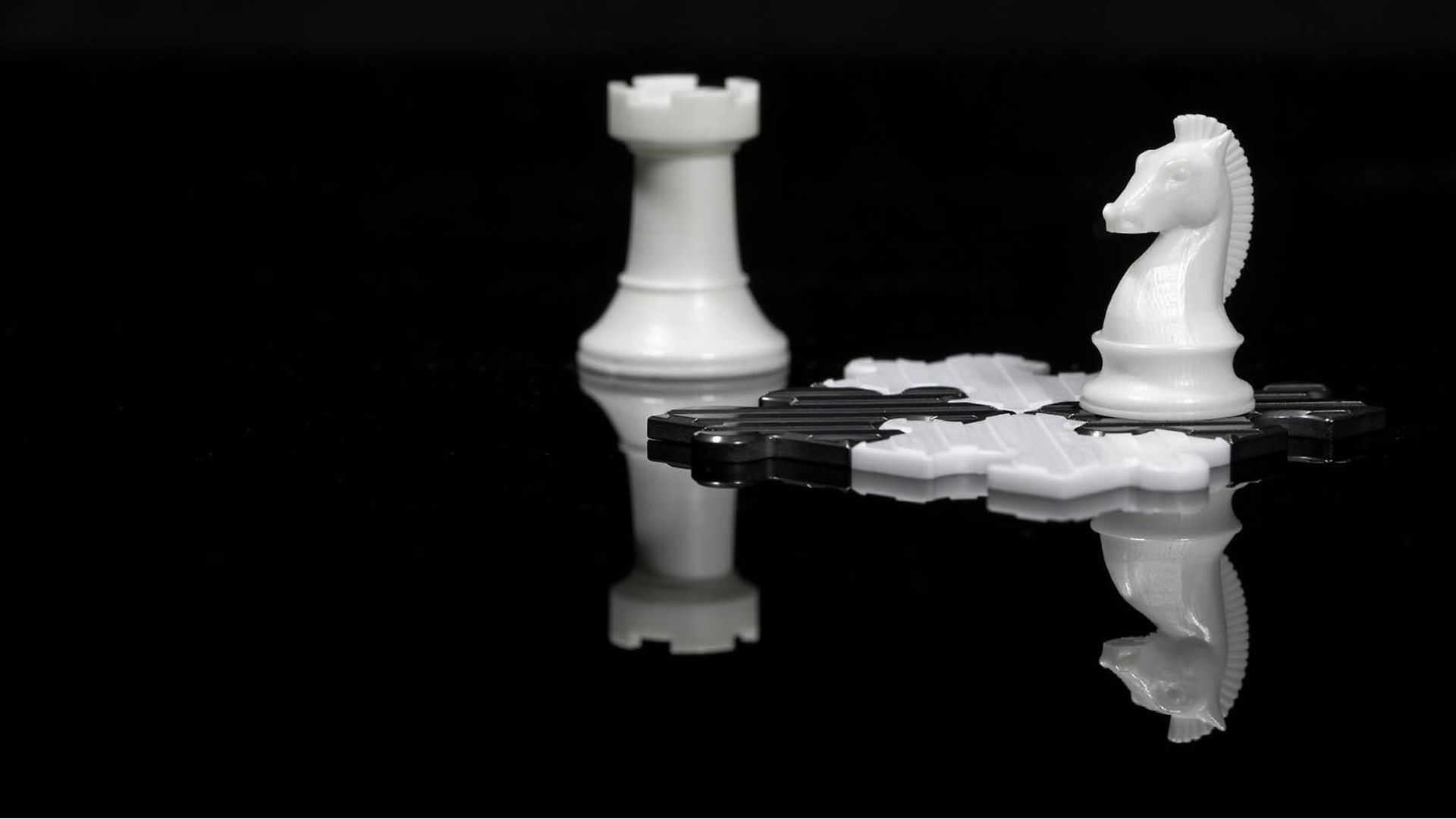
Additieve productie van keramische onderdelen versnelt de productie van prototype-onderdelen en opent nieuwe mogelijkheden.
Het Zwitserse bedrijf maxon staat bekend om zijn aandrijftechnologie die in verschillende Marsrovers van NASA is toegepast. Haar hightechafdeling voor technische keramiek in Sexau bij Freiburg is minder bekend. Hier worden keramische onderdelen nu ook in 3D geprint en met lasers geperfectioneerd.
“Wat is nog slijtvaster dan staal en kan worden verwerkt tot assen voor onze planetaire overbrengingen, om deze nog preciezer en betrouwbaarder te maken?” Dat is de vraag die medewerkers van aandrijfspecialist maxon motor GmbH zich meer dan 20 jaar geleden stelden. Stefan Zilm, hoofd Business Development & Quality Engineering bij het Competence Center CIM/MIM in Sexau weet het antwoord: keramische onderdelen die met behulp van keramisch spuitgieten worden vervaardigd. Dit is een proces dat vergelijkbaar is met het spuitgieten van metaal.
Tegenwoordig beschikt het bedrijf over een uitgebreide knowhow op het gebied van technische keramiek. Bij CIM kunnen componenten in serie worden geproduceerd, in aantallen van enkele tienduizenden stuks. Maar ondanks alle ervaring, en zelfs met het gebruik van de modernste engineeringmethodes zoals CAD, eindige elementenberekeningen en simulaties, blijft de realiteit de ultieme test die bepaalt of een nieuw idee deugt, en of een keramisch onderdeel überhaupt kan worden geproduceerd en zich gedraagt zoals gepland.
De gebruikelijke weg van idee tot echte keramische component is lang en kostbaar. Er is een dure matrijs nodig voor de te sinteren ‘groenling’. Vervolgens wordt hij in arbeidsintensieve processen gedraaid en gesneden, gesinterd en geschuurd. Zilm geeft toe: “Voor een eerste sample is dit proces behoorlijk ingewikkeld, het kost veel tijd en geld.”
Keramiek uit de printer
Maar er is nog een andere mogelijkheid: 3D-printen. Deze techniek die voor kunststofonderdelen al goed is ingeburgerd, wordt ook steeds vaker voor metalen gebruikt. Terwijl het bedrukken van plastic en metaal al enkele jaren deel uitmaakt van de industriële productie, staat het bedrukken van keramiek nog in de kinderschoenen: men is momenteel bezig om de laboratoriumresultaten in praktijksituaties in de fabriek te testen. Desalniettemin waren de voordelen zo verleidelijk dat maxon vijf jaar geleden al begon met pilottesten, met als doel prototypes van keramische componenten sneller bij de klanten te krijgen wat als echt pionierswerk kan worden beschouwd. Zilm: “Met zo’n printer kunnen de eerste twee tot drie iteraties van de ontwikkeling veel eenvoudiger en sneller worden doorlopen.”
Na intensief marktonderzoek koos maxon voor een printer van de Franse fabrikant 3Dceram. De printer werd speciaal aan de eisen van het bedrijf aangepast. “De belangrijkste aanschafargumenten voor ons waren de printerprecisie en het vrij grote printoppervlak van 300 bij 300 millimeter,” legt Zilm uit. De printer is gebaseerd op de stereolithografiemethode, waarbij een emulsie bestaande uit bindmiddel en keramisch poeder door laserlicht wordt gestold en een onderdeel zo laag voor laag wordt opgebouwd. De lagen zijn tussen 0,025 en 0,125 millimeter dik. Telkens wanneer een laag is aangebracht, gaat het printerbed één stap omlaag. Dit garandeert een gelijkmatige krimp tijdens het stollen, een hoge precisie en zeer nauwkeurige details. Een ondersteunende structuur is niet nodig. De bijzondere eigenschap van 3DCeram is dat ook miniatuuronderdelen met een volume van slechts 50 kubieke millimeter kunnen worden gemaakt.
Afhankelijk van de vereisten worden keramische onderdelen meestal gemaakt van zirkonium- en aluminiumoxiden. Dit zijn de basismaterialen voor technische keramiek die beide als emulsie voor de 3D-printer leverbaar zijn. De debinding- en sintertechnologie correspondeert met de CIM-procedure, zodat de groenlingen die in de 3D-printer zijn gecreëerd dezelfde productiesystemen kunnen doorlopen als de serieonderdelen. Afhankelijk van de complexiteit van het gewenste onderdeel en het vereiste tolerantieniveau zijn ook kleine series mogelijk. Ze vormen een goed alternatief voor keramisch spuitgieten (CIM).
Volgens Zilm heeft de procedure wel zijn beperkingen vanwege de diameter van de uv-laserstraal. Deze bepaalt welke minimale wanddikte kan worden geproduceerd. De componenten worden met perslucht en een additief gereinigd om het overtollige materiaal van het onderdeel te verwijderen. Gaatjes van 0,5 millimeter en kleiner kunnen niet zo perfect rond worden gemaakt als bij het spuitgieten, maar voor prototypes volstaat het meestal.
Ontwikkelingspartners vanaf het begin
Tegenwoordig stuurt de klant gewoon een bestand in het gestandaardiseerde STEP-formaat (Standard for the Exchange of Product model data) dat gemeengoed is geworden voor 3D-printen. Kort daarna ontvangt hij een offerte. Al na 10 tot 14 dagen na de orderbevestiging kan de klant al over de eerste prototype-onderdelen beschikken. “In het verleden duurde dit weken of zelfs maanden. Bovendien was het spuitgieten duur,” herinnert Zilm zich.
In het ideale geval betrekt de klant maxon er vanaf het begin bij. “We zijn er graag bij als het eerste idee ontstaat. Zo kunnen we het ontwerp beïnvloeden en het zo geschikt mogelijk maken voor keramiek,” legt Zilm uit. Zo is het bijvoorbeeld mogelijk verschillende componenten tot één component te combineren, waardoor je een component krijgt dat optimaal functioneert. Volgens Zilm zijn dergelijke verbeteringen heel belangrijk, aangezien de prijs voor een kilogram van de voor keramiek benodigde grondstoffen ongeveer het tienvoudige is van die van staal. “We moeten dit compenseren door een aanzienlijk betere functionaliteit te bieden, bijvoorbeeld door slijtvastheid, temperatuurstabiliteit of de overbodigheid van smeermiddelen.”
Maar de grenzen van additieve productie zijn nog niet bereikt. Andreas Philipp, chef van het Competence Center CIM/MIM, weet het zeker: “We moeten in 3D gaan denken en niet op de klassieke manier zoals vroeger.” Dan openen zich volledig nieuwe mogelijkheden, zodat 3D-printen een heel goed alternatief kan zijn voor de beproefde processen.