maxon Story
De vierde industriële revolutie

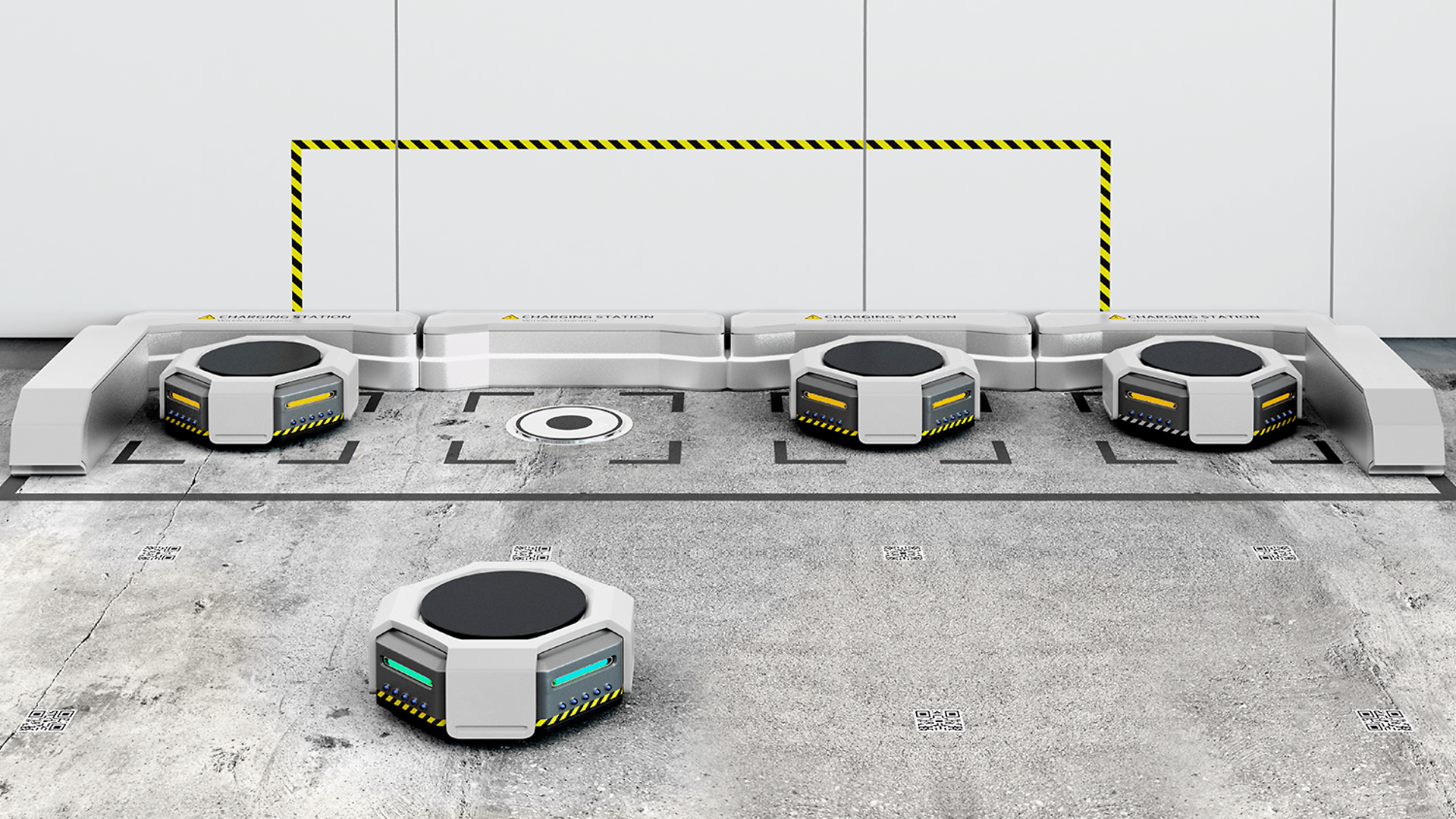
De wereld heeft sinds 1760 drie industriële revoluties meegemaakt, en nu staan we aan de vooravond van de vierde industriële revolutie: Industrie 4.0, ook wel bekend als Smart Industry. Laten we eens kijken wat deze veranderingen betekenen voor het bedrijfsleven en de beroepsbevolking.
Tussen 1760 en 1840 werd bij de eerste industriële revolutie omgeschakeld van handmatige productie naar het gebruik van stoom en waterkracht.
In de periode tussen ongeveer 1871 en 1914 kwam de tweede industriële revolutie tot stand door de grootschalige aanleg van spoorwegen en de elektrificatie van fabrieken. Het was ook het begin van telecommunicatienetwerken die een snellere overdracht van ideeën mogelijk maakten en tot de eerste moderne productielijnen leidden.
De derde revolutie was de digitale revolutie aan het einde van de 20e eeuw met de uitvinding van computers. Machineoperators konden de computers programmeren waardoor repetitieve mechanische taken automatisch konden worden uitgevoerd. Hierdoor steeg de productie enorm en daalden de arbeidskosten.
We staan nu aan het begin van de vierde industriële revolutie, ook wel bekend onder de namen digital manufacturing, Industrial Industry of Things (IIoT) en Industrie 4.0. Wat houden deze veranderingen in voor het bedrijfsleven en het personeel?
Wat zijn de uitdagingen voor Industrie 4.0?
Zoals bij elke revolutie moeten er politieke, economische, organisatorische en sociale uitdagingen worden overwonnen. Politiek: gezamenlijke regelgeving en juridische kwesties. Economisch: implementatie tegen hoge kosten ten voordele van eerstewereldlanden. Organisatorisch: betrouwbaarheid, beveiliging en veiligheid, IP-bescherming en opleiding van het personeel. En sociaal: zorgen over privacy en wantrouwen in het toezicht, onwil onder huidige medewerkers vanwege angst voor verandering en werkzekerheid.
De nieuwste revolutie leidt tot automatisering van de gegevensuitwisseling: geavanceerde mens-machine-interfaces met realtime communicatie. Deze snelheid zorgt in combinatie met big data en digitale verwerkingsplatforms voor meer transparantie voor de operator. De operator bakent de overkoepelende taak af en verbetert deze terwijl de systeemcomponenten zichzelf autonoom monitoren. Dit resulteert in een enorme flexibiliteit waarbij machines storingen voorspellen en onderhoud uitvoeren en plannen voordat er sprake is van een probleem. Bedrijven kunnen aanzienlijk op de kosten besparen door de stilstandtijd te verkorten, de algehele efficiëntie te vergroten en het personeelsbestand in te krimpen. De medewerkers zullen echter op hun hoede zijn en zich zorgen maken over hun baan. Bij elk automatiseringsproject in de geschiedenis van de industriële revolutie zijn sommige banen overbodig geworden. De nieuwe banen die door innovatie ontstaan, vereisen echter andere vaardigheden waardoor mensen moeten worden omgeschoold.
Hoe zou dit eruit zien?
Voor elke bedrijfstak geldt dat er enorme mogelijkheden zijn. Laten we eens kijken hoe de fabriek van morgen eruit zou kunnen zien.
Machine learning
Autonome mobiele robots (AMR) kunnen op verschillende dagen op verschillende routes hun werk doen, afhankelijk van de vraag in magazijnen en de intralogistiek. Ze hebben een aantal sensoren waarmee ze om andere robots en mensen heen kunnen navigeren. En als ze onderhoud nodig hebben, stellen de AMR’s zelf een diagnose en gaan ze uit eigen beweging naar de werkplaats voor preventief of kritisch onderhoud.
Slimme fabriek
Industrie 4.0 omvat ook de ‘slimme fabriek’ die gebruik maakt van cyber-fysieke systemen (CPS). Een CPS bestuurt een mechanisme op basis van een computergebaseerd algoritme en is gekoppeld aan het internet der dingen, waarbij apparatuur met sensortechnologie uitsluitend via internet gegevens uitwisselt. Voorbeelden van CPS zijn zelfrijdende auto’s en drones die zich virtueel van hun omgeving bewust zijn. In plaats van magazijnen en fabrieken die leveringen lossen met een door mensen uitgevoerde keten, kan een vrachtwagen op basis van geautomatiseerde gegevensverzameling precies de gewenste hoeveelheid grondstof leveren. Producten worden digitaal ontwikkeld en getest. De slimme fabriek functioneert van toelevering tot eindproduct met een minimum aan toezicht.
Onze klanten bevinden zich vaak in de voorhoede van deze transformatie en we zien het als een spannende uitdaging om producten te ontwikkelen en te produceren die innovatie blijven stimuleren.
Om AGV- en AMR-ontwerpers maximale vrijheid te bieden, heeft de maxon Group een complete serie compacte en modulaire motoren ontwikkeld. Deze Deze IDX-aandrijfoplossingen voldoen aan de strengste eisen: ze bieden 20% hogere prestaties dan de huidige oplossingen op de markt.