Expert Blog
Sobre a eficiência dos componentes do acionamento
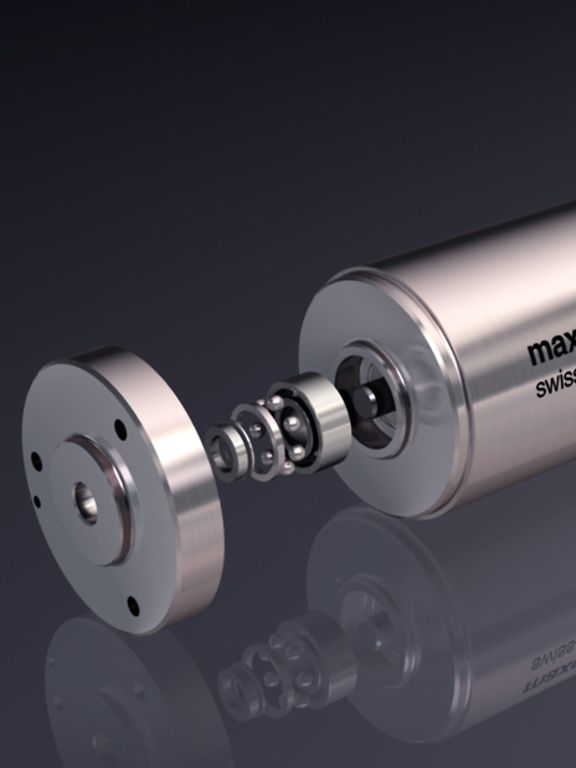
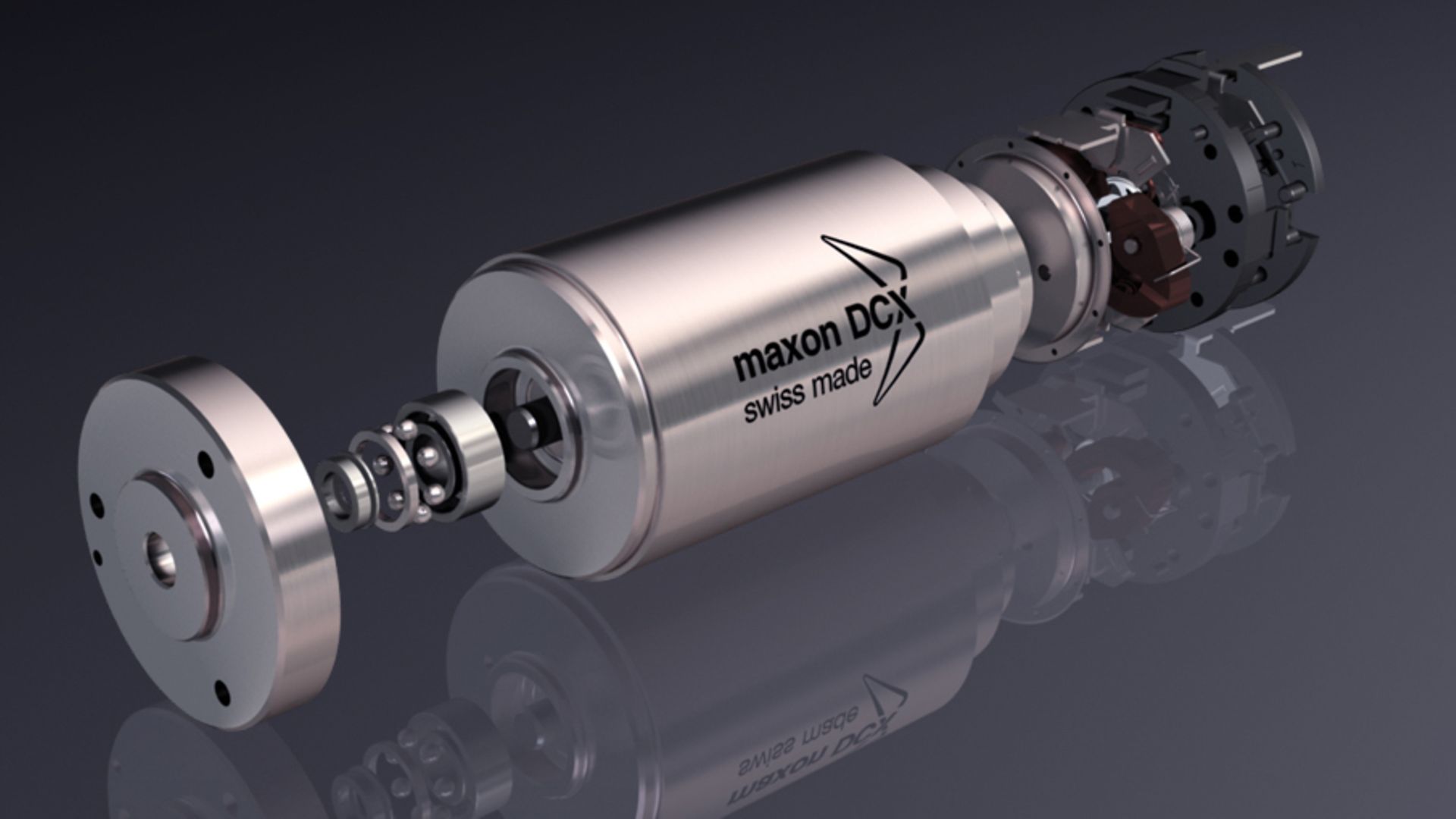
Frequentemente, surgem questões quanto ao motor que apresenta a maior eficiência. Em especial, quando falamos sobre aplicações com fontes de alimentação limitadas, tais como ferramentas a bateria ou satélites alimentados por painéis solares. Creio que vale a pena alargar a questão ao sistema de acionamento completo, que consiste no sistema de controlo, motor, redutor e outros sistemas mecânicos. A tabela 1 apresenta uma estimativa aproximada sobre as habituais eficiências dos diferentes dispositivos de conversão de energia.
Constatamos que muito depende de como o sistema mecânico é concebido. Uma elevada fricção no sistema mecânico custa muita energia. Portanto, a otimização da eficiência de uma unidade de acionamento deve começar sempre pelo sistema mecânico.
É importante lembrar que os sistemas de acionamento DC são muitas vezes alimentados por uma tensão fixa. Consequentemente, não é realmente a eficiência global que tem de ser maximizada. A eficiência é um parâmetro relativo que indica as perdas por potência de entrada. Contudo, a uma tensão fixa, é o consumo de corrente (como um parâmetro absoluto) que tem de ser minimizado. Uma utilização adequada da tensão de alimentação total reduz o consumo de corrente — e aumenta a vida da bateria.
De seguida apresentamos algumas regras para uma alta eficiência e baixo consumo de corrente.
Regras para a transformação mecânica
- Utilizar mecânica de baixa fricção ou não utilizar mecânica de fricção.
- Utilizar fricção de rolamento (coeficiente de fricção < 0,01) em vez de fricção de deslize (coeficientes de fricção típica de 0,1 … 0,4). Por exemplo, um sistema de fuso de esferas tem uma fricção consideravelmente inferior ao fuso roscado. Contudo, uma solução de fuso de esferas normalmente não dispõe de autobloqueio, pelo que necessita de ser alimentada para permanecer na posição de paragem. Considerando todo o ciclo de trabalho, existem situações em que um fuso trapezoidal pode consumir menos energia no total.
Regras para redutores de engrenagens de dentes retos e planetários
- Utilizar um número reduzido de estágios.
- Utilizar redutores pequenos com um binário nominal apenas ligeiramente superior ao binário necessário. Não utilizar um redutor de grandes dimensões. A eficiência a uma carga reduzida do redutor é bastante insatisfatória.
- Em termos de eficiência, um motor de acionamento direto maior sem redutor é muitas vezes melhor do que uma combinação de motor/redutor. No entanto, o acionamento direto pode ser maior, mais pesado e mais dispendioso.
Regras para motores
- Operar os motores a velocidades de vários milhares de rpm.
- Não escolher um motor demasiado grande. Não operá-lo com uma carga perto de zero.
- Prestar atenção ao selecionar o enrolamento. Utilizar um motor que tire o melhor proveito da tensão para atingir a velocidade sob carga; esse será o motor que necessita da menor corrente.
Regras para sistemas de controlo
Neste caso, as regras são semelhantes às dos redutores. Colocá-los a uma carga adequada e não operá-los a uma corrente demasiado baixa. Não escolher sistemas de controlo com uma corrente nominal demasiado elevada. Combinar a dimensão do estágio de potência com a corrente motora necessária.
E por último
Utilizar adequadamente a tensão de alimentação total. Isto reduz o consumo de corrente, permitindo-lhe poupar dinheiro: irá necessitar de uma menor fonte de alimentação, menor sistema de controlo, menos blindagem de cabos... Ou como um colega meu diria: a tensão é gratuita — a corrente não.