maxon Inside
Wenn alle anderen Materialien versagen...
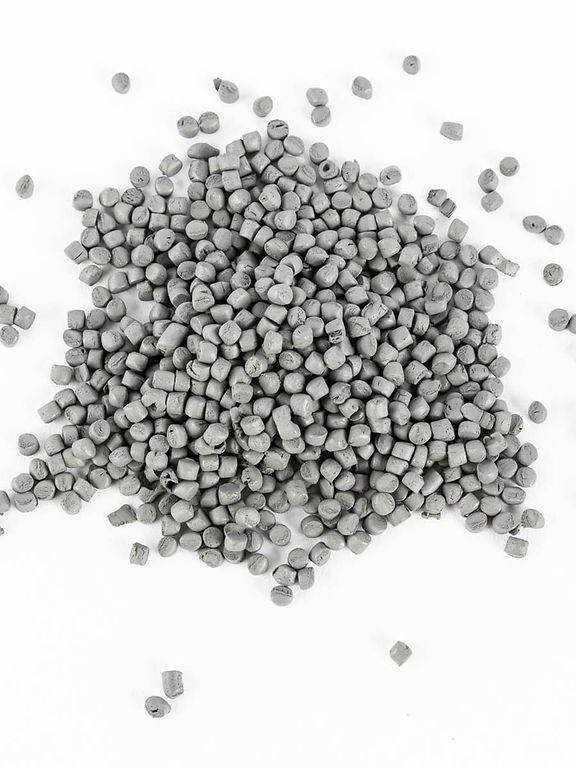
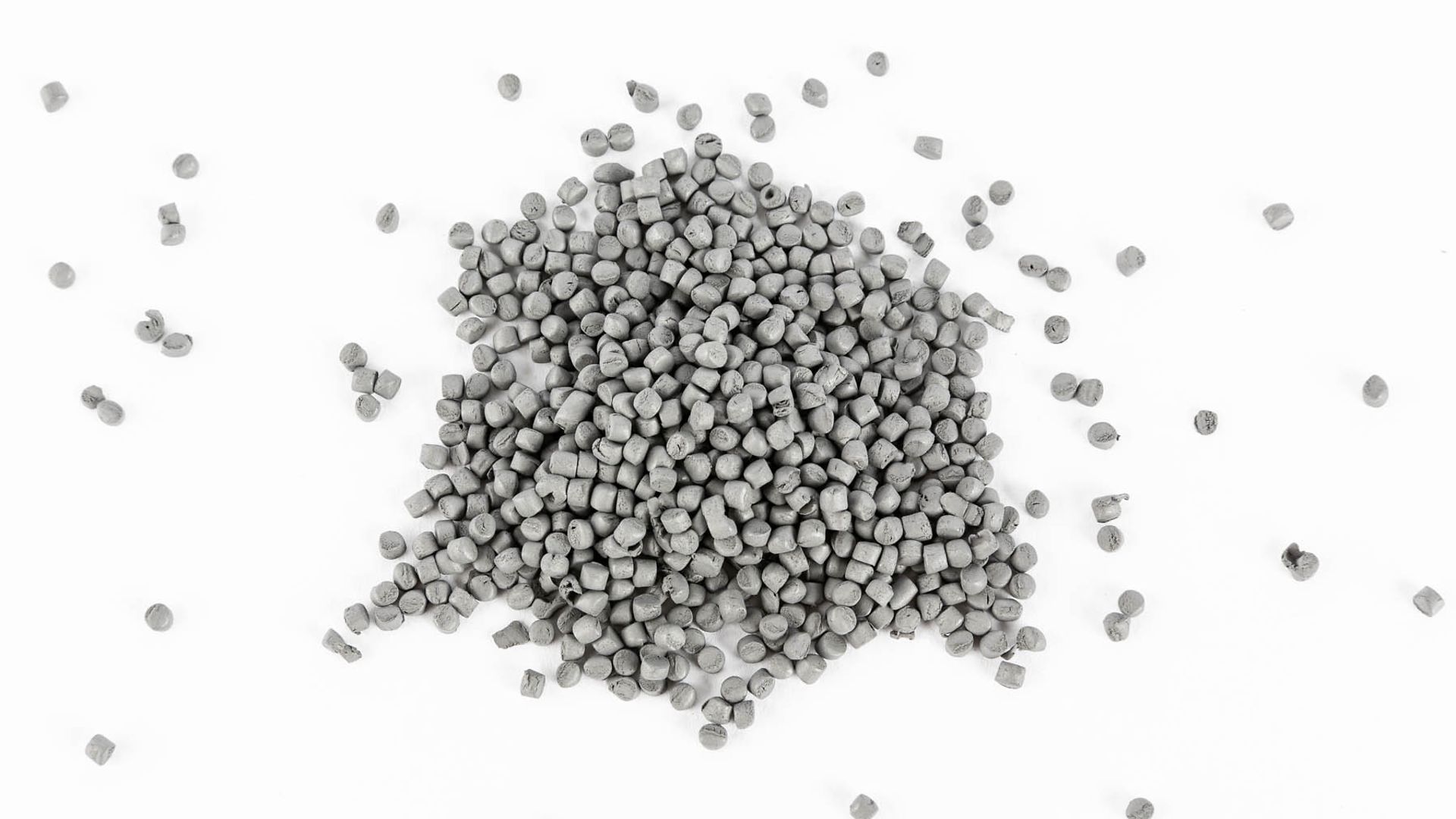
Auf der ganzen Welt ist maxon für seine hochpräzisen Antriebe bekannt. Doch nur wenige wissen, dass das Unternehmen eine eigene Spritzgussabteilung für Keramik und Metall unterhält. Hier werden nicht nur Keramikspindeln produziert sondern auch Spezialteile für die Uhren- und Musikindustrie. Keramik ist ein hervorragendes Material, um Getriebe zu verstärken. Aus diesem Grund hat maxon bereits vor 20 Jahren eine eigene Pulverspritzguss-Abteilung gegründet. Heute werden dort auch Keramikteile produziert, die für ein besseres Musikerlebnis sorgen.
Der grösste Stolz der Abteilung bekommt dabei ein eigenes Zimmer. Andreas Philipp, Leiter der Abteilung Pulverspritzguss bei maxon, steuert schnurgerade auf die neu hochgezogenen Mauern hin, öffnet die Türe und zeigt auf die einzige Maschine, die im Raum untergebracht ist – eine Lasermaschine zur Hartbearbeitung von Keramikbauteilen. Die neuste Anschaffung ist in der Lage, Keramik auf 2 Mikrometer genau zu schneiden, erklärt Philipp. Federelemente mit einer Wandstärke von 17 Mikrometer bearbeiten und gleichzeitig präzise Messungen durchführen: damit soll die Abteilung fit für die Zukunft gemacht und Kunden noch schneller mit Präzisionsteilen beliefert werden.
Keramik für längere Lebensdauer
Dass maxon überhaupt eine eigene Spritzguss-Abteilung für Keramik und Metall betreibt, dürften nur wenige Leute wissen, schliesslich ist das Unternehmen hauptsächlich für seine Mikromotoren bekannt, die auf dem Mars im Einsatz sind, aber auch auf der Erde unzählige Anwendungen antreiben – von Operationsrobotern über Laborautomaten bis hin zu Tätowiermaschinen.
Doch neben Präzisionsantrieben entwickelt und produziert maxon auch Steuerungen, Encoder und vor allem Getriebe. Und diese – oder genauer gesagt: deren einzelne Komponenten wie etwa Zahnräder, Achsen oder Planetenträger – müssen für bestimmte Einsätze verstärkt werden. Für diese «Aufrüstung» eignet sich Keramik besonders, schliesslich ist das Material im Vergleich zu Stahl beständiger gegen Chemikalien und hohe Temperaturen und ist ausserdem extrem hart. Keramikachsen in Getrieben verlängern deren Lebensdauer beträchtlich. Besonders, wenn der Antrieb im Start-Stopp-Betrieb eingesetzt wird. Aus diesem Grund hat maxon vor rund zwanzig Jahren begonnen, die Keramikteile selbst herzustellen. Heute arbeiten in der Spritzgussabteilung etwa 45 Personen, darunter Entwickler:innen, Applikationsingenieur:innen, Qualitätsfachleute und Produktionsmitarbeitende.
Vom Motor bis zur Spindel
Die Pulverspritzguss-Fachleute sind Teil des maxon Produktionswerkes im süddeutschen Sexau, welches sich auf Getriebe spezialisiert hat. Rund die Hälfte aller Teile, die die Abteilung verlassen, werden in maxon Antrieben eingesetzt. Besonders begehrt sind die Keramikspindeln für Linearantriebe, da sie leichtgängig und verschleissfest sind. «Wir sind das einzige Unternehmen, das dem Kunden Motor, Getriebe und Keramikspindel aus einer Hand bieten kann», erklärt Andreas Philipp. Die Entwicklung und Produktion von präzisen Keramikbauteilen ist nicht ganz billig. Die Prozesse sind komplex und für die Hartbearbeitung werden Diamantwerkzeuge oder – wie bereits erwähnt – Lasermaschinen benötigt. Deshalb wird Keramik meistens nur aufgrund von sehr spezifischen Anforderungen gewählt, die mit herkömmlicheren Werkstoffen nicht erfüllt werden können. Oder wie es Andreas Philipp ausdrückt: «Keramik kommt zum Einsatz, wenn alle anderen Materialien versagen.»
Zwei Tage in den Ofen
Am Anfang des Produktionsprozesses steht das Granulat, auch Feedstock genannt. Dieses beinhaltet einen bestimmten Anteil an Bindemittel, damit das Material überhaupt in Gussformen gepresst werden kann. Nachdem die Teile dann die Spritzgussmaschine verlassen haben, können sie bereits leicht bearbeitet werden. Mit fertigen Keramikkomponenten haben sie aber noch nicht viel gemein. Diese so genannten Grünlinge sind spröde, leicht zerbrechlich und viel grösser als das Endprodukt. Damit sie die herausragenden Eigenschaften industrieller Keramik erhalten, sind ein paar weitere Schritte nötig. Zuerst wird ihnen in einem chemischen Verfahren das Bindemittel wieder entzogen. Danach geht es für zwei Tage in den Ofen zum Sintern, wo die Bauteile bei maximal 1500 Grad Celsius um bis zu 30 Prozent schrumpfen.
Dieser Volumenverlust lässt sich nur schwer kalkulieren, besonders wenn Toleranzen im Mikrometerbereich das Ziel sind. Aus diesem Grund werden viele Bauteile nach dem Sintern geschliffen, um die geforderten Toleranzen zu erreichen. Bei manchen Komponenten reicht auch ein einfaches Polierverfahren, und danach sind sie bereit zur Auslieferung.
Schnelle Herstellung von Prototypen
Weil die besonderen Eigenschaften von Keramik einige Vorteile bieten, fertigt maxon damit nicht nur Bauteile für Getriebe an. Zu den gefertigten Produkten zählen auch kleinste Düsen für die Industrieautomation, Klinken für die Uhrenindustrie aber auch Gehäuse für Kopfhörer. Letztere werden bereits seit Jahren im maxon Werk hergestellt und haben laut Hersteller einen positiven Effekt auf die Klangqualität. Zudem sind sie im Gegensatz zu Metallgehäusen kratzfest und behalten ihren schönen Glanz über eine lange Zeit.
Das Grundprinzip in der Pulverspritzguss-Verarbeitung ist in den letzten Jahren im Grossen und Ganzen gleich geblieben. Trotzdem sind gewisse Veränderungen spürbar. Laut Andreas Philipp wird wohl in Zukunft die Bearbeitung von Grünlingen abnehmen. Stattdessen geht man vermehrt dazu über, einfache Grundformen zu spritzen und diese danach mit Hightech-Maschinen zu bearbeiten, bis sie die perfekte Form haben. «Dadurch erhalten die Kunden viel schneller einen Prototypen», sagt Andreas Philipp. Auch Kleinserien können rascher ausgeliefert werden. Was sich nicht verändert, ist die Faszination für Pulverspritzguss, die in der gesamten Abteilung spürbar ist. «Jeder Auftrag ist anders, nichts ist Routine. Keramik ist ein massiv herausforderndes Material und genau das macht es so spannend.»