maxon Inside
Kein Zutritt für Bakterien
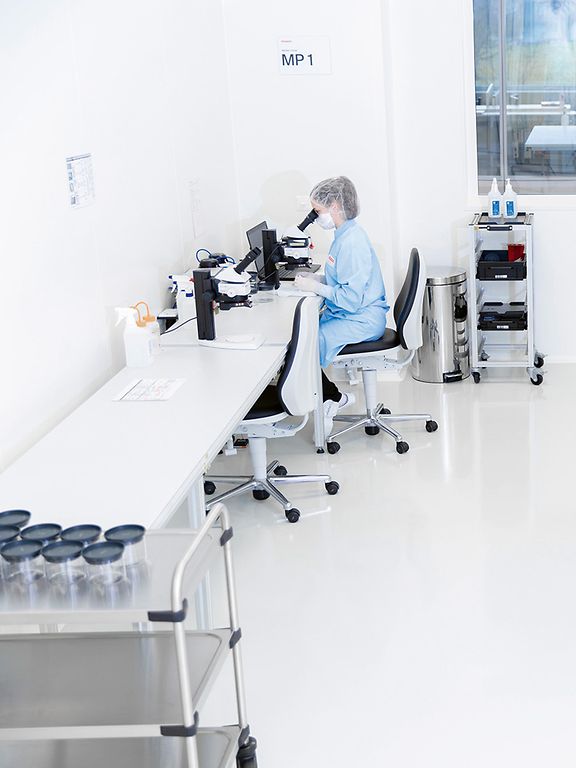
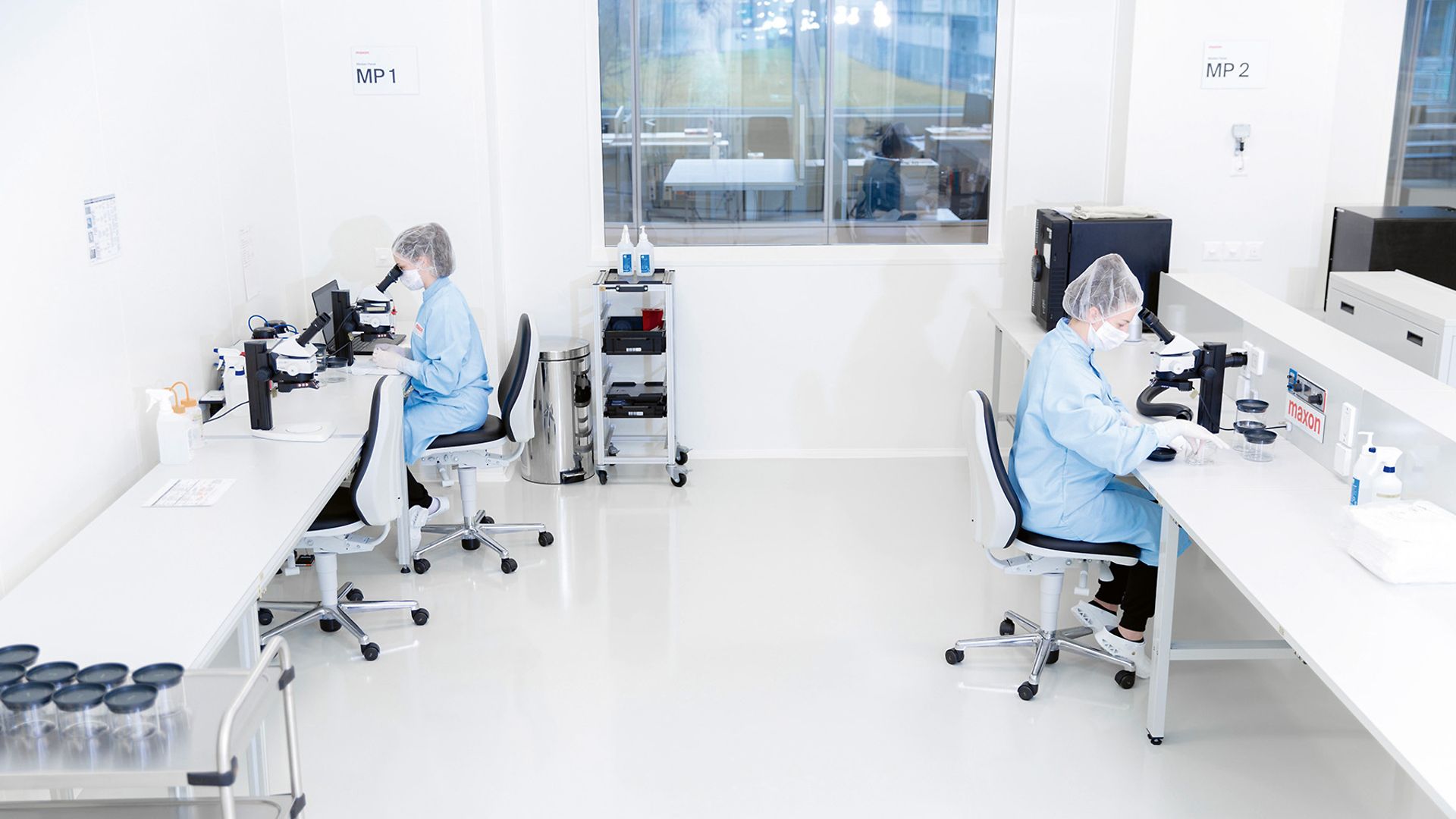
Kleinste Antriebssysteme für den Einsatz im menschlichen Körper müssen in einer reinen Umgebung gebaut werden, frei von mikrobiologischer Verschmutzung. Willkommen im GMP-Reinraum von maxon, wo Disziplin und Gelatine aufeinandertreffen.
Hinter der Glasscheibe, im weissen, lichtdurchfluteten Raum, ist die Welt ganz anders als in den restlichen Produktionsbereichen der maxon Group. Hier, am Hauptsitz des Antriebsspezialisten, zwischen Bergen und Seen, befindet sich seit kurzer Zeit ein Produktionsbereich für Antriebe für medizinische Anwendungen. Die Partikelkonzentration in der Luft ist gering und wird kontinuierlich überwacht. Eine saubere Umgebung. Und in den meisten Fällen absolut ausreichend. Denn Motoren für Insulinpumpen, medizinische Dosiergeräte usw. müssen nicht zwingend frei von Keimen und Bakterien sein.
Wenn es allerdings um Anwendungen in der Hightech-Medizin geht, etwa um implantierbare Antriebssysteme, sieht die Sache anders aus. Dann wird der Zusammenbau in den neu eingerichteten GMP-Bereich (Good Manufacturing Practice) verlagert. In dieser Reinraumklasse wird neben der Partikelkonzentration auch die mikrobiologische Kontamination von Oberflächen sowie der Luft gemessen und auf Spuren von Bakterien, Pilzen und Sporen untersucht. Es ist eine klinische Umgebung, die hohe Anforderungen an die Belüftungstechnik, die Instrumente und vor allem die Menschen stellt, die sich darin bewegen.
Disziplin ist das A und O der Reinheit
Wer in dieser Umgebung arbeitet, muss sich konsequent an die gleichen, strengen Prozesse und Vorschriften halten. Die zwei Produktionsmitarbeiterinnen Albane Lloqanaj und Ruth Da Silva ziehen sich spezielle Hosen und Oberteile an, die vakuumiert von einer Reinraumwäscherei angeliefert wurden und dank Hightech-Materialien antibakteriell sind. Hinzu kommen eine spezielle Hygienemaske, Haarnetz, Handschuhe, ein Arbeitskittel und Schuhe, die antistatisch sind.
Zudem müssen die Hände mit hautfreundlichem Desinfektionsmittel im sechs-schrittigen hygienischen Händedesinfektionsverfahren mindestens 30 Sekunden lang desinfiziert werden. Die Handschuhe werden anschliessend mit reinem Alkohol desinfiziert, der rückstandslos verdunstet. So kann gewährleistet werden, dass weder Partikel noch Keime an den Handschuhen haften bleiben. All diese Prozessschritte erfolgen in einer definierten Reihenfolge. Zudem muss sichergestellt werden, dass keine verschmutzte Luft von aussen in den GMP-Raum eindringt. Dazu müssen drei Zonen durchschritten werden, die durch automatisierte Schleusentüren getrennt sind. Öffnen lässt sich jeweils nur eine Türe, denn je weiter man vordringt, desto höher wird der Luftdruck im jeweiligen Raum.
Im Reinraum
Auch im Reinraum selbst benötigen die Arbeiter:innen strikte Disziplin. Sie dürfen sich zum Beispiel nicht ins Gesicht fassen. Und wenn, dann nur bewusst, sodass sie sofort wieder die Handschuhe desinfizieren können. «Ich mag diese Art von Arbeit sehr, denn sie ist herausfordernd, abwechslungsreich und verantwortungsvoll. Wir dürfen uns keine Fehler erlauben, wenn unsere Antriebe für implantierbare Systeme verwendet werden», erläutert Produktionsmitarbeiterin Albane Lloqanaj. Das bedeutet auch, dass man mit Fehlern offen umgehen muss. Teamleiter Stefan Kathriner erklärt: «Es ist wichtig, dass wir uns sofort gegenseitig ansprechen, wenn etwas komisch erscheint oder wir einen Fehler vermuten. Eine Kritik ist nie persönlich, sondern immer objektiv.»
Um sicherzugehen, dass Arbeitsoberflächen und Luft ein gewisses Mass an Keimen oder Bakterien nicht überschreiten, führt maxon regelmässig Tests mit einer nährstoffreichen Gelatine durch. Diese sogenannten Agar-Platten werden von den Produktionsverantwortlichen auf Flächen gedrückt oder offen stehengelassen. Da die Gelatine als Nährboden für Mikroorganismen dient, sieht man nach 72 Stunden im Inkubator mit blossem Auge, ob eine Kontamination vorliegt und wie hoch sie ist.
Der Aufwand für den Betrieb einer solchen GMP-Umgebung ist beachtlich, weshalb bislang nur wenige, spezielle Kundenaufträge für implantierbare Systeme dort bearbeitet werden. Die Reinraum-Spezialist:innen bei maxon haben aus diesen Projekten in den vergangenen Jahren viel gelernt. Stefan Kathriner sagt: «Wir besitzen ein umfangreiches Know-how und hoffen darauf, in Zukunft vermehrt Kundenaufträge dieser Art bearbeiten zu dürfen.»
Weitere Informationen zu Antriebssystemen für die Medizintechnik finden Sie auf unserer Website unter medical.maxongroup.com
Image Copyrights
maxon/Philipp Schmidli