Expert Blog
Encoder-Wahl – Teil 1: Eigenschaften
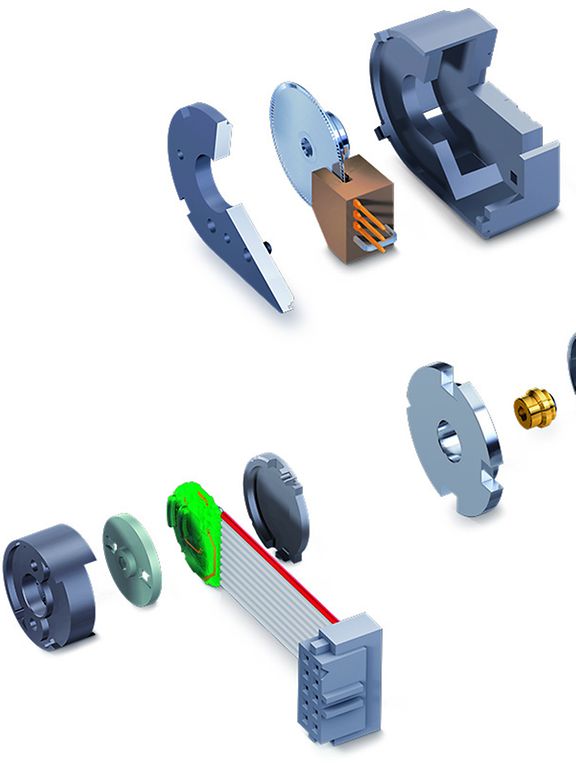
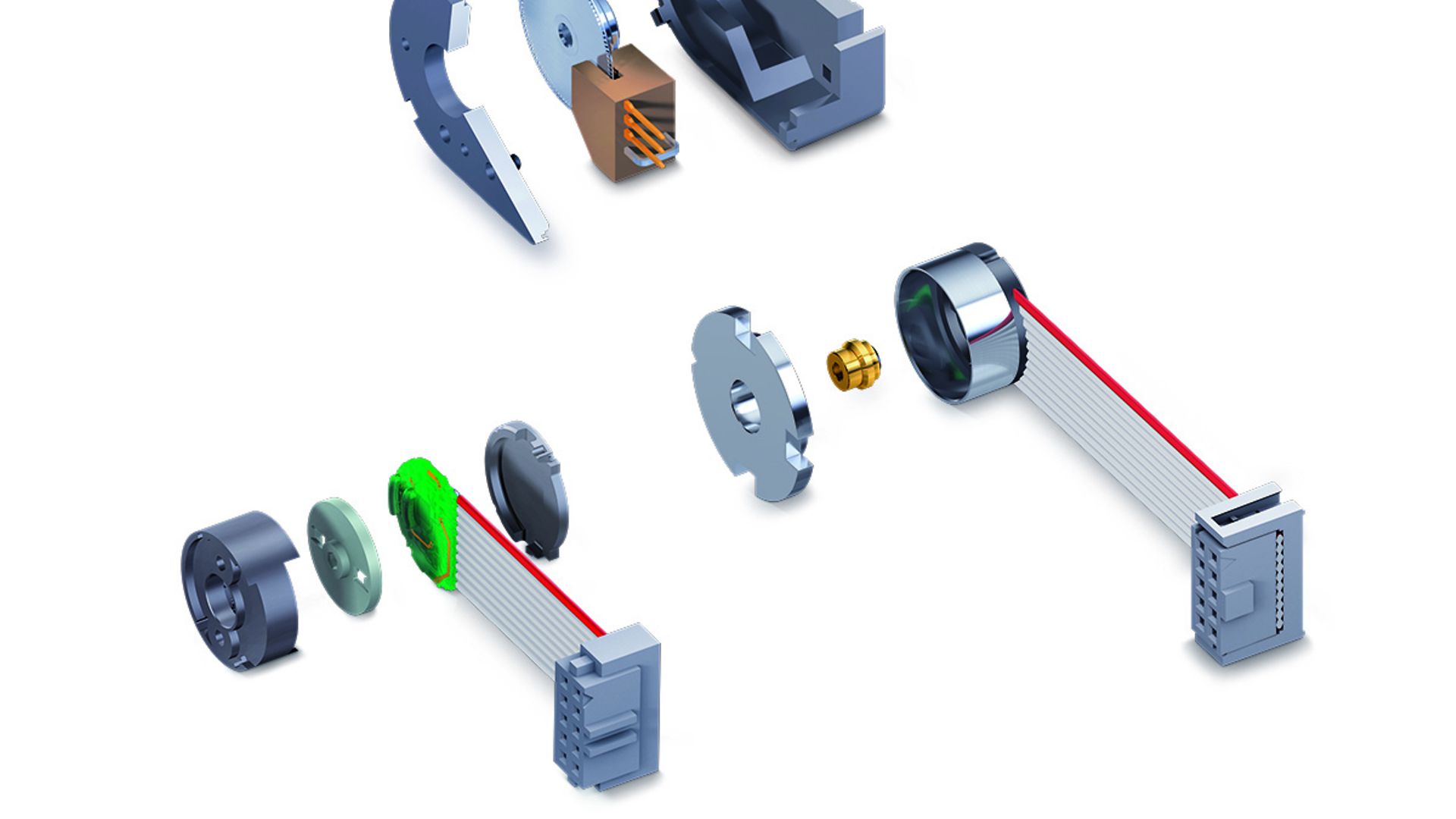
Wie wählen Sie den richtigen Encoder für Ihre Applikation aus? Dieser Blogeintrag hat die Antworten.
Der bevorzugte Feedback-Sensor für viele Applikationen mit kleinen Motoren ist der digitale Inkremental-Encoder. Diese Blogreihe startet mit einer Betrachtung der wichtigsten Encoder-Eigenschaften, bevor wir uns genauer mit der Auswahl für Anwendungen der Positions- und Drehzahlregelung befassen.
Typischen Anforderungen
Jede Applikation ist anders. Die Hauptaufgabe besteht möglicherweise in der Positionsregelung oder der Drehzahlregelung. Der Grad an Genauigkeit kann in der Drehzahl- oder Positionsregelung sehr unterschiedlich ausfallen und sollte deshalb bereits vor der Wahl des Encoders festgelegt werden. Die Drehzahlregelung bei niedrigen Drehzahlen (unter 100 min-1) benötigt akkurateres Feedback als die Drehzahlregelung bei hohen Drehzahlen (1 000 min-1 und höher).
Die Last kann direkt mit dem Motor gekuppelt werden oder es liegt ein mechanisches Transformationssystem vor, z. B. ein Getriebe oder eine Schraube. Encoder werden normalerweise auf der Motorwelle montiert, können aber auch an der Last selbst angebracht werden. Die mechanischen Eigenschaften des Transformationsmechanismus beeinflussen die Encoder-Wahl: Getriebeuntersetzung und mechanisches Spiel müssen berücksichtigt werden.
Die Umgebungsbedingungen, wie Temperatur, Vibration, elektromagnetische Störungen, wirken sich ebenso auf die Wahl des Encoders aus. Optische Encoder müssen z. B. gegen Staub geschützt werden. Magnetische Encoder können empfindlich auf externe Magnetfelder – einschliesslich denen des Motors – reagieren und benötigen ggf. eine Abschirmung.
Haupteigenschaften von Inkremental-Encodern
Die charakteristische Grösse eines Inkremental-Encoders ist die Anzahl der Rechteckimpulse pro Motorumdrehung. Üblicherweise liefern zwei Kanäle die gleiche Anzahl an Impulsen. Die beiden Signale sind um eine Viertelsignallänge gegeneinander phasenverschoben. Dieser Aufbau ermöglicht die Erkennung der Motordrehrichtung und führt zu 4 ausgeprägten Zuständen pro Impuls. Manchmal werden diese Zustände auch Quadcounts genannt. Sie stellen die reale Auflösung dar, die viermal höher ist als die Anzahl der Impulse pro Kanal. Bei einem Encoder mit 1 000 cpt («counts» oder Impulsen pro Umdrehung) ergibt dies 4 000 Zustände pro Umdrehung oder eine nominelle Auflösung von 360°/4 000 = 0,09°.
Bitte beachten: Wenn über die Auflösung eines Encoders gesprochen wird, sollte geklärt werden, dass alle über das Gleiche sprechen: die Anzahl der Impulse pro Kanal (cpt) oder die Anzahl der Zustände (Quadcounts).
Die Encoderauflösung kann grosse Unterschiede aufweisen. Von dem sehr einfachen Wert von 1 cpt (oder 4 Zuständen) eines Encoders, der lediglich zur Erkennung von Bewegung eingesetzt werden kann, bis hin zu mehreren 10 000 cpt für ein hochakkurates Positions- oder Drehzahl-Feedback. Viele Faktoren beeinflussen die erzielbare Encoderauflösung: das zugrunde liegende physikalische Prinzip (optisch, magnetisch, induktiv, ...), der vorrangige Signaltyp (analog oder digital), die Signalverarbeitung (z. B. Interpolation) und das mechanische Layout, um nur ein paar zu nennen. In diesem Blogeintrag dreht es sich allerdings nicht um Encoder-Design, sondern darum, wie geeignete Encoder besondere Steuerungsanforderungen einer Applikation erfüllen können.
Genauigkeit von Encodern
Die Auflösung – die Anzahl der Zustände – bedingt die nominelle Genauigkeit. Die Position wird bis auf einen Encoder-Quadcount (qc) genau erreicht. Encoder-Impulslängen können aufgrund von mechanischen Toleranzen (z. B. Wellenrundlauf, Länge der magnetischen Pole) jedoch sehr unterschiedlich ausfallen. Die Impulse in einem Motorumdrehungsbereich können kürzer als die Impulse anderer Bereiche sein. Die gemessene Position weicht daher periodisch über eine Motorumdrehung hinweg von der realen Position ab.
Ein Beispiel der gemessenen Nichtlinearität eines magnetischen, interpolierten Encoders mit 256 cpt. Die Abweichung der perfekten Position wird als Funktion des Encoder-Signals (1 024 Quadcounts) dargestellt. Das Diagramm setzt sich aus 25 Messungen einer Umdrehung zusammen. Sie können deutlich erkennen, wie sich die Abweichung nach einer Umdrehung wiederholt. Die Abweichung von der durchschnittlichen Absolutposition beträgt ca. +/-0.45° bzw. ca. 0.9° hinsichtlich der INL. An einer beliebigen Encoderposition beträgt die Signalstörung (Jitter) ca. 0.3°. Dies entspricht ziemlich genau einer Abweichung von 1 Zustand (360°/1 024 = 0.35°).
Die maximale Abweichung (Spitze zu Spitze) wird integrale Nichtlinearität (INL) genannt. INL ist wichtig für Applikationen, die absolute Positionsgenauigkeit erfordern. Die Wiederholbarkeit – d. h. immer die gleiche Position für einen bestimmten Sollwert zu erreichen – wird von INL nicht beeinflusst. Die Wiederholbarkeit ist eher eine Frage des Signaljitters, der sich typischerweise auf weniger als 1 Zustand beläuft.
Inkremental-Encoder und absolute Positionen
Inkremental-Encoder geben nur Positionsveränderungen an. Für die absolute Positionierung muss zuerst eine Referenz- oder Homingposition festgelegt werden. Dafür wird der Mechanismus auf eine externe Referenz verlagert. Dies kann ein mechanischer Endanschlag oder ein Endschalter sein.
Manche Encoder besitzen einen dritten Kanal mit einem Impuls pro Umdrehung. Die Flanken dieses Indexkanals liefern absolute Positionsreferenzen innerhalb einer Umdrehung. Die begrenzte Genauigkeit externer Referenzen kann durch eine zusätzliche Bewegung zu einer Flanke des Indexkanals verbessert werden. Beachten Sie dabei jedoch bitte, dass der Indexkanal keine Voraussetzung für die Positionierung ist. Maschinenbauer vermeiden sogar die Nutzung des Indexkanals als Referenz, da eine erneute Kalibrierung erforderlich ist, sobald ein Motor-Encoder ersetzt werden muss. Zudem verwenden manche Steuerungen den Indexkanal, um die Encodersignale zu überprüfen und die Encoder-Impulszahl zu überwachen.
Signalübertragung
Line Drivers werden für die Übertragung über lange Leitungen und für eine bessere Signalqualität empfohlen. Für die Positionierung ist ein Line Driver ein Muss, um keine Encoderimpulse zu versäumen.
Line Driver generieren invertierte Signale (Ā, B̄, Ī) auf dem jeweiligen Kanal (A, B, I). Jedes Signalpaar wird gemeinsam übertragen und die Differenz wird daraufhin ausgewertet. Auf diese Weise werden elektromagnetische Störungen während der Signalübertragung herausgefiltert. Dadurch wird die Signalqualität verbessert, die Signalflanken werden klarer definiert und die Driver-Funktion ermöglicht die Signalübertragung über weitere Entfernungen (bis zu 30 m).
Encoder benötigen eine Minimal-Betriebsspannung. Bei längeren Encoderleitungen kann der Leitungswiderstand sowie der dazugehörige Spannungsabfall Probleme verursachen. Überprüfen Sie den Kabelquerschnitt sowie die Versorgungsspannung.
Umgebungsbedingungen, Robustheit
Die standardmässigen Betriebstemperaturen von Encodern liegen im Bereich von -30°C bis +100°C. Dies erfüllt auch die Anforderungen der meisten Applikationen und entspricht der vom Motor erzeugten Wärme.
Bei vibrierenden Anwendungen und mechanischen Stössen ist es wichtig, für ein robustes, mechanisches Gehäuse sowie für eine ausreichende Zugentlastung der Kabel zu sorgen.
Während optische Encoder weniger empfindlich auf elektromagnetische Störungen reagieren, benötigen magnetische Encoder eine geeignete Abschirmung gegen magnetische Streufelder. Wenn das Gehäuse nicht gut verschlossen und dicht ist, sind optische Encoder anfällig für Staub.
Im nächsten Blogeintrag werde ich genauer auf die Encoderwahl bei der Positionierung und der Drehzahlregelung eingehen.