maxon Inside
Cerámica en su máxima expresión
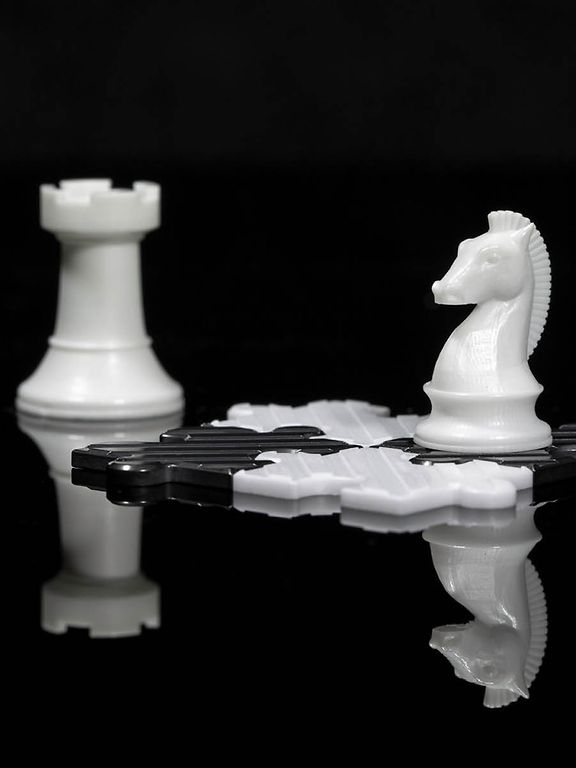
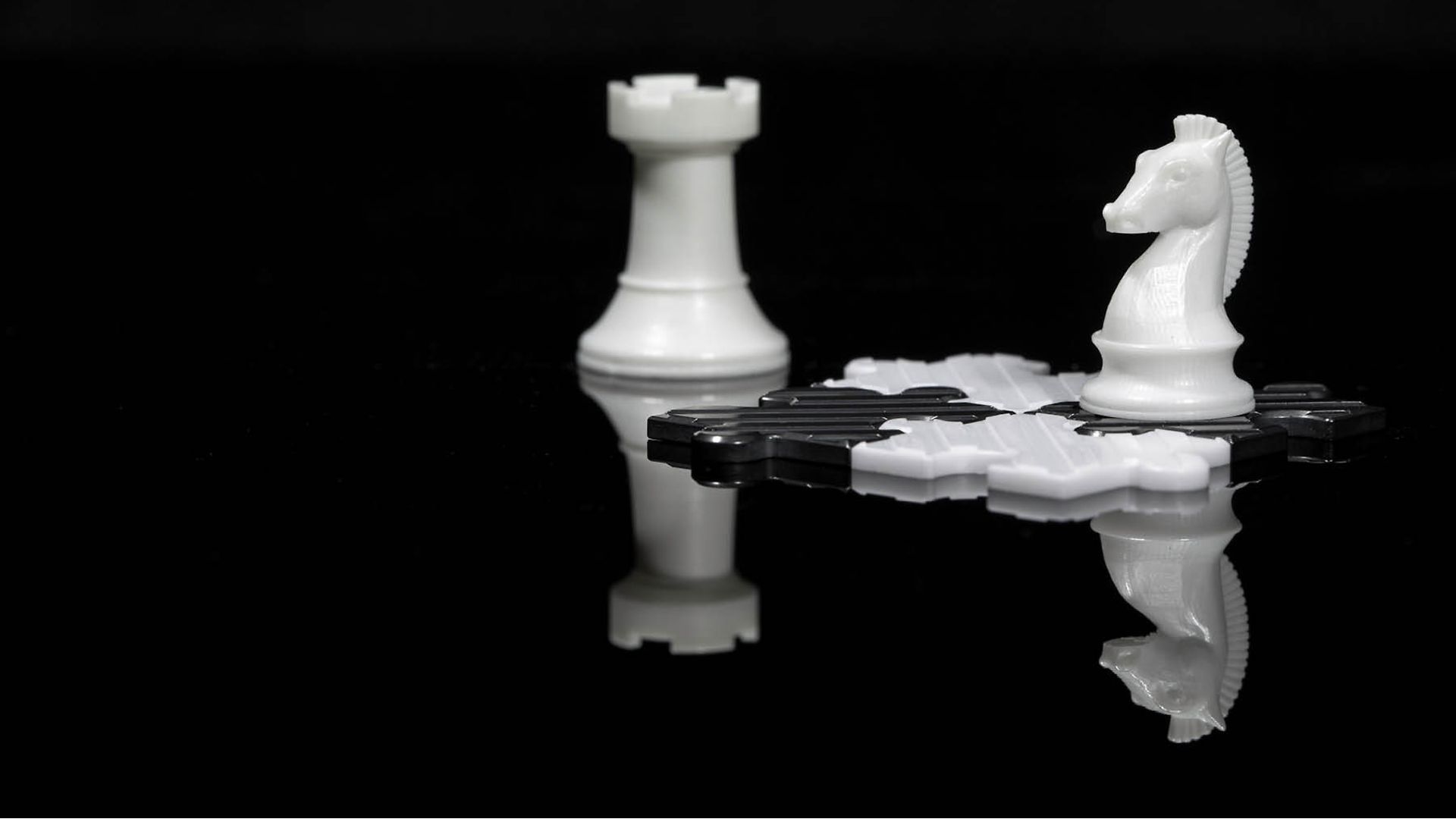
La fabricación aditiva de componentes de cerámica acelera la producción piezas para prototipos y ofrece nuevas posibilidades.
La empresa suiza maxon es conocida por su tecnología motriz, que ha viajado hasta marte en varios rovers de la NASA. Su departamento de alta tecnología para cerámica de uso técnico en Sexau, cerca de Friburgo (Alemania), no es tan conocido. Aquí, los componentes de cerámica también se imprimen ahora en 3D y se perfeccionan con láseres.
«¿Qué material tiene una mayor resistencia al desgaste que el acero y puede utilizarse para fabricar ejes y árboles de cara a conseguir que nuestros reductores planetarios sean más precisos y fiables?» Esta es la pregunta que se plantearon en maxon motor GmbH hace ya más de 20 años. Stefan Zilm, director de desarrollo empresarial e ingeniería de calidad en el Centro de Competencias CIM/MIM en Sexau, conoce la respuesta: componentes de cerámica producidos con moldeo por inyección de cerámica, un proceso similar al moldeo por inyección de metal.
Hoy en día, la empresa tiene unos amplios conocimientos técnicos en el campo de la cerámica de uso técnico. Con CIM, los componentes pueden producirse en serie en cantidades de varias decenas de miles. Sin embargo, a pesar de toda la experiencia, e incluso utilizando métodos de ingeniería de última tecnología —como CAD y cálculos y simulaciones con elementos finitos— la realidad sigue siendo la prueba definitiva que determina si una idea nueva tiene fundamento o si es posible producir una pieza de cerámica que se comporte según lo previsto.
El camino habitual desde la idea hasta el componente de cerámica real es largo y costoso. Se necesita un molde caro para crear el cuerpo verde que debe sinterizarse. A continuación, se tornea, se corta, se sinteriza y se lija en procesos que requieren mucho trabajo. Zilm admite: «En la primera muestra, esto es muy complicado. Cuesta mucho tiempo y dinero».
Cerámica salida de la impresora
Pero hay otra opción: usar el atajo que ofrece la impresión 3D, ya que se trata de un proceso ya consolidado para componentes de plástico y que se está usando cada vez más para metales. Mientras que la impresión de plástico ya forma parte de la producción industrial desde hace varios años, la impresión de cerámica aún está en el proceso de aventurarse a salir del laboratorio para entrar en las naves industriales. Sin embargo, las ventajas eran tan tentadoras que maxon ya inició pruebas piloto hace cinco años con el objetivo de obtener más rápidamente prototipos de componentes de cerámica para el cliente, para lo que realizó un verdadero trabajo pionero. Zilm comenta: «Con una impresora de este tipo, los dos o tres primeros ciclos de desarrollo pueden completarse con mucha mayor facilidad y rapidez».
Después de un intensivo estudio de mercado, maxon se decidió por una impresora del fabricante francés 3Dceram, la cual se personalizó para cumplir los propios requisitos de la empresa. «Para nosotros, los factores principales para la adquisición fueron la precisión y el gran tamaño del área de impresión de 300 por 300 milímetros», explica Zilm. La impresora utiliza el método de la estereolitografía, en el que un láser solidifica una emulsión compuesta por aglutinante y polvo de cerámica, construyendo así un componente capa por capa desde abajo hacia arriba. Las capas tienen un espesor de entre 0,025 y 0,125 milímetros. Después de aplicar cada capa, el lecho de la impresora baja un paso. Esto garantiza una reducción uniforme del volumen durante la solidificación, así como una alta precisión y reproducción de detalles muy delicados. No se requiere una estructura portante. La ventaja especial de los sistema 3DCeram es que también es posible crear piezas muy pequeñas con un volumen de tan solo 50 milímetros cúbicos.
En función de los requisitos, los componentes de cerámica se fabrican normalmente con óxidos de circonio y de aluminio. Estos materiales son el «sustento básico» del sector de la cerámica de uso técnico. Ambos están disponibles como emulsión para la impresora 3D. La tecnología de desaglomeración y sinterización se corresponde con el procedimiento CIM, lo que permite que los cuerpos verdes creados en la impresora 3D pasen por los mismos sistemas de fabricación que las piezas de serie. Dependiendo de la complejidad del componente deseado y del nivel de tolerancia requerido, también es posible realizar pequeñas series, lo que supone una buena alternativa al moldeo por inyección de cerámica (CIM).
Según Zilm, el procedimiento tiene sus limitaciones, debido a que el diámetro del rayo láser de radiación ultravioleta determina el grosor de pared mínimo que puede producirse. Los componentes se limpian con aire comprimido y un aditivo para retirar de ellos el material excedente. Los agujeros con tamaños menores o iguales a 0,5 milímetros no pueden realizarse con una redondez tan perfecta como la del moldeo por inyección, pero para prototipos suele ser suficiente.
Socios de desarrollo desde el primer momento
Hoy en día, basta con que el cliente envíe un archivo en formato estandarizado STEP (Standard for the Exchange of Product model data), que se ha popularizado en la impresión 3D, para que reciba una oferta poco después. Tan solo 10 a 14 días después de la confirmación del pedido, el cliente puede tener en sus manos las primeras piezas prototipo. «Antes, este proceso requería semanas o incluso meses, e implicaba altos costes de los moldes», recuerda Zilm.
Lo ideal es que el cliente implique a maxon desde el principio. «Somos socios de desarrollo desde la primera idea, por lo que podemos influir en el diseño para adecuarlo lo más posible a la cerámica», explica Zilm. Esto permite, por ejemplo, combinar varios componentes para formar un componente único con funcionalidad optimizada. Según Zilm, estas optimizaciones son muy importantes, considerando que el precio de un kilogramo de las materias primas requeridas para la cerámica cuesta unas diez veces más que para el acero. «Tenemos que justificar esto ofreciendo una funcionalidad significativamente mayor, por ejemplo, mediante resistencia al desgaste, estabilidad térmica o la ausencia de lubricantes».
Pero los límites de la fabricación aditiva aún no se han alcanzado. Andreas Philipp, director del Centro de Competencias CIM/MIM asegura: «Tenemos que empezar a pensar en 3D y no en la manera clásica como hasta ahora». Así descubriremos nuevas posibilidades, por lo que la impresión 3D podría ser una alternativa real a los procesos establecidos.