maxon Inside
Aquí no entran las bacterias
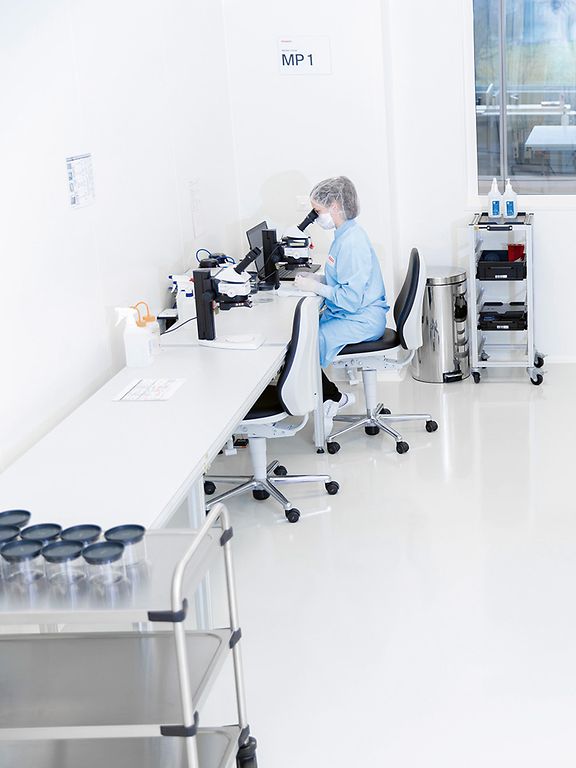
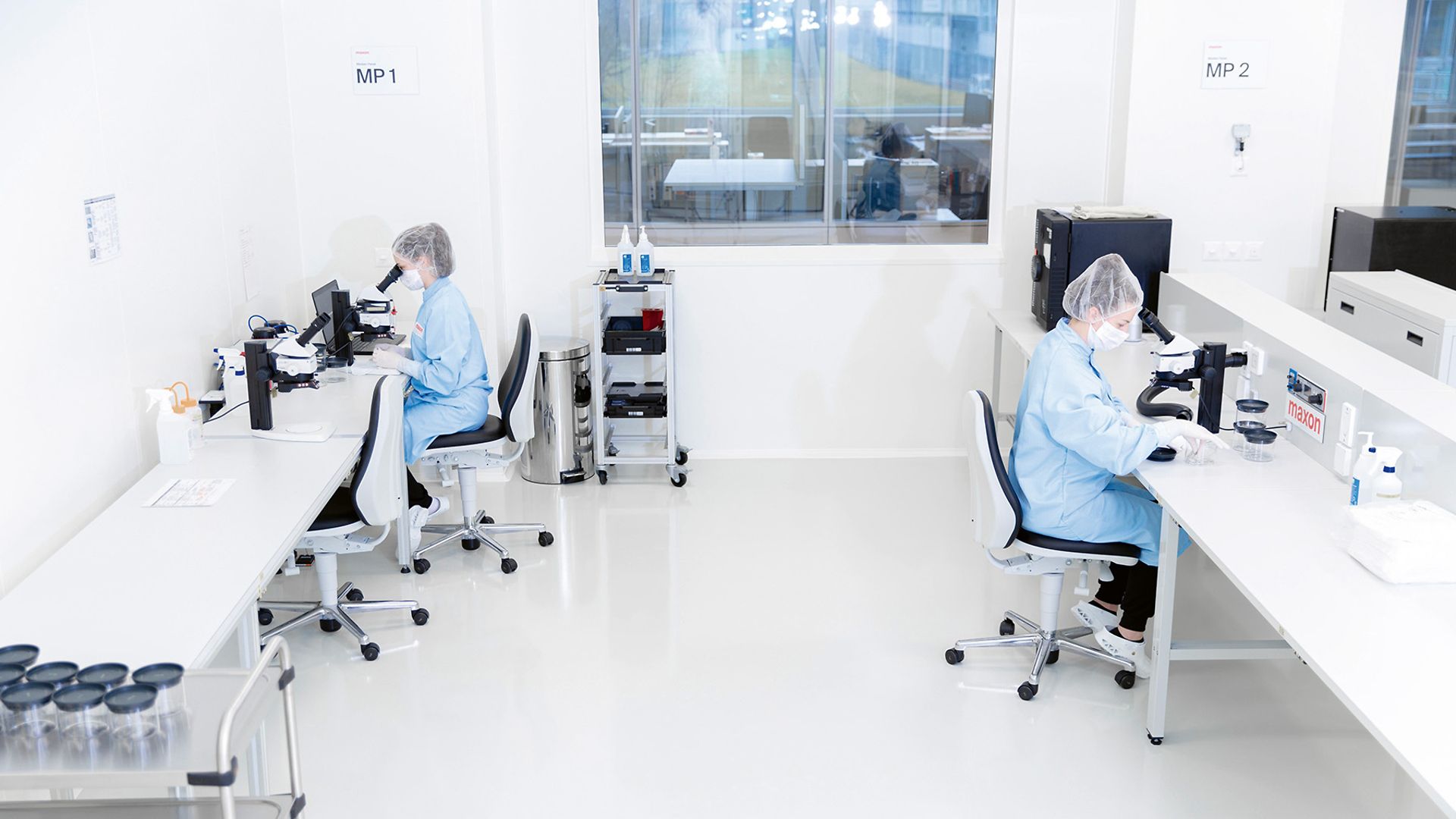
Los motores diminutos para su uso dentro del cuerpo humano deben fabricarse en un entorno limpio, libre de contaminación microbiológica. Bienvenidos a la sala blanca GMP de maxon en la que la disciplina se une a la gelatina.
Detrás del panel de vidrio, en la sala blanca y bien iluminada, el mundo es muy diferente al del resto de las áreas de producción del grupo maxon. Aquí, en la sede central de este especialista en motores, entre lagos y montañas, hace poco que comenzó a funcionar un área de producción para motores que se usarán en aplicaciones médicas. La concentración de partículas en el aire es baja y se monitoriza constantemente. Normalmente, este entorno limpio es perfectamente adecuado, ya que los motores para bombas de insulina, unidades de dosificación de medicamentos, etc. no necesitan estar completamente libres de bacterias y otros gérmenes.
Sin embargo, las aplicaciones en el campo de la medicina de alta tecnología son otra historia completamente diferente, sobre todo cuando se trata de sistemas motores implantables. Para estas aplicaciones, el ensamblaje se está trasladando a la nueva área GMP (buenas prácticas de fabricación, en sus siglas en inglés). En este tipo de sala blanca no solo se monitoriza la concentración de partículas, sino que también se mide la contaminación microbiológica de las superficies y el aire para detectar rastros de esporas, bacterias u hongos. Este entorno clínico plantea altas exigencias en relación con la tecnología de la ventilación, los instrumentos y, de forma especial, las personas que pasan tiempo en él.
La limpieza empieza y acaba con disciplina
Las personas que trabajan en este entorno siempre deben ejecutar los mismos procesos y cumplir idénticas y estrictas reglas. Los dos miembros del equipo de producción, Albane Lloqanaj y Ruth Da Silva, se ponen los pantalones y las blusas especiales envasadas al vacío que llegaron de una lavandería para salas blancas. Los materiales de alta tecnología de los que está fabricada esta ropa hacen que sea antibacteriana. A continuación, los dos miembros del equipo se colocan sus mascarillas higiénicas especiales, así como las redecillas para el pelo, las batas de laboratorio y el calzado antiestático.
Además, tienen que desinfectarse las manos durante un mínimo de 30 segundos con un desinfectante que no irrita la piel en un procedimiento de desinfección higiénica de las manos que consta de seis pasos. A continuación, se desinfectan los guantes con alcohol puro, que se evapora sin dejar residuo alguno. Esto garantiza que ninguna partícula o germen pueda adherirse a los guantes. Todos estos pasos de proceso tienen lugar en un orden definido. Además, es necesario asegurarse de que no entra aire contaminado a la sala GMP desde el exterior. Para ello deben cruzarse tres zonas separadas por esclusas de aire automatizadas. Solo es posible abrir una puerta a la vez, ya que, cuanto más se adentra uno en el sistema, mayor es la presión del aire en la sala.
En la sala blanca
Dentro de la sala blanca propiamente dicha, el equipo debe ser muy disciplinado. Por ejemplo, no les está permitido tocarse la cara. Y, si lo hacen, siempre debe ser de forma consciente para poder volver a desinfectar los guantes inmediatamente. «Me gusta mucho este tipo de trabajo, porque es exigente y variado, y requiere responsabilidad. No se admiten errores cuando nuestros motores se utilizan para sistemas implantables», dice Albane Lloqanaj, miembro del equipo de producción. Esto también requiere una actitud abierta para con los errores. Stefan Kathriner, el jefe del equipo, comenta: «Es importante que nos alertemos mutuamente si algo parece extraño o si ha ocurrido un error. La crítica nunca es personal, siempre es objetiva».
Para garantizar que la cantidad de bacterias y otros gérmenes en las superficies de trabajo o en el aire no exceda un límite determinado, maxon realiza pruebas periódicas con una gelatina rica en nutrientes. Estos preparados se denominan placas de agar y se presionan contra las superficies o se dejan en algún lugar de la sala. La gelatina sirve como caldo de cultivo para microorganismos. Después de 72 horas en la incubadora, es posible ver a simple vista si hay contaminación y en qué medida.
El esfuerzo que supone trabajar en un entorno GMP de este tipo es inmenso, por lo que aquí solo se procesan unos pocos pedidos especiales de clientes para sistemas implantables. En los últimos años, los especialistas en salas blancas de maxon han aprendido mucho de estos proyectos. Stefan Kathriner dice: «Disponemos de unos amplios conocimientos técnicos y esperamos poder procesar más pedidos de clientes de este tipo en el futuro».
Más información acerca de los sistemas motores para la tecnología médica: medical.maxongroup.com