maxon Story
Dans l’atelier du vide
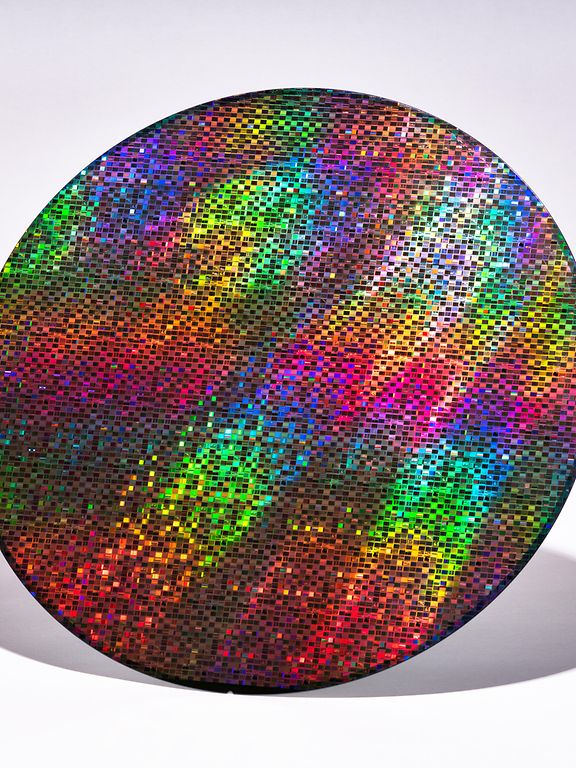
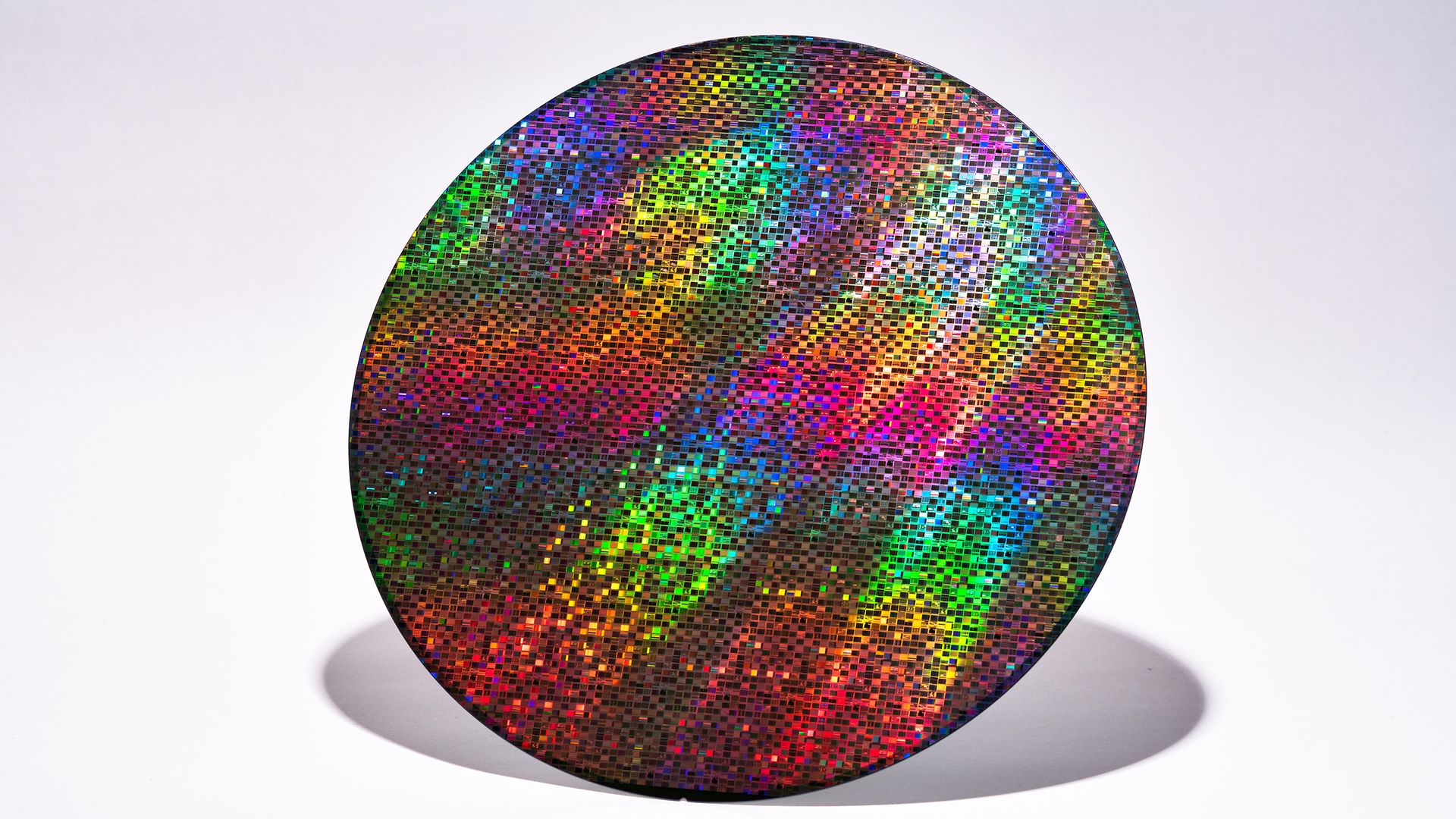
La propreté et la précision sont essentielles dans l’industrie des semi-conducteurs. VAT, spécialiste suisse du vide, a donc mis au point un système d’entraînement destiné à l’usinage des wafers, en coopération avec maxon.
Même chez ceux et celles qui s’intéressent à la technique, il y a peu de chance que le terme «vanne à vide» suscite l’enthousiasme. Qu’est-ce qu’une telle vanne peut donc avoir de captivant? Le sujet gagne en intérêt lorsque l’on est en visite chez VAT, entreprise internationale basée à Haag, en Suisse orientale. Dans toutes les applications industrielles requérant du vide, VAT est l’une des meilleures références au monde. Pour faire simple, disons qu’une vanne à vide est une vanne qui ouvre ou bloque l’accès à une installation de vide. Si le mot «vide» vous évoque en premier lieu les aliments emballés sous vide dans les supermarchés, vous faites fausse route. Dans le secteur industriel, les chambres à vide servent surtout dans les applications où le moindre grain de poussière ou goutte d’eau risque de saboter toute une étape de production. Cela nous place au cœur de notre sujet: l’industrie high-tech. Smartphones, écrans plats, panneaux solaires, processeurs... la fabrication de tous ces produits et de bien d’autres encore serait impensable sans installations de vide. La société VAT exporte donc une grande partie de ses systèmes vers l’Asie, où se trouvent les «grands acteurs» de la microélectronique et de la technologie des semi-conducteurs.
Un ascenseur pour wafers
Une étape importante du processus dans le domaine de la microélectronique est la fabrication et le traitement subséquent des «wafers». Il s’agit de fines plaquettes rondes en matériau semi-conducteur, tel que le silicium. Ces disques sont la base des circuits intégrés. Quand on sait que plusieurs milliards de transistors sont utilisés dans les processeurs modernes, notamment dans les smartphones, on se rend compte que tout corps étranger doit être éloigné lors de la production des substrats semi-conducteurs. Et le meilleur moyen d’y parvenir est de procéder à ces étapes de production dans des chambres à vide. Le hic: plus le vide est poussé, plus la pression de l’air extérieur est forte. Ce sont donc des forces considérables qui s’exercent sur une chambre à vide professionnelle. Une vanne courante ne saurait résister à une telle pression. Les vannes de VAT, elles, y parviennent.
Ces dernières années, l’entreprise a franchi une étape supplémentaire en proposant, en plus des vannes, des systèmes complets pour différentes étapes de production dans les chambres à vide. L’un de ces systèmes est appelé «pinlifter», une sorte d’ascenseur pour les wafers en silicium. Le wafer est déposé sur trois broches, et chacune de ces broches peut être déplacée verticalement par un moteur. Il en résulte une sorte d’ascenseur à trois pieds (trois pinlifters) qui permet de faire monter un wafer posé dessus dans une chambre à vide, où un système de manutention récupère le wafer. C’est là que les moteurs maxon déploient leurs atouts. Le pinlifter, système d’entraînement mécatronique de haute précision, est le résultat d’une collaboration de plusieurs mois entre VAT et maxon. L’unité d’entraînement d’un pinlifter se compose d’un moteur EC flat sans balais avec codeur optique, d’un frein et d’une broche. La longueur maximale de l’unité d’entraînement de 40 millimètres a constitué un défi particulier.
Marco Apolloni, responsable de l’ingénierie chez VAT, revient sur la phase de développement: «Nous avons dans un premier temps étudié environ six concepts, en choisissant différents fournisseurs dans le domaine du moteur, du frein, du codeur, etc.». Dans quatre de ces concepts, il a été adopté une approche par composants, dans deux autres, une approche par système, où l’ensemble de l’entraînement était considéré comme unité testée (y compris le boîtier, la broche, l’arbre du moteur, les composants d’isolation). «En raison des exigences élevées en matière de précision et de taille, seule l’approche système a été retenue pour la phase finale, car elle permettrait de minimiser de nombreux risques et de concevoir une solution optimale», explique Marco Apolloni.
«maxon nous a convaincu par son expertise technique et a pu proposer une solution complète».