Drive systems for the oil and gas industry
Designed for extremely harsh operating conditions.
maxon Heavy Duty drives for the oil and gas industry withstand temperatures up to 200 °C as well as pressure, shocks, and vibrations. This makes them ideal for extremely harsh operating conditions in a wide variety of drilling applications such as hydraulic valve controllers, communication mechanisms, and measuring instruments.
Heavy Duty technology.
maxon high-performance drives have been used in a variety of drilling applications, especially for MWD applications, since 2010. The ironless winding and the high-performance rotor combine with a powerful gearhead to produce a robust drive system with high torque. The maxon Heavy Duty range of motors features efficiency levels of up to 88% in air and over 70% in oil.
Designed for the highest temperatures.
Most components of our Heavy Duty drives are made of stainless steel. During assembly, we minimize the use of structural adhesives and instead join the individual components by means of mechanical fits and laser welding in order to increase their resistance.
The magnets in the Heavy Duty motors are made of samarium cobalt, which can withstand much higher temperatures before becoming demagnetized. The insulation used for the copper wire in the winding and the impregnating varnish also have higher temperature resistance.
Our product recommendations.
Motors
Many movements involve large forces, but at the same time a high level of dynamics is required, since the motors must constantly change the direction of rotation due to the movement. In addition, a compact design that takes up as little space as possible must be considered.
Gearheads
Our gearheads combine maximum power with low weight and low noise levels. This does not affect the performance of the prosthesis and increases user comfort.
Sensors
maxon offers inductive, magnetic, and optical encoders, DC tachos and resolvers in various versions and configurations.
Brakes
Cogging torque brake
- Mechanical brake
- Prevents reverse travel
- Compact
Drive systems for the oil and gas industry
Download brochure now.
Learn about maxon drives for the oil and gas industry and find out more about our products for downhole generators, hydraulic micropumps, electric setting tools, or measurement systems.
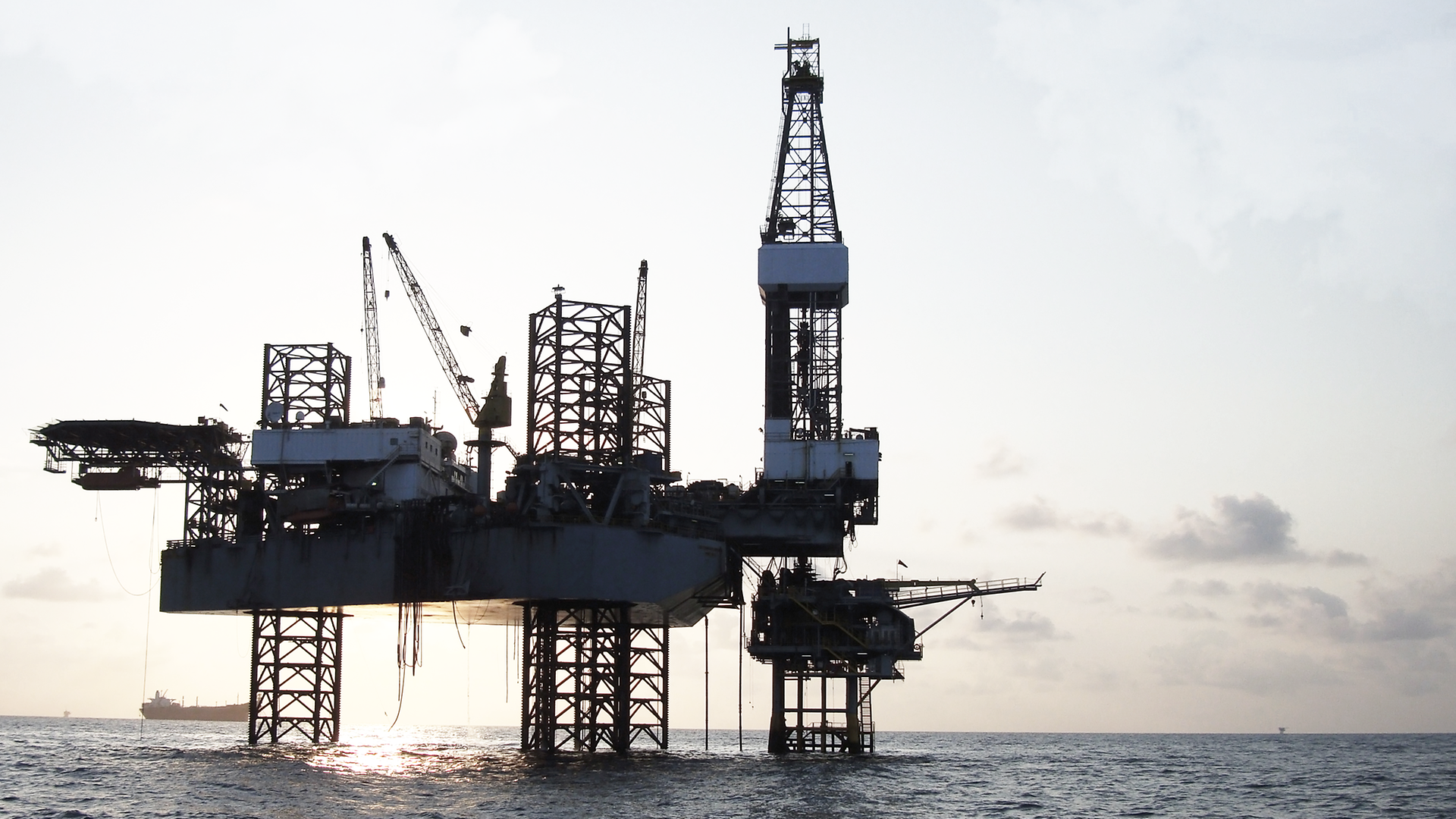
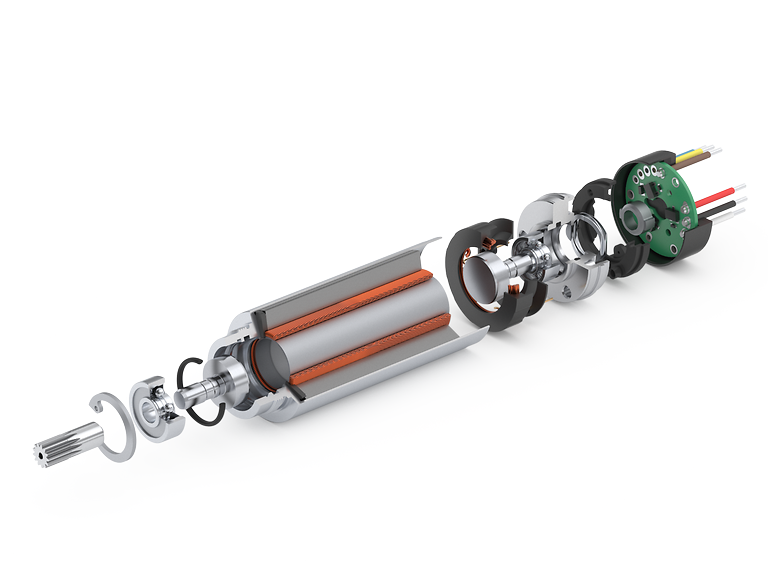
Custom-made products
Tailor-made.
Whether a complete electric drive system or a tailor-made drive that fits in a specific installation space, we develop high-performance drives from our products according to the specific requirements of our customers.
We push our drives to their limits.
Our in-house laboratory enables us to simulate extreme conditions and conduct standard maxon tests during the development phase. On request, we can also conduct customer-specific tests.
Frequently asked questions
How does maxon test drive components to ensure they are suitable for downhole applications?
All drive components from the Heavy Duty product portfolio are tested during the development phase for suitability for the downhole environment. Among others, these tests include exposure to high temperature, shock, and vibration. If necessary, we can also conduct customer-specific tests internally or externally. All high-performance motors and combinations are tested at high temperature in production.
Does maxon offer linear drives for downhole applications?
Yes. For linear drives, we can integrate ball screw or other spindle types into our gearheads.
What sensors does maxon offer?
Heavy Duty motors are equipped as standard with Hall sensors, which are also tested for downhole conditions. For higher precision, we offer the option of combining the motor with a resolver. This combination does not require Hall sensors.
Does maxon offer any Heavy Duty motors other than EC 22 HD and EC 32 HD?
EC 22 HD and EC-4pole 32 HD are catalog products for the Heavy Duty segment. These motors are available to order at all times, and are already qualified for heavy-duty applications. However, we also work on solutions outside the standard portfolio which are not listed in the catalog. For a custom drive solution, please contact our experts.
Contact
What challenges are you facing?
Our oil and gas industry experts will be happy to help you.