maxon Story
“A prosthetic will never be perfect”
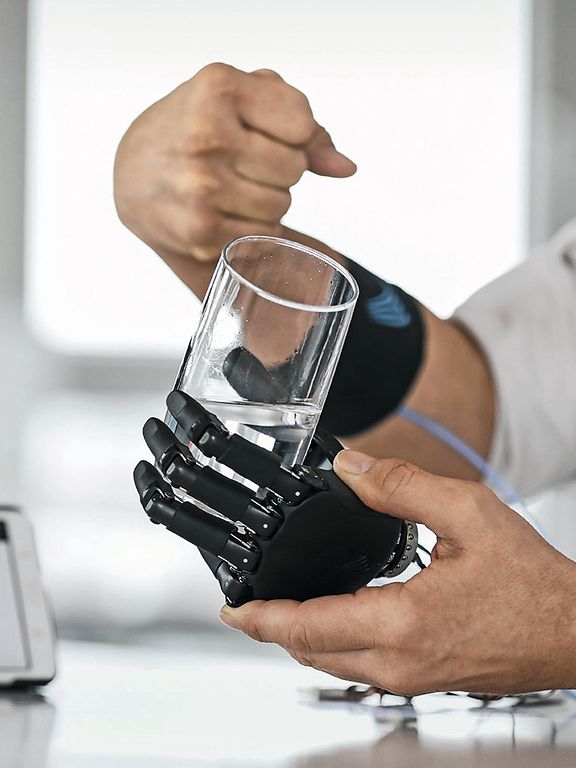
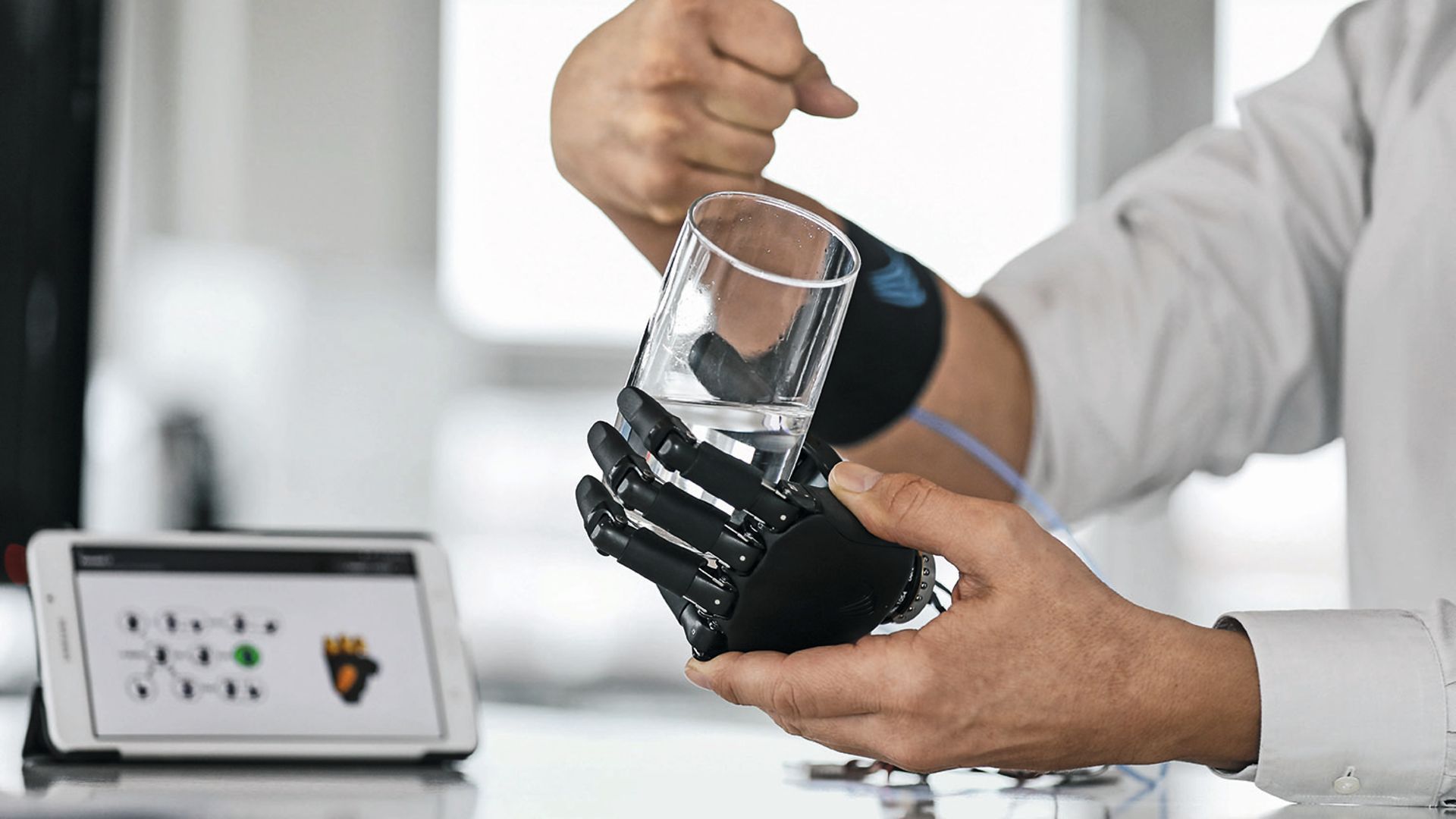
A small start-up is set to turn the market for hand prostheses on its head – with an innovative spirit, compact DC motors, and a touch function.
Opening the door is only the first of many challenges. A human hand encloses the handle, depresses it, and moves flexibly. In comparison, an electromechanical hand prosthesis is stiff. When the door moves, this results in large forces acting upon individual fingers. “This is why a good prosthesis needs to be made of high-quality materials and components,” Stefan Schulz says, with conviction. He is the founder and CEO of Vincent Systems, a start-up with ten employees in the German city of Karlsruhe. When it comes to hand prostheses, Stefan Schulz is an expert. He built his first electromechanical prosthesis in 1999 while he was still working at the Karlsruhe Institute of Technology (KIT). Ten years later, he moved into the private sector.
Currently, the third generation of prosthetic hands by Vincent Systems is available. “It's lighter and more compact than other models and basically weighs the same as a human hand,” Schulz explains. The smallest version is even suitable for children – its youngest wearer is only eight years old. The special thing about these hands is that they're bionic. This means that each individual finger is actively driven by a DC motor, and the thumb is driven by two. The motors are installed directly in the fingers and thumb, which makes it possible to replace digits individually. There is something else making the Vincent Systems hand so special: It's the first commercially available prosthetic hand that delivers feedback about grip strength to its wearer. This is achieved with short pulses of vibration. If the hand were to vibrate evenly, a person would quickly get used to the sensation and stop paying attention to it.
Stefan Schulz knows that the task he and his colleagues have set themselves will never be complete. As an engineer, he wants to develop a mechatronic hand prosthesis that imitates the human hand as closely as possible. “But it no matter how many innovations we come up with, compared to the human original it will always be a compromise. The product will never be perfect; it can always be improved.” However, this doesn't discourage him. On the contrary, it motivates him in his daily work, and it may be one of the secrets behind the success of Vincent Systems. During the short span of the company's existence, the engineers completely revised the prosthetic hand several times, taking into the account feedback by users of the prosthesis and trying new technological approaches. Hearing Stefan Schulz speak, it seems that this wasn't a big deal. As an engineer, he obviously feels comfortable in his field of expertise.
The basic design of most arm prostheses has not changed since the 1960s, when the first models equipped with motors and myoelectric controllers were launched on the market. Two electrodes attached to the wearer's remaining muscles enable them to open and close the gripper. In most cases, only the thumb and forefinger are powered. This design that hasn't changed much for a long time – in part due to the fact that many users were content with these simple functions. In the words of Stefan Schulz: “The world of prosthetics has been in a decades-long slumber, and today it's an engineer's paradise.” While he appreciates the robustness and practicality of simple prosthetics, he is also convinced that “the future belongs to bionic prostheses! We have the technological means, so we should use them to help customers enjoy a higher level of freedom.”
maxon drives deliver that little extra bit of power
Prosthetics present a significant engineering challenge because of their conflicting design goals: high torque, high speed, compact size, and as energy-efficient as possible. This makes the choice of integrated motors so important. Prosthetic hands by Vincent Systems incorporate up to six maxon brushed DC motors: DCX 10 drives – which are also being used in the first Mars helicopter – in combination with modified GP 10 A planetary gearheads. “The units are compact, and they are the motors with the highest energy density currently available for our application,” says Stefan Schulz. Moreover, the drives need to be durable and function flawlessly for about five years while being exposed to highly diverse, heavy strain every day. “We are very satisfied, and we plan to further modify the electric motors for our future prostheses in cooperation with maxon.”
Being able to move each finger individually opens up many possibilities for the wearer. 12 grip patterns are available that can be activated fairly easily via muscle contractions – for example by holding a muscle signal or with a double impulse. It was important to Stefan Schulz that patients wouldn't need their healthy hand to help. “A prosthetic hand should help its wearer and not demand the attention of the good hand.” Most customers need no more than half an hour to learn to control the hand well. Depending on the person, it then takes another few weeks up to a few months to be able to control the prosthesis fully intuitively. After that, the wearer will be able to ride a bicycle, tie shoelaces, hold raw eggs – and open doors, of course.
Image Copyrights
maxon Group/Karin Mertens