Expert Blog
Flexible communication within a mechatronic system
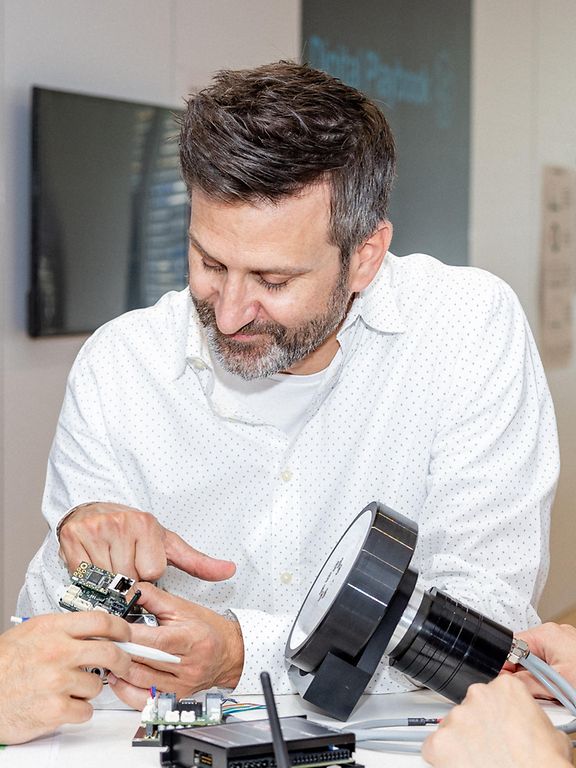
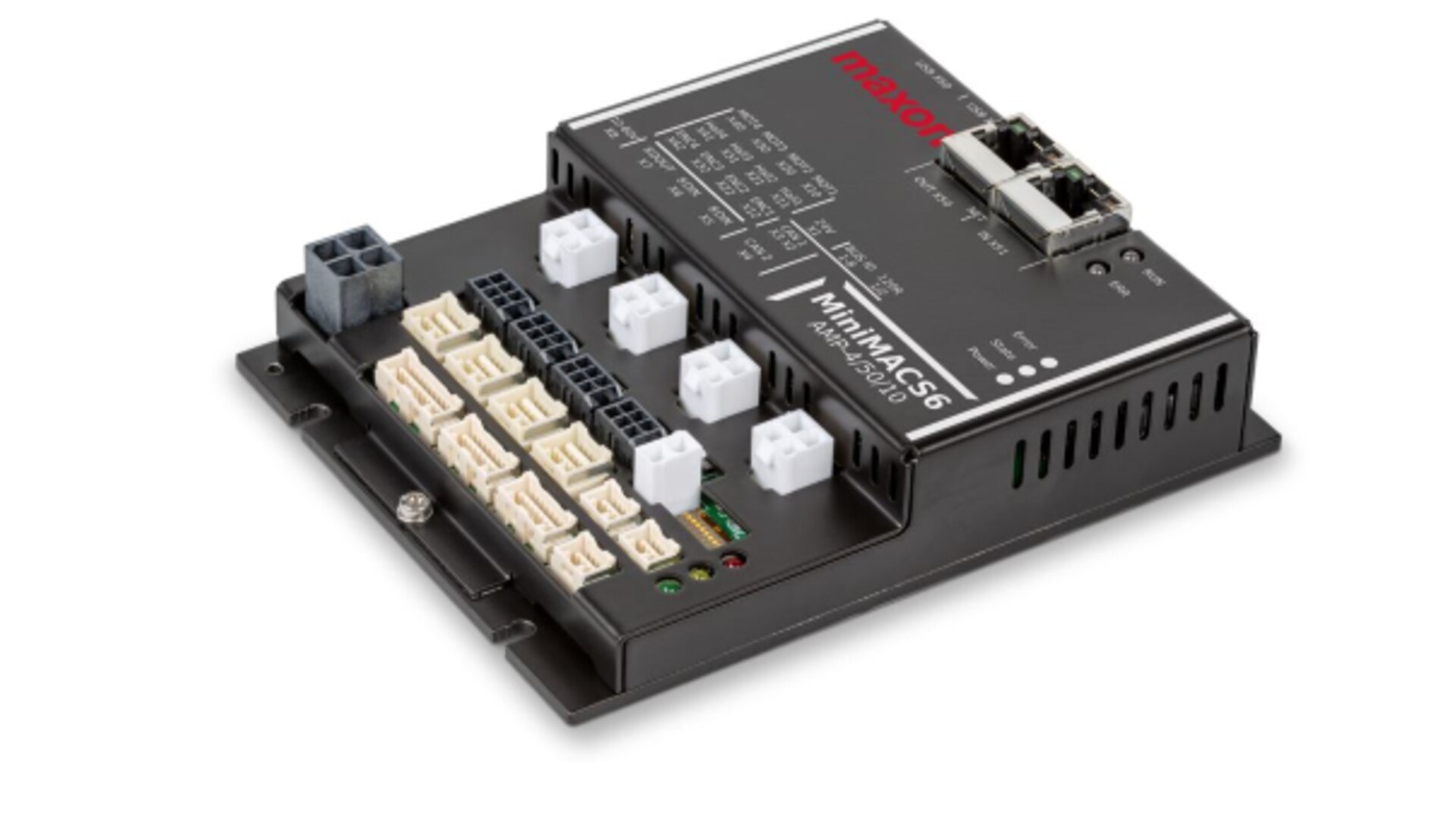
maxon develops and produces multi-axis control modules for precise positioning and synchronization of drives. These can be quickly integrated into existing systems. We discussed this and other advantages with Fabian Vogel, Managing Director at zub.
MACS motion controller autonomously regulates the highly dynamic positioning and synchronization of up to 32 axis. The controllers are preferably used where PLC solutions are either too expensive or simply do not meet the high requirements. With the control devices of the MACS6 generation, maxon has two devices on the market that are ultra-compact and set new standards:
The MiniMACS6-AMP-4 moves up to four BLDC motors, six DC motors or three stepper motors and has integrated amplifiers and encoder inputs.
The MicroMACS6, on the other hand, is a pure master controller without integrated amplifier and commands one to six external power stages via CANopen. The MicroMACS6 is one of the most compact control devices on the market. These motion controllers play a central role in bringing drive components together into a mechatronic system.
Why should an elementary component like a controller be replaced within a functioning mechatronic system?
There can be many reasons for this:
Let’s take a company who has used its own customized positioning controller for years. Shortages or even the discontinuation of electronic components make its production difficult and pose major challenges for management. How can they act quickly and find an agile solution for the existing system? Developing your own solution usually takes time and money and does not always make economic sense. At the same time, existing systems must continue to run “in time”.
Another scenario is the expansion of an existing system by one or more axes. How can this be implemented with little effort without interfering too much with the existing system and affect it?
How can maxon support here?
With the MiniMACS6 and the MicroMACS6, maxon offers a compact, freely programmable controller. This enables us to provide simple integration and quick implementation at the end customer.
A concrete example?
maxon can draw on a broad hardware and software base and adapt it to specific requirements. Within a few days, we can create a functional sample that fully meets the requested performance. After successful use, such as a demo model, maxon can offer a functioning solution.
Is such integration feasible in all system architectures? Where are possible limitations?
By carefully coordinating the architecture and configuration of the controller with the requirements of the application, we ensure safe integration into the existing system. In some cases, however, additional hardware or more powerful controllers may be required. Efficient design and targeted programming contribute to maximizing the flexibility and performance of the MACS controllers.
Thanks to their programmability, MACS controllers enable a comprehensive selection of architectures for various requirements. The controllers can be used as a CiA402 slave in conven-tional applications as well as a master in partial or complete systems.
The interface to higher or lower-level systems can be individually defined, which facilitates integration into existing systems. This gives engineers and technicians more options when developing mechatronic systems and thus enables flexible adaptation to changing requirements at any time.
How can my system communicate with a MACS controller?
The MACS6 generation offers various communication protocols that are suitable for integration into different systems. These include two independent CAN drivers and interfaces for USB, TCP/IP (Transmission Control Protocol/Internet Protocol) and EtherCAT (slave).
For integration into Windows systems, a communication DLL is provided, while a library is provided for Linux systems. Regardless of this, the MACS controllers can also be operated as a TCP client or TCP server via the Ethernet port. These enable communication between the MACS controller and the higher-level system and facilitate the integration of the controllers.
What knowledge is required for the use of a MiniMACS6 controller?
Knowledge of the C programming language is an advantage. To make it easier to get started, we offer a free SDK (Software Development Kit). This software development package contains useful functions as well as numerous specific program examples.
Using our own development environment, ApossIDE, control processes can be analyzed and recorded in real time. With the application library, we can fall back on prefabricated standard solutions for various machine types and applications. This allows us to interact quickly with the existing system.
What if there is no suitable interface to the MACS6 controller generation?
Which interfaces are needed? With the MiniMACS6, for example, we offer the standard interfaces CAN and CANopen as master and slave. Thanks to an integrated SoC (System on-a-Chip), we also support Ethernet and the EtherCAT interface (ProfiNet by arrangement). If needed, we can also provide a USB connection.
The MicroMACS6 has a BLE (Bluetooth Low Energy) service and support option for the first time. This makes it possible for the first time to have a wireless interface to all nodes of the CANopen bus for service and support via a specific smart device application.
Why does maxon develop a controller with such a wide range of interfaces?
As a specialist in multi-axis positioning and synchronization, we not only offer standard solutions, but often also customer-specific (OEM) solutions. This means that we must interact with our customers’ systems in a variety of ways and adapt to them.
Another reason is that interfaces are needed simultaneously in a specific architecture. For example, service interfaces are needed for debugging or ensuring oscilloscope recordings or monitoring motion sequences without interrupting the communication of a higher-level system.
This flexibility is one of our strengths that we focus on.
Back to integration into a mechatronic system. Where does maxon draw borders?
When developing applications, questions automatically arise that affect the entire architecture. Are there higher-level controls? Which interfaces are used for communication? Are real-time capability requirements relevant? Which and in what form do the axes work together? How does the dynamics affect and what precision is needed? Here we are already in the middle of system thinking. Here maxon draws clear borders: we are system experts in the drive area.