maxon Story
Brave new underwater world
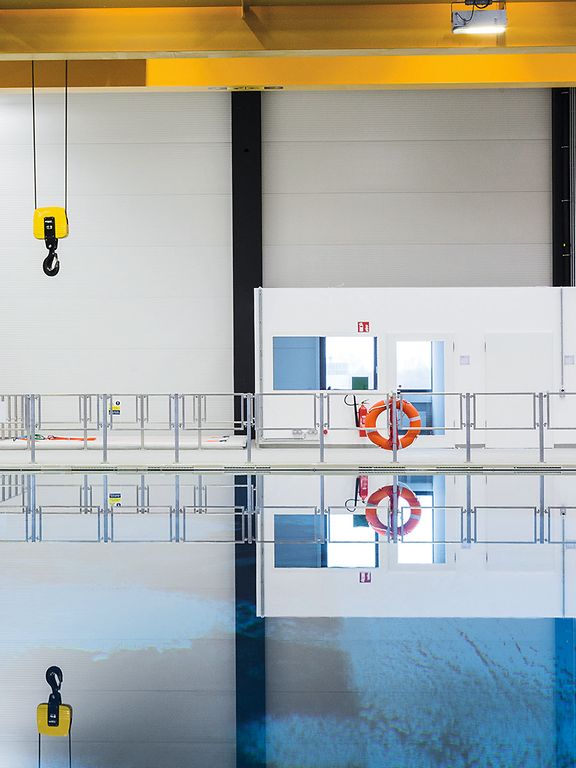
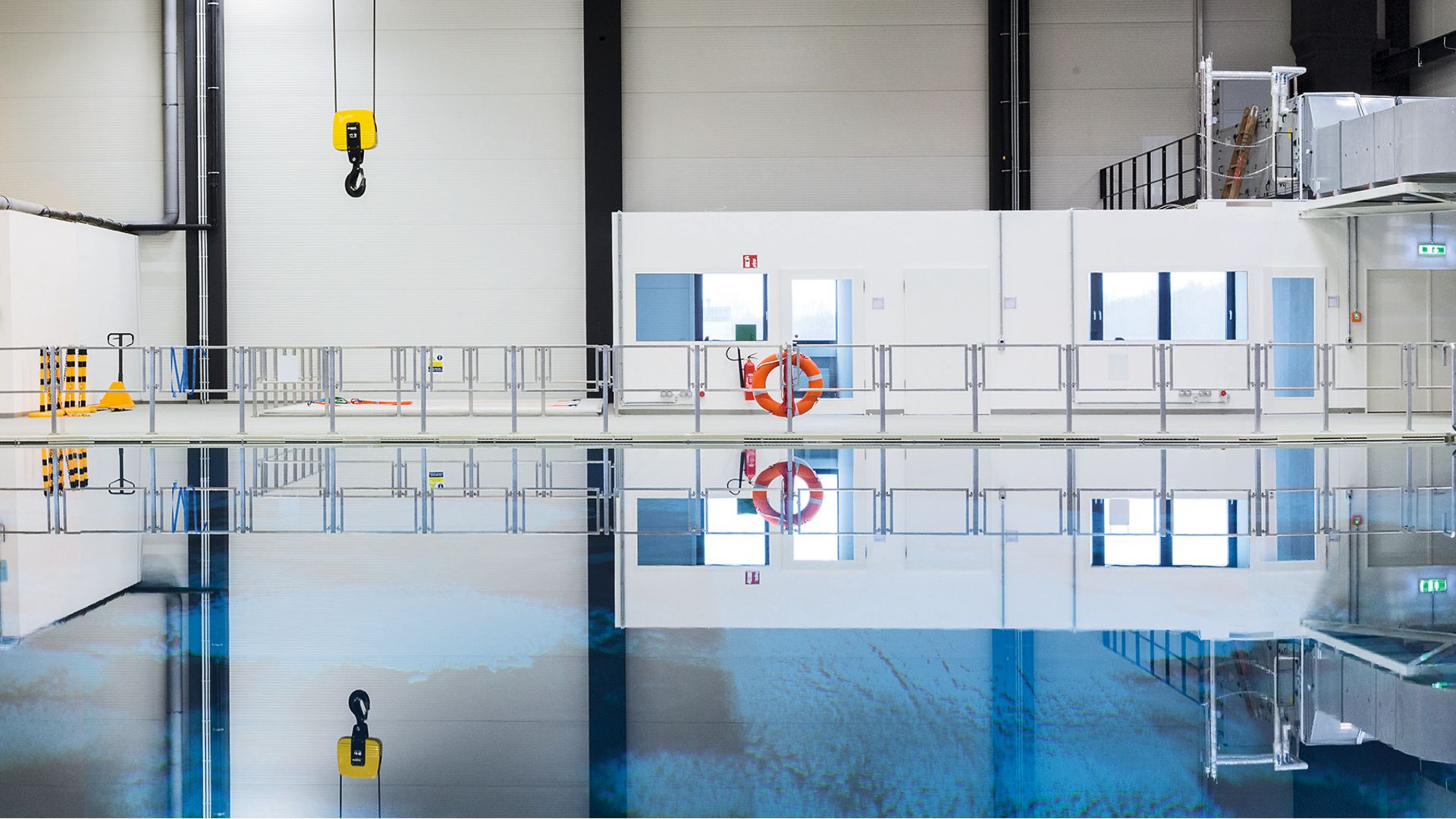
Engineers at the Robotics Innovation Center in Bremen have been working with underwater robots. They are intended to help us understand the world’s oceans. And in the future also the deep waters of other planets.
The passion of the engineers is apparent from the Christmas tree which stands at the bottom of a large water tank throughout December, prominently displayed for all the visitors to the German Research Center for Artificial Intelligence (DFKI) in Bremen. Buoyancy pulls the Christmas baubles upwards. Fairy lights provide suitable lighting – with 230 V. But don’t worry. The researchers know what they are doing. Underwater technology is their specialist area. They decorated the Christmas tree for the fun of it in their spare time. “With the excellent conditions here at the institute, the motivation for trying out innovative new approaches is particularly high. Sometimes we enjoy staying here longer,” says Peter Kampmann, research associate and specialist in underwater robotics at the DFKI Robotics Innovation Center.
Kampmann takes us through the large maritime exploration hall of the DFKI. This is home to a Europe-wide unique testing system for diving robots: a saltwater basin eight meters deep and with a capacity of 3.4 million liters. Perfectly suited for testing new underwater systems, which inspire ships and pipelines to explore unknown waters or perform measurements in the deep sea.
The maritime sector has led a shadowy existence for a long time. Large sections of the deep sea are still uncharted, for example. So we don’t know what it looks like exactly down there, at a depth of 3,000 to 6,000 meters. There are more accurate maps of even the surface of Mars. But in the next few years all this is set to change – also due to modern technologies. The Robotics Innovation Center of the DFKI is working closely together with the engineers at maxon on new underwater drives with brushless DC motors. They are pressure-tolerant, compact and energyefficient and ideally suited for ROVs (remotely operated vehicle) and AUVs (autonomous underwater vehicle). A development which comes in handy for Peter Kampmann and his colleagues. “New components which are lighter and more powerful open up completely new opportunities for us.”
The polar bear comparison
The trend in underwater technology is moving towards “small and intelligent.” Engineers are currently building vehicles which are equipped with sensors and electronics. The machines should be able to carry out research, collect data and react autonomously to different scenarios for months without any human intervention. Not an easy task in such tough conditions, for visibility is poor in the sea and wavelengths which are used for GPS or WLAN signals are quickly absorbed in water. This makes navigation difficult. The saltwater also attacks the components, and even corrodes stainless steel after a certain time. Sensitive parts such as motor shafts should therefore be made from titanium. And last but not least, there is the high ambient pressure. The pressure at 6,000 meters is 600 bar. This is roughly comparable to a fully grown polar bear sitting on an area of only one square centimeter. The Robotics Innovation Center can simulate such values in a pressure chamber. maxon also had its specially developed underwater drives tested here. Components at a depth of 6,000 meters can be used in over 95 percent of the world’s oceans.
Every gram is important
While walking through the Robotics Innovation Center of the DFKI we come across several underwater vehicles. Take, for example, the Micro-AUV. As the name says, it is particularly small and is used by researchers to test new approaches to control and navigation. Everything on this vehicle must be designed to achieve minimum residual buoyancy. Every additional gram of buoyancy plays a role under water. For if a system should fail at any time, it must rise to the surface through positive buoyancy control, otherwise it will be lost for ever. The Micro-AUV is driven by four maxon DC motors. They are particularly energy-efficient drives and enable a long service life in spite of the small battery.
Trip to Jupiter’s moon soon?
Another of DFKI’s exciting projects is the Europa Explorer, an underwater exploration vehicle, which is long and shaped like a thin cigar. The long-term objective of this project is the exploration of Jupiter's moon Europa. It is covered with a 3- to 15-kilometer-thick layer of ice, under which lies an ocean. The DFKI is researching into the potential of such a mission on behalf of the German Aerospace Center (DLR). This would involve – according to the current theory – the AUV reaching the underground ocean inside a drill, where it then detaches itself, autonomously collects data and then sends it to the Earth.
The current test type at the DFKI is equipped with a maxon Escon Module 50/5 motor controller. It is particularly popular on account of its dynamics and assist function. “The controller autonomously detects sources of error, which makes our work much more pleasant,” says Peter Kampmann. And after the visit to the DFKI Robotics Innovation Center it’s clear: The field of underwater applications is no longer characterized by large, robust components and improvisations. Sensor technology, automation and robotics are also playing a role in the meantime. A promising starting point for the future.
Robotics Center
The German Research Center for Artificial Intelligence (DFKI) is Germany’s leading institute in the field of innovative software technology based on artificial intelligence methods. It has a workforce of 800 spread across various locations. Around 130 employees and 80 students are working on 25 to 30 projects dealing with robots in space or in the deep sea at the Robotics Innovation Center in Bremen.
Special deep sea drives
maxon motor is venturing into the dark depths of the ocean. After a two year development period the Swiss drive specialist is presenting its own underwater drives. These thrusters consist of a brushless DC motor, a gearhead and a controller. Added to this is the housing and a propeller. The unit is designed for use in seawater, withstands pressure at a depth of 6,000 meters (600 bar) and is corrosion-resistant.
To ensure this, maxon used mainly titanium and plastic. The engineers cooperated with the German Research Center for Artificial Intelligence (DFKI) to carry out development work. The institute is specialized in underwater vehicles. The first model of the thruster, the MT30, is available this year as a standard product. Other sizes (20, 40 and 70millimeter diameters) are planned.
Oil-filled and pressuretolerant
maxon offers a pressuretolerant drive system as a standard solution for custom underwater applications. Th e core element is a motorgear combination, comprising a brushless DC motor and planetary gearhead. For corrosion protection the drive is encased in a plastic housing and sealed with two titanium flanges. It can be connected to a compensator.
The oilfilled drive unit is connected to the compensator via a tube. The water pressure is transferred to the oil by a membrane, which, depending on the depth of the water or water pressure, is compressed by a particular volume. The drive is equipped with connectors to connect the control electronics. The compact underwater drive is available with diameters of 16 to 42 millimeters. And this will be customized depending on the customer’s requirements.
maxongroup.com
Image Copyrights
maxon motor ag; DFKI