Young Engineers Program
Blazing the trail for flying robots.
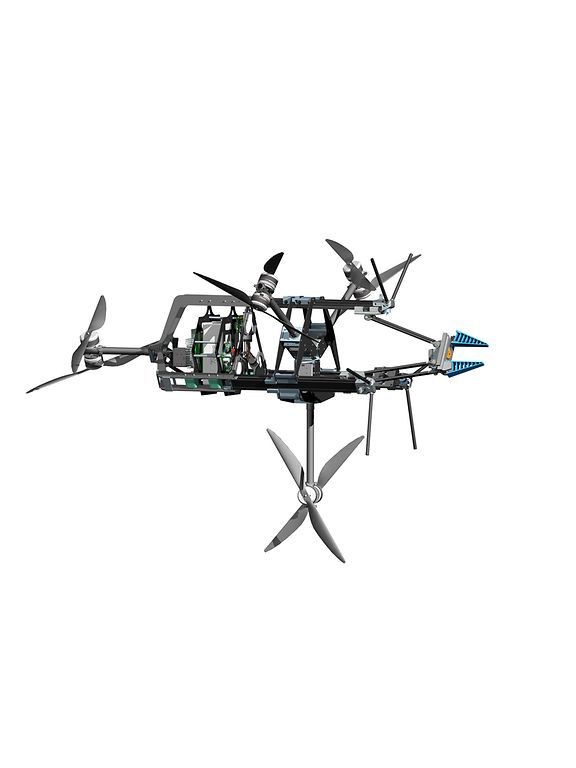
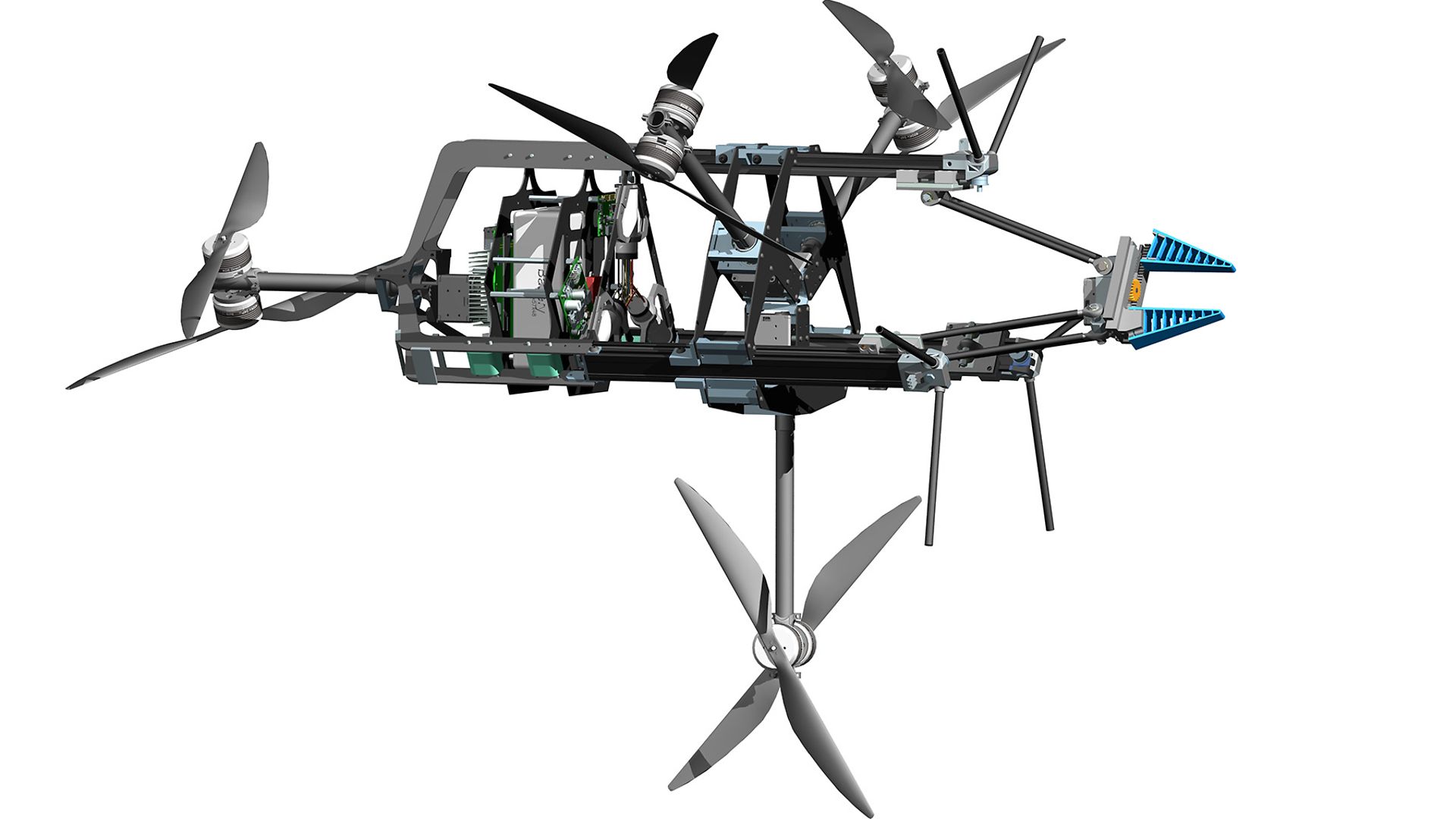
As part of a focus project at ETH Zurich, eight Bachelor students built a flying manipulator that can hover in any orientation and grasp objects. The drone is even more maneuverable than a quadrocopter and has been designed with the aim of pushing aerial robotics to new heights.
A warehouse with flying robots that transport packages. Many inventors have attempted to turn this vision of the future of intralogistics into reality by equipping quadrocopters with serial gripper arms. But such drone-plus-arm combinations are sluggish and the projecting arm causes an unfavorable weight distribution that affects both the precision and the load capacity. Additionally, quadrocopters can only rotate on the horizontal plane, which means that the so-called end effector – in this case, the gripper – cannot move in all directions. For the time being, most drones are currently still limited to inspection tasks.
Last fall, a team of Bachelor’s students in mechanical engineering and process engineering at ETH Zurich got an idea for developing an integrated flying robot that does not suffer from these shortcomings. The young engineers tackled the focus project, which was tendered by Autonomous Systems Lab (ASL), and built an omnidirectional flying manipulator – in other words, a device that is capable of physically interacting with its surroundings.
Inspired by a 3D printer
To create a high-precision end effector, the students installed a linear parallel arm that is positioned by means of three slides that move within a prismatic structure. The young innovators equipped the Prismav – Prism Micro Aerial Vehicle – with four differently aligned drives, each consisting of two propellers rotating in opposite directions. This balances out the moment of the individual propellers and provides stable flight behavior.
The inspiration for the delta arm came from the inside of a 3D printer. Matthias Rubio, mechanical engineering student, explains: “We were standing in front of the 3D printer and got the idea to use the interior structure of the printer to build a flying platform that combines flying and manipulation.” This is a new approach, as this kind of delta arm is still rare in flying manipulators.
Parallel arm compensates positioning errors
The rotor groups can rotate around their own axis. This enables the 7.5 kg flying object to hover in any orientation. During the focus project, the omnidirectional drone was operated inside a room that is equipped with a visual motion tracking system and ensures accurate measurement of the position and alignment. This makes Prismav capable of interacting with its surroundings and positioning the gripper with precision. Two batteries with a capacity of 20,000 mAh provide a flight time of around 12 minutes.
The remaining imprecision in the flight maneuvers is usually in the range of 10 to 15 centimeters. To compensate this, three brushless maxon motors accurately position the gripper arm. The three slides, which move on linear guides, are all individually positioned by means of a toothed belt. With this system, the gripper can reach any position within the marked 3D space. To save weight without compromising force, the team chose the compact ECX TORQUE 22 M drives.
For dangerous or inaccessible areas
With Prismav, the students established the foundation for further research. Matthias Rubio adds: “We demonstrated that a flying manipulator can grip, transport, and put down a 500 g cylinder by interacting with its surroundings.” The key is that the gripper arm compensates positioning errors faster than the drone moves.
The focus project, which was presented in 2021, met with great response. Therefore the students are now continuing to develop the Prismav as part of their Bachelor’s projects. They are optimizing the automated positioning, flight path calculation, and control software, and are integrating an intuitive controller. This makes sense, because the potential range of applications is huge. For example, flight robots could in future perform work in inaccessible or dangerous locations: tightening screws, setting up scaffolding, repairing high-voltage lines, or even building avalanche protection structures.
Image Copyrights
Focusproject Griffin