maxon Inside
最好的陶瓷
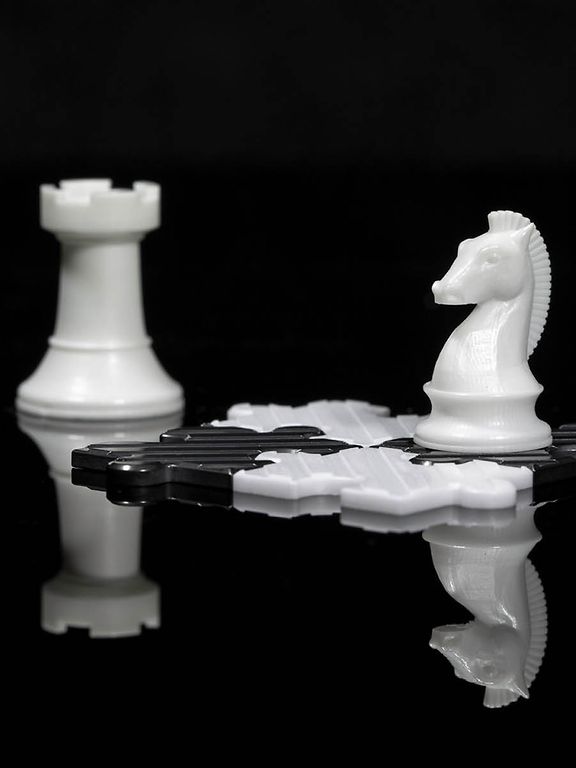
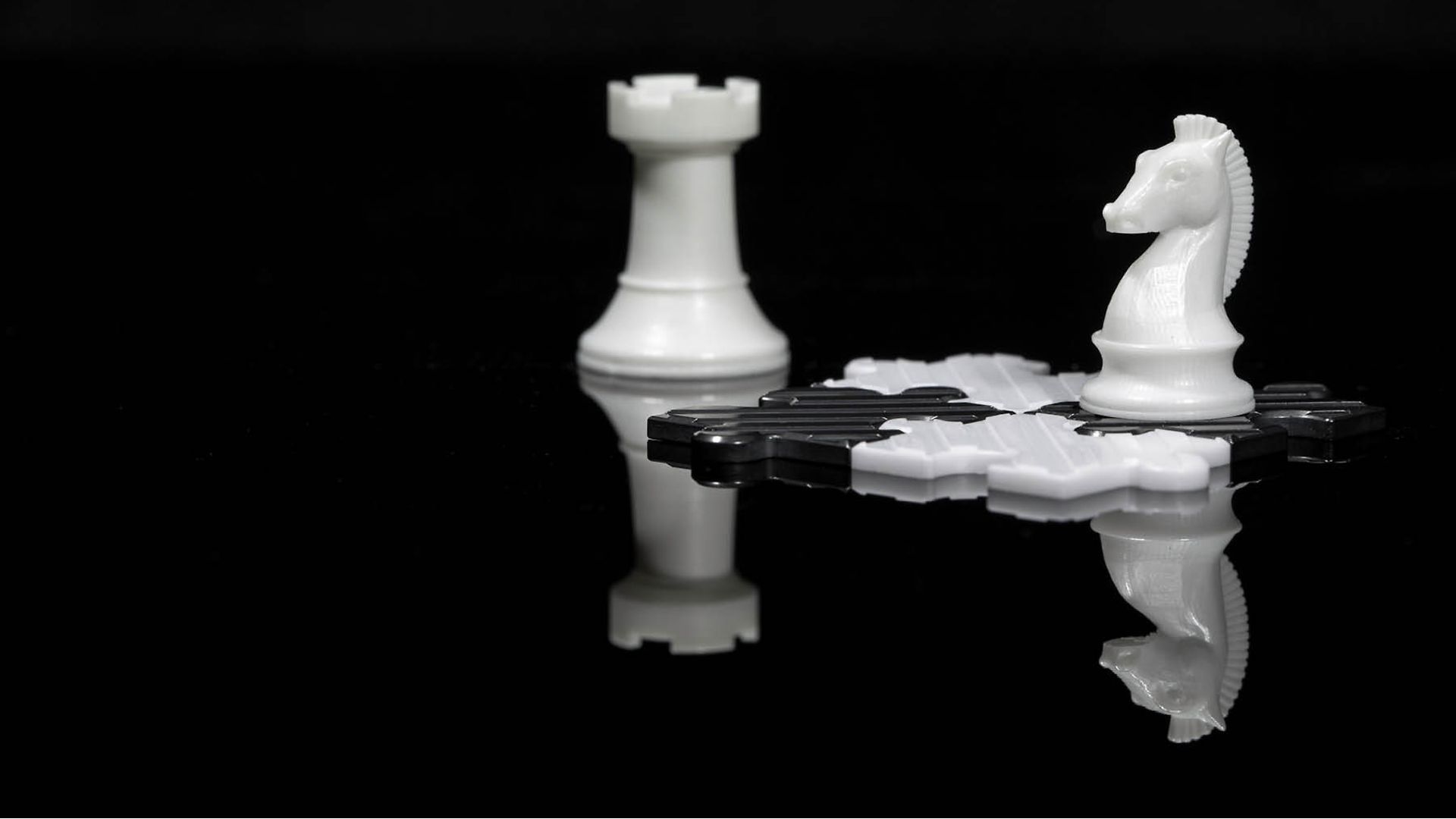
陶瓷組件積層製造技術加快了原型零件的生產速度,,並開啟了全新可能性。
瑞士公司 maxon 以其驅動技術著名,名聲透過各種美國太空總署探測車遠馳火星。然而,位於弗萊堡附近塞克紹(Sexau)的技術陶瓷高科技部門,卻少有人知。現在,這裡也開始採用 3D 列印技術製作陶瓷組件,並且再用雷射使其臻至完美。
「什麼材質比鋼材更耐用,而且可以用來製成我們行星式減速機裡的軸桿,讓它們更精準和可靠?」在 20 多年前,Maxon Motor GmbH 驅動技術公司的專家們便已如此自問。塞克紹 CIM/MIM 能力中心的開發與品質工程主管 Stefan Zilm 知道答案:以陶瓷射出成型技術(Ceramic Injection Molding,CIM)製成的陶瓷組件。這個過程與金屬射出成型(Metal Injection Molding,MIM)類似。
今天,這家公司在技術陶瓷領域擁有廣泛的專業知識。利用陶瓷射出成型技術,可以大量生產成千上萬的組件。然而,儘管有所有的經驗且使用了例如 CAD、有限元計算和模擬等最先進的工程方法,現實仍是最終考驗:新想法是否萬全,或是陶瓷元件到底能不能做得出來,並具有預期中的表現。
從想法到實際陶瓷組件之間的這條路,通常是漫長且昂貴的。首先,需要昂貴的模具來製作待燒結的生坯。接著,生坯需經過車削、切削、燒結和打磨等密集工作過程。Zilm 承認道:「第一個樣品非常複雜,需要花費很多時間和金錢。」
來自列印機的陶瓷
但還有另一個可能性:利用 3D 列印所提供的捷徑,這在塑膠組件中已行之有年,且在金屬領域也逐漸廣受運用。即使這幾年來塑膠和金屬列印已成為工業生產的一部分,但是陶瓷列印仍處於實驗室和工廠之間的冒險過程。然而這項技術的優勢是如此吸引人,因此 maxon 仍在五年前開始了初步試驗,目標在於能更快速為客戶提供陶瓷元件原型,以及進行一些真正的開創性工作。Zilm 表示:「有了這種列印機,可以更容易和更早完成前兩三個開發循環。」
經過密集的市場調查之後,maxon 決定採用法國製造商 3DCeram 的列印機,並且是依據 maxon 的本身需求訂製。「對我們來說,主要的銷售賣點是精確度和相當大的 300 x 300 公釐列印區,」Zilm 如此解釋。這臺列印機基於立體光刻造型技術,也就是利用雷射將一種含有黏合劑和陶瓷粉末的光感乳劑固化,然後從下到上逐層構成組件。每一層的厚度大約在 0.025~0.125 公釐之間。每當印好一層之後,列印平臺就會往下移一階。這可以確保在固化過程中收縮平均,並實現高精度和呈現精微的細節。此處不需要支撐結構。3DCeram 系統的特別優勢在於也可以製作非常小的零件,可精細達 50 立方公釐。
視需求而定,陶瓷組件通常是以鋯和氧化鋁製成。這些是技術陶瓷領域中的「基本需要」。兩者都可作為 3D 列印機的光感乳劑。脫脂和燒結方式與陶瓷射出成型的程序相同,因此以 3D 列印機製作出來的生坯可以用和量產零件相同的生產系統處理。視所需組件的複雜程度以及公差大小而定,也可以進行小量生產,是很好的陶瓷射出成型替代方案。
根據 Zilm 表示,這種過程的確有其限制,例如紫外線雷射光束的直徑決定了可製作的最小壁厚。列印完成後會使用壓縮空氣和添加物清潔元件,以移除元件上多餘的材料。小於 0.5 公釐的圓孔無法是像射出成型成品那樣完美的圓形,但對於原型而言,通常足夠了。
一開始就成為開發合作夥伴
今天,客戶只要將檔案以標準 STEP 格式寄來(Standard for the Exchange of Product model data,產品模型資料交換標準)——這在 3D 列印領域中早已司空見慣,之後很快就會獲得報價。訂單確認之後,只需要 10 到 14 天,客戶就可以拿到第一個原型零件。「在過去,這要花上幾個星期或甚至幾個月的時間,而且牽涉到非常高的開模成本,」Zilm 回憶道。
理想的是,客戶從一開始就找上了 maxon。Zilm 解釋說:「我們從第一個想法開始就成為開發合作夥伴,因此能夠參與並影響設計,使產品盡可能適合陶瓷這種材質。」例如將數個元件組合成一個具有最佳化功能的元件。根據 Zilm,這樣的優化過程非常重要,尤其考慮到製作陶瓷所需的商品每公斤價格是鋼的約十倍。「我們必須提供更好的功能來證明這一點,例如透過耐磨性、溫度穩定性或不需潤滑劑。」
增材製造尚未達到其極限。CIM/MIM 能力中心主管 Andreas Philipp 確信:「我們必須開始 3D 思考,脫離以前的傳統方式。」然後就會開啟全新的可能性,屆時 3D 列印就會成為傳統製程真正的替代方案。