maxon Story
The future of UAV: between reliability and connectivity.
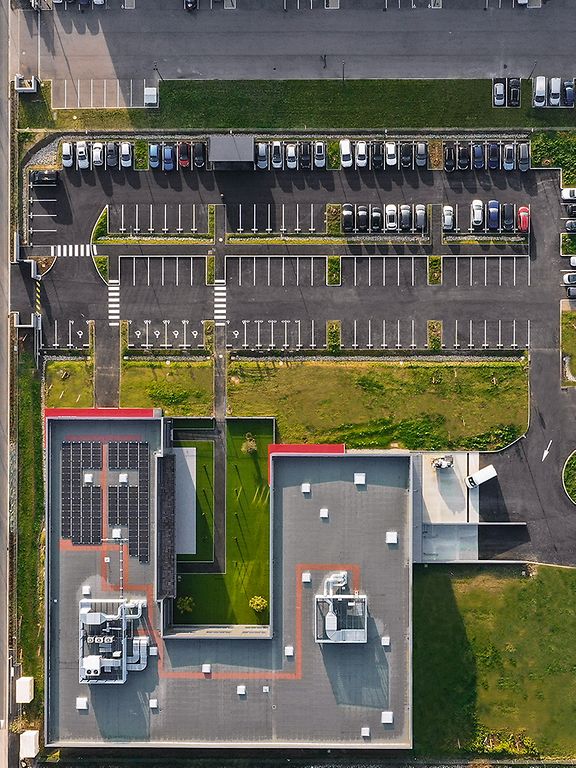
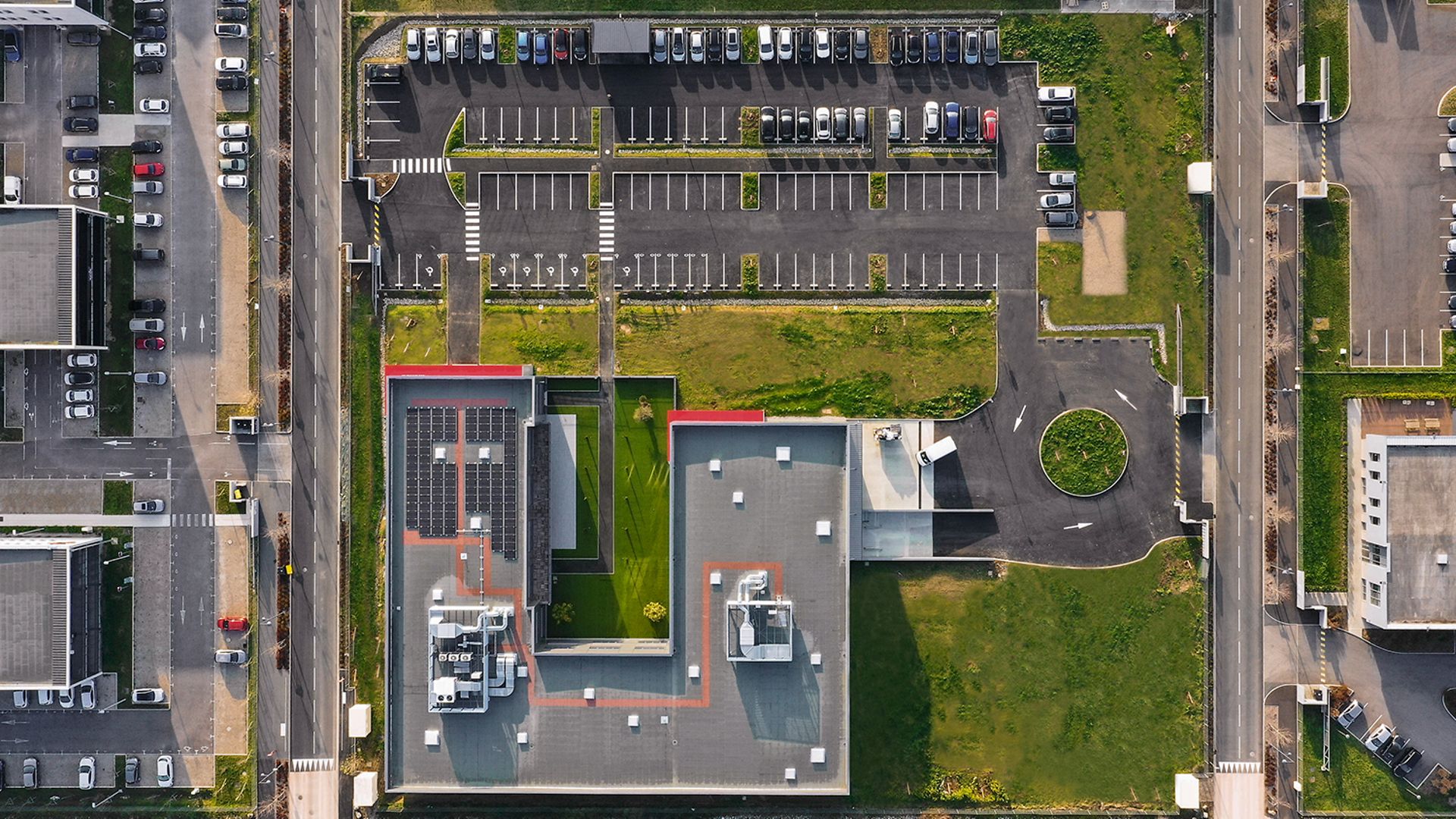
More and more drones used by professionals fly with maxon drives. This Swiss manufacturer’s motors contribute to the safety and reliability of the aircraft. At the same time, there is also a need for system optimization of all the components of the complex drone system. “The major advance is likely to be in the networking, communication, and intelligence of the systems,” says Marco Sicher, Business Development Engineer for Aerospace at maxon.
Mr. Sicher, what is the significance of drones as a field of application for the drive specialist maxon?
For years now, maxon products have been increasingly deployed with success in conventional aerospace applications. Especially in the industrial aerospace market, unmanned aerial vehicles (UAV) have been gaining importance. The market is developing from more of a hobby-oriented environment into an established professional market segment. maxon seeks to take an active role in that, ensuring the safety and reliability of the products and contributing to growth.
Are you breaking new ground with the drone motor?
No, not directly. Although this is a new area of application for maxon motors, we are thoroughly familiar with the high requirements of aerospace and the necessary motor and control technology. The team was able to transfer that knowledge across and make use of synergies. When it came to new areas, such as propeller aerodynamics, we built up a strong network and new know-how.
Are drones with integrated maxon drives already taking off, and who are you collaborating with on that?
maxon drives are being tested by various customers all around the world, both under laboratory conditions and also under real conditions in flight tests in the field. In order to gain important experience and knowledge from flight tests ourselves, the maxon team also built a test drone with the components from our drone range. In parallel, we have used our close connections to universities, our memberships in associations, and new partnerships (such as in the field of propellers) to generate know-how and act as a comprehensive partner.
What requirements does a motor have to meet for drones to be able to carry out the longest missions possible, but also indoor flights?
A long flight time is attained when the entire drive system works together optimally and gets as much energy as possible out of what is stored in the battery. Specifically, this means that the motors have to work as efficiently as possible, and have to be perfectly matched to the propeller, the electronic controller (ESC), and also the flight mission. The effect of the environment on the motor during the different missions can’t be ignored either, such as high and low temperatures and humidity. In contrast, flights in enclosed spaces impose other requirements on the drive system, such as compact size or noise emissions.
Is a new approach needed when developing drone motors?
We are used to developing drives and systems for highly demanding applications. So our approach to development is very suitable. With drone motors, however, you do have to pay special attention to the weight, while also meeting very high requirements for quality and performance. Then there is also the system complexity of the drone drive, with the aerodynamic effects of the propeller and the active cooling from the air flow having a significant influence on the motor design.
Would you call this a product innovation, or is it more about optimizing the overall concept of the drone?
The interplay of all the components is crucial for optimum deployment. So what matters primarily is developing a system in which all the components are perfectly matched to one another. Both the motor technology and the control technology are nothing new for maxon in themselves, but they have been specifically optimized for this new market.
What technological advances are still conceivable here?
New materials and technology are leading to motors that are more and more powerful and compact. maxon is already working on the system optimization of all components. However, the major advance is more likely to be in the networking, communication, and intelligence of the systems. It’s becoming increasingly important that the components of such a complex system can communicate with each other and provide important feedback to the operator.
What is the potential for innovation in drone drives?
There is a lot of potential in the communication capability I just mentioned. We also see a lot of opportunities and possibilities for development in the area of predictive maintenance. That is concerned with targeted, preventive maintenance of the systems and the drive.
Do you also make use of catalog products that are specifically adapted?
In the area of drone drives, meaning the motors that drive the propellers, Maxon has developed new motors designed especially for that purpose, with electronic control to match. However, they are based on motor technology that comes from proven catalog products for many different industrial applications. In other parts of the drone, such as gimbal systems and gripping mechanisms, we use proven catalog products, which we optimize and modify according to customer requirements.
From the point of view of the motor supplier, what is different with unmanned aerial devices (UAV) compared to land-based transport systems?
The safety and reliability of the components is absolutely central. Especially with new technologies that have not yet established themselves with the public and in the regulatory environment, trouble-free operation is imperative, as it is in the aerospace field in general. Reducing the weight of the components for all aerial devices is another important aspect. In combination with the high demands for quality and the environmental requirements, that means walking a difficult tightrope between robustness and weight-optimized design.
Drones are nothing new. What can you, as a component supplier, contribute to the overall further development of drone technology?
Drones have indeed been around for several years, but it’s only now that the big jump is happening from hobby applications to professional applications and services. The professional environment imposes different and, above all, significantly higher requirements on all elements of drones. Here, with reliable, high-quality, and safe products, the component supplier can make a big difference and can contribute to the further development of drone technology.
How closely do you work together with the system manufacturer here?
In all industries, maxon strives to cultivate a close relationship with customers, because that is the only way to achieve the best possible solutions. That applies to drones too. It’s only by working with the system manufacturer that the specific requirements can be identified, and then addressed in development. That goes from simple modifications through to customized drives and controls. In our development process, we also use feedback from the system manufacturer for further development and optimization.