maxon Story
Starter kit for a moon factory
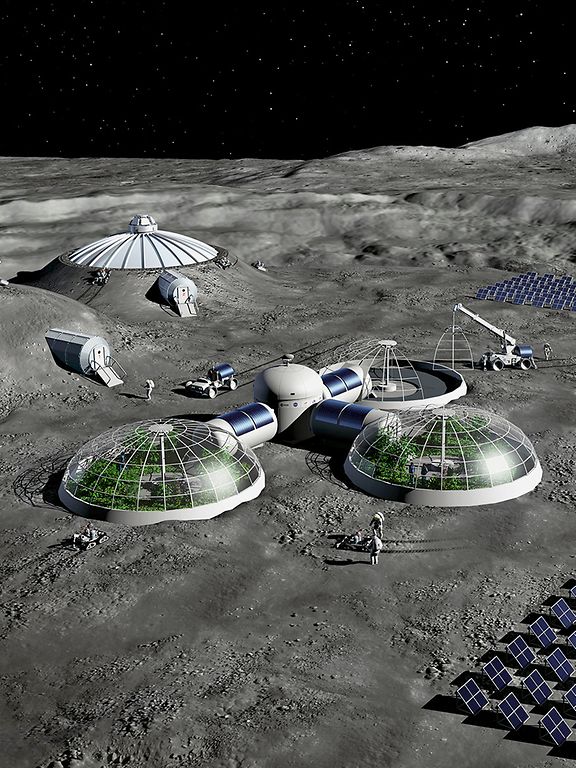
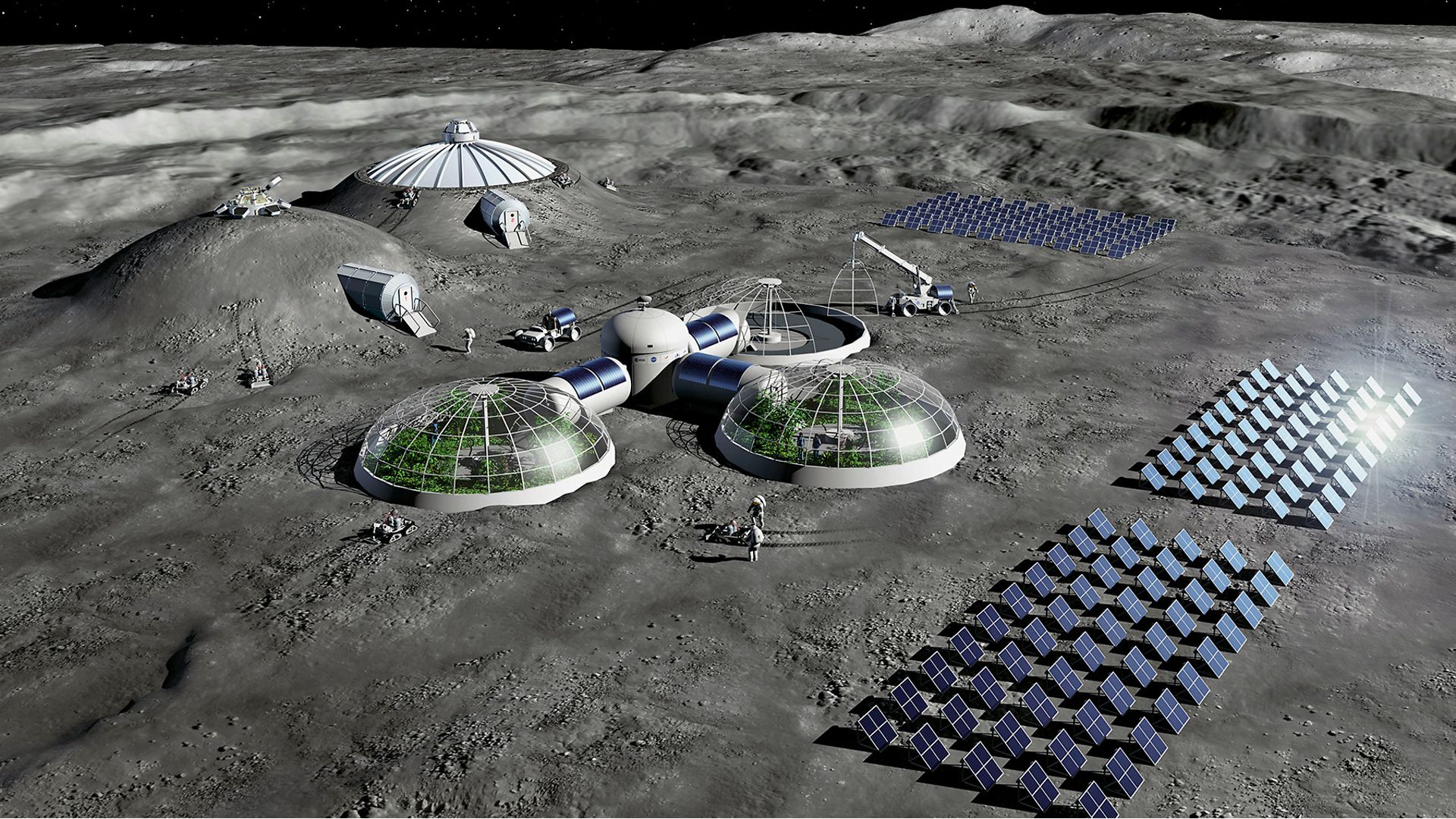
Fiber-based materials are suitable for the construction of a future moon base. In their MoonFibre project, researchers developed a miniature system to produce continuous glass fibers under adverse conditions.
The moon is now well known to us, including its dark side. A Chinese probe landed there in 2019. The ESA and NASA are also pursuing plans for new moon missions. If only the transportation costs weren’t so high. It costs USD 1 million to bring a liter of water to the moon. Simply delivering the materials for a space station the size of the ISS would come to USD 450 billion. So the aim is to build extraterrestrial infrastructure with locally available materials. The lunar surface consists of boulders, rubble, and dust. This porous and loose rock is regolith, and is similar in its chemical composition to basalt, which is suitable for the production of mineral fibers.
The Institute of Structural Mechanics and Lightweight Design (SLA) and the Institute of Textile Technology (ITA) at RWTH Aachen University have developed an automated miniature spinning mill for the production of mineral fibers. After analyzing soil samples from the Apollo and Luna missions, regolith simulants were produced and fibers as thin as 17 micrometers were spun from them.
Versatile
Using the production systems of glass fiber manufacturing as their starting point, the researchers simplified the processes and packed them into a 40-centimeter cube made of carbon-fiber-reinforced materials. In that cube, the moon rock will be melted into glass at 1,450 degrees Celsius. The molten glass will then be drawn out through a nozzle at the bottom of the melting pot to form a continuous fiber. Finally, the continuous fiber will be wound onto a spool. The iBlock should be able to produce up to 180 kilometers of fiber material per hour.
The conventional spinning process is affected by gravity and air pressure. This is where the difficulties lay in adapting it to lunar conditions. In addition to the weaker gravitational force, the extreme temperature fluctuations were also taken into account when designing the plant concept.
The glass fibers obtained from regolith would be very versatile in the construction of a moon base. They could be used to produce fiber-reinforced structures made of concrete and mineral wool, or textiles which, in turn, could be used in the manufacture of clothing, medical equipment, ropes, and cables. Wool material and nonwovens would be used to produce filters, heat and sound insulation, and radiation shielding. There are even plans to cultivate plants on substrates made of moon fibers.
Scalable to a system
The cube, which weighs only 17 kilograms, can be scaled up to form a system or a small factory. Multiple units, interacting via interfaces, would perform various different functions. In a study conducted by the German Aerospace Center (TLR), which looked into setting up a moon base, these moon fibers were a central component.
The MoonFibre team was one of the three winning teams of students in the ESA project IGLUNA, coordinated by the Swiss Space Center, which took place in Lucerne in July 2020. By the way: the winder and the thread guidance are driven by brushless EC 45 flat and EC 20 flat motors (the latter with an extended planetary gearhead). Height adjustment is performed using another actuator, made up of a brushed DCX 19 S motor, a low-backlash planetary gearhead, and an ENX incremental encoder for positioning.
Young Engineers Program
With its Young Engineers Program (YEP), maxon supports innovative projects with discounted products and technical advice.