maxon Story
Pipe inspection with top power density.
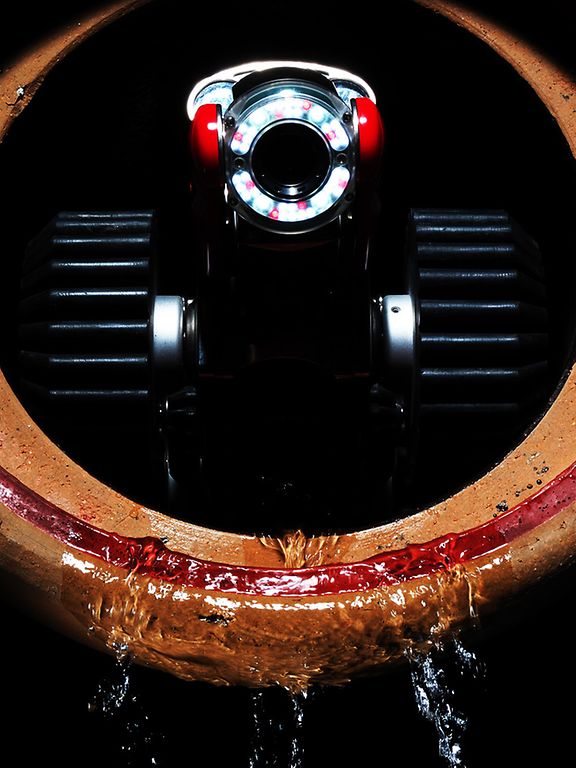
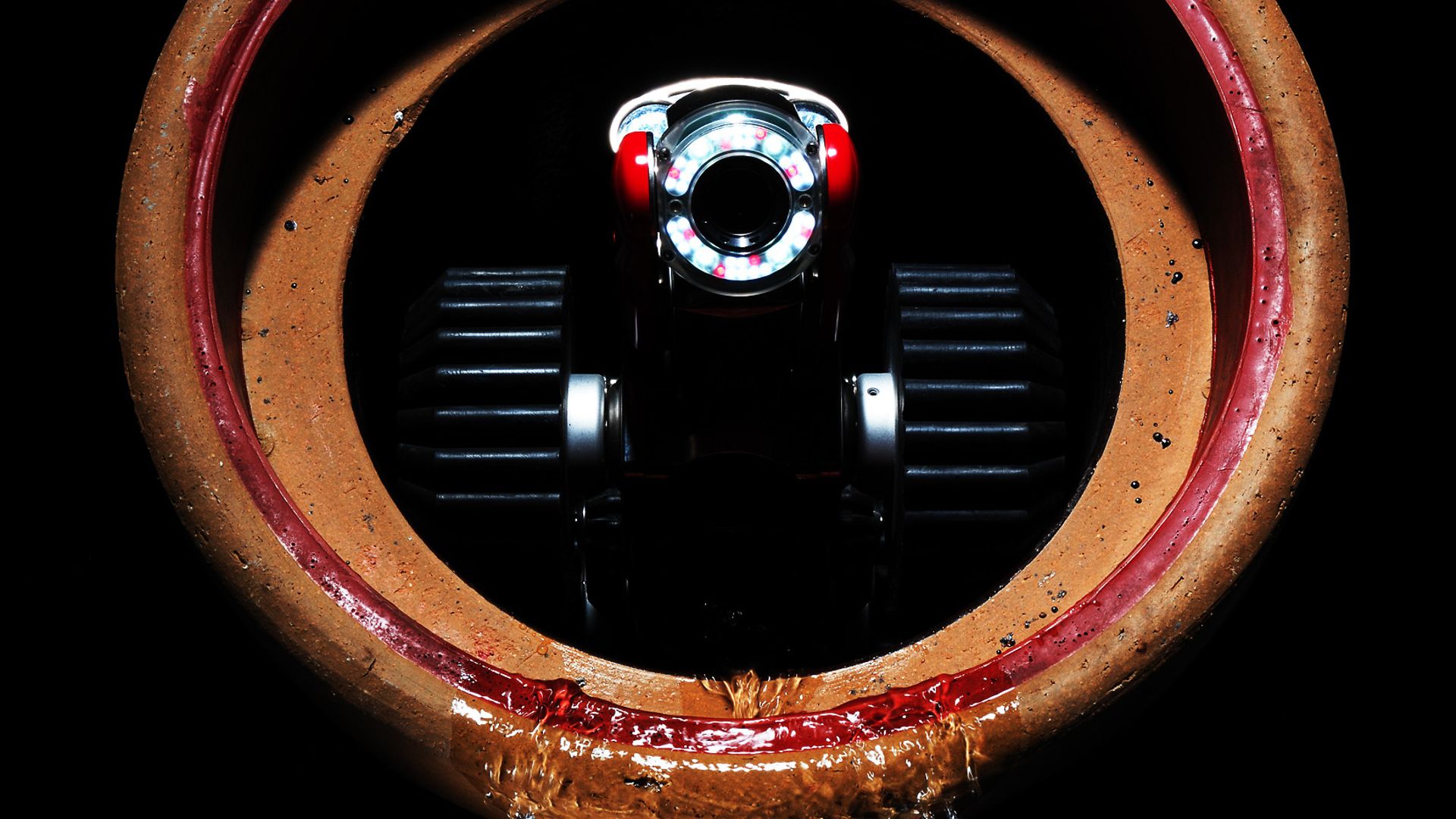
Imagine the drain is clogged and not a single drop is flowing down any more. A common problem – the cause can be hidden in the far corners of a sewage system. This is where inspection robots come into play to hunt for the cause. Motors by maxon motor provide the robotic vehicles with a precision drive, among others uses.
Robots are increasingly being used for fully automated tasks that are too dangerous, monotonous or when it would be unreasonable to ask a human to perform the task. For example, today innovative systems such as inspection robots for sewage ducts are used worldwide for high-precision damage detection. There are even inspection robots that can climb 90 m high onto wind turbines to inspect the rotor blades of the wind energy generators. Underground sewage pipelines that stretch across many kilometers are also highly complex systems. These systems have to function reliably at all times. Regular inspection is therefore mandatory, to avoid damage caused by corrosion, cracks and mechanical wear. Yet the narrow, labyrinthine sewer systems are frequently inaccessible for humans – this is where only technical equipment can save the day.
Today many different devices are available, for everything from inspections to remedying faults and breakdowns. Depending on the type of application, the sewer robots come in different sizes and with different tools and other specific features. From simple inspection units to complete systems, iPEK International GmbH based in Sulzberg (Germany) and Hirschegg (Austria) provides a wide range of robots for pipe and sewer inspections. The company, which was found in 1988, develops camera systems and driving units for sewer inspection, for example the modular “ROVION®” inspection system.
The driving units are characterized by ease of steering and the short wheel base means that obstacles and stairs are no problem. Two different driving unit sizes and a separately available carriage make it possible to inspect pipe systems with inner diameters of 100 mm to 1000 mm. The remote-controlled ROVION is equipped with a color camera with shutter function, which is necessary for lens protection. Furthermore the bright LEDs help to light up even the darkest corners. Additionally products such as the “SUPERVISION®” and “ROVVER®” system are available for use in pipes with diameters of 100 mm or larger. The “SUPERVISION®” system has also been designed for inspecting deep wells, shafts and boreholes.
maxon motors for in-pipe use
The drives for these sewer robots have to withstand the high loads inherent to the difficult conditions. The requirements therefore include a very high power density, to allow smaller sizes. This is an important criterion especially for applications in narrow spaces. Furthermore the motors have to have smooth power curves, to allow accurate motor control. For the planetary gearhead, high efficiency is mandatory. And the motor-gearhead units used have to have an excellent build quality, as they will be subjected to high loads. Motors from maxon motor meet all these requirements. The maxon motors are used mainly as drive motors for the driving units of the ROVION®, SuperVision® and ROVVER® inspection systems. All motors are coupled with a matching gearhead.
The largest maxon motor used in iPEK products is the brushless EC-max 30, with a power of 60 W. The ROVION® driving units are each equipped with one EC-max with a diameter of 22 mm. This drive is also the smallest motor used in the driving units. Each driving unit is equipped with two drives (left, right), to enable steering of the vehicles. Some of the various camera heads for the sewer robots are equipped with medium-sized motors, as rotation and pan motors (panning, rotating and focusing). The smallest combination used consists of a maxon RE 6 DC motor – an energy-efficient direct current motor with a diameter of only 6 mm. This drive is used in a highly flexible camera head, in combination with a planetary gearhead. The camera heads with LED lighting allow inspection of every nook and cranny of the pipeline system, as they have a pan range of ±135° and can rotate fully around their own axis. Other motors are used for the lift drive of the camera lifter.