Expert Blog
New motor speed measurement technique optimises control without encoder
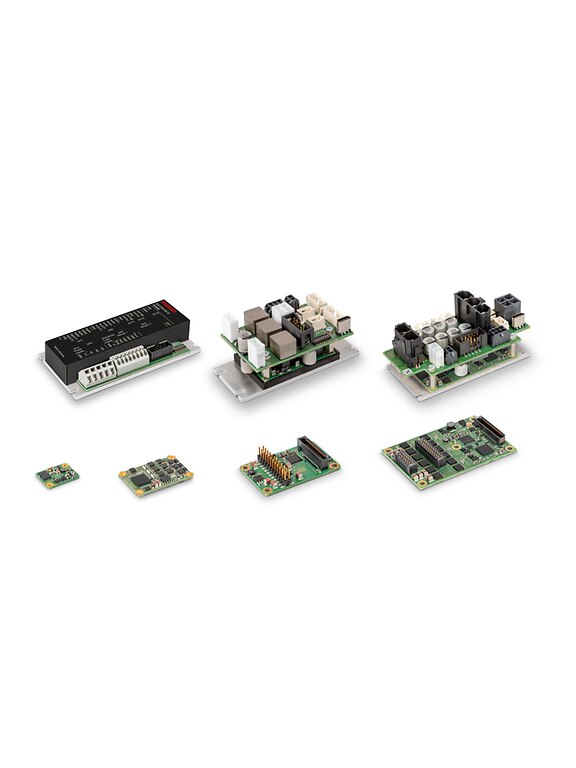
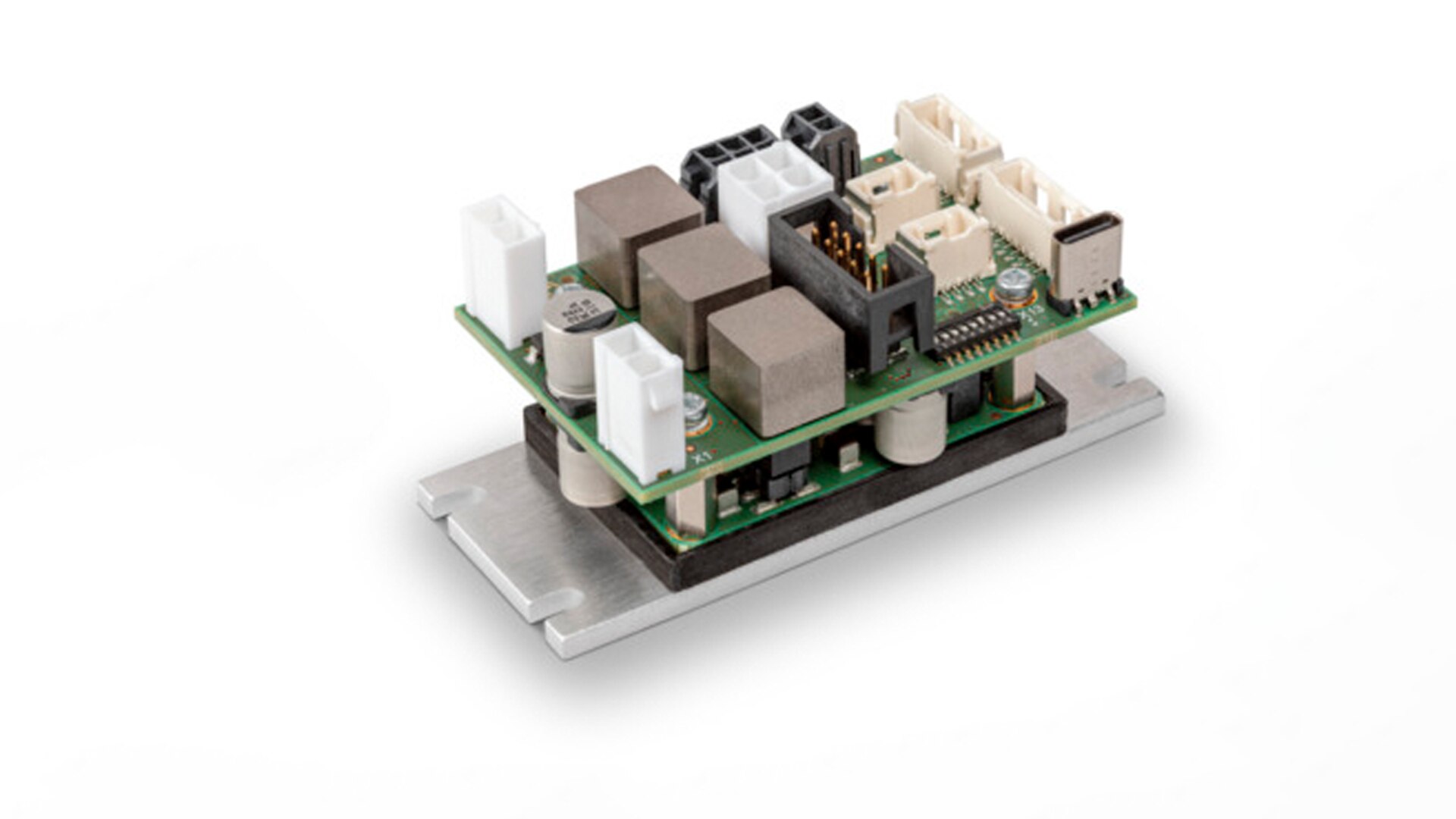
maxon has released a new speed measurement method for brushless DC motors (BLDC) to optimise control precision without requiring an encoder. The new method is based on an advanced approach to Hall sensor feedback that enhances speed control precision while minimising the cost and footprint of application design. The new control method is now included across maxon’s ESCON2 speed controller range.
maxon’s new speed control method, used for the first time in ESCON2, analyses the switching edge distribution of a BLDC motor’s Hall sensors during its first motor revolutions to generate virtual, precise sensor information. Due to their operating principle, Hall sensors typically provide only a low resolution per rotor revolution and the switching edges are not perfectly distributed over one revolution of the motor shaft due to manufacturing tolerances. However, maxon’s new patent-pending technique means that from a speed of just a few hundred rpm, speed stability and control are comparable or an improvement on systems based on encoder feedback.
maxon’s tests show that the speed control of the ESCON2 with Hall sensor feedback is significantly smoother than standard servo controllers supported by encoders, even at speeds as low as 300rpm, which also results in higher energy efficiency. Crucially, the elimination of the encoder reduces application cost and footprint, and also enables a faster set up.
The field-oriented control, which regulates the magnitude and angle of the stator’s magnetic field to optimise dynamism and efficiency, generates sinusoidal motor currents over the entire speed range up to 120,000 rpm. Combined with the new speed control algorithms, supported by a 10 kHz speed control rate, 50 kHz current control rate, and overload-resistant power stages, this enables ESCON2 controlling maxon BLDC motors to follow high accelerations and precise motion profiles. These important features enable the host application to achieve increased productivity with greater precision and accuracy.
ESCON2 is available for embedded electronic design as well as ready-to-connect solutions for cabinet or close-to-motor installation. Nano, Micro, and Module PCB-based formats of maxon’s ESCON2 motor speed controller are for direct embedded integration within compact and hand-held devices. The ESCON2 Nano is the most compact controller in the range, measuring just 23 × 16 × 4.5 mm and weighing only 2.5g for 2A output current with 24V operating voltage. ESCON2 controllers for embedded electronic integration also extend to 5A, 12A, and 30A continuous output current. Ready-to-connect formats of ESCON2 are also available. The compact and housed versions of ESCON2 include connections and are designed for integration close to the motor or in a cabinet or on-machine.
To optimise flexible connectivity and design integration, ESCON2 features a variety of analogue and digital I/O along bus interfaces including USB, serial interface/RS232 and CAN (CiA402). Meanwhile, rapid set up is achieved via maxon Motion Studio that features a Startup wizard to guide configuration including I/O functions, plus a Regulation Tuning wizard that automatically determines control parameters.
Find out more here about maxon ESCON2.