maxon Story
Multi-axis motion control drives pipe-based robots
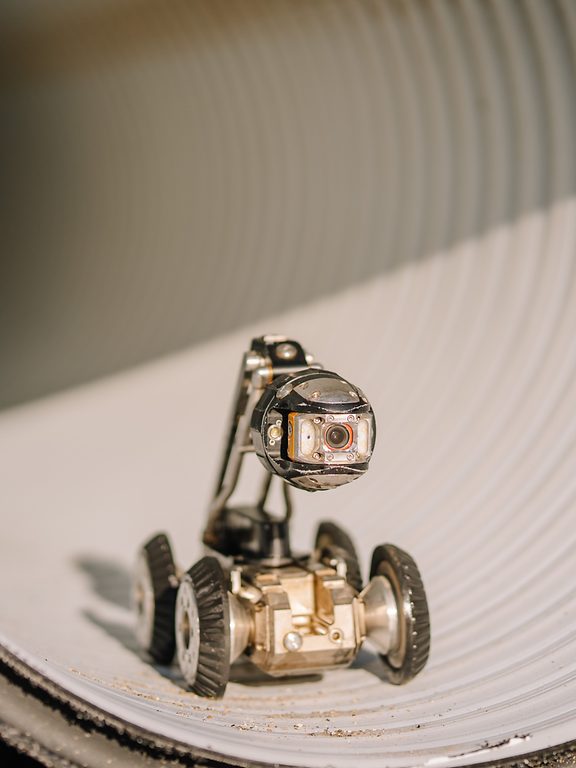
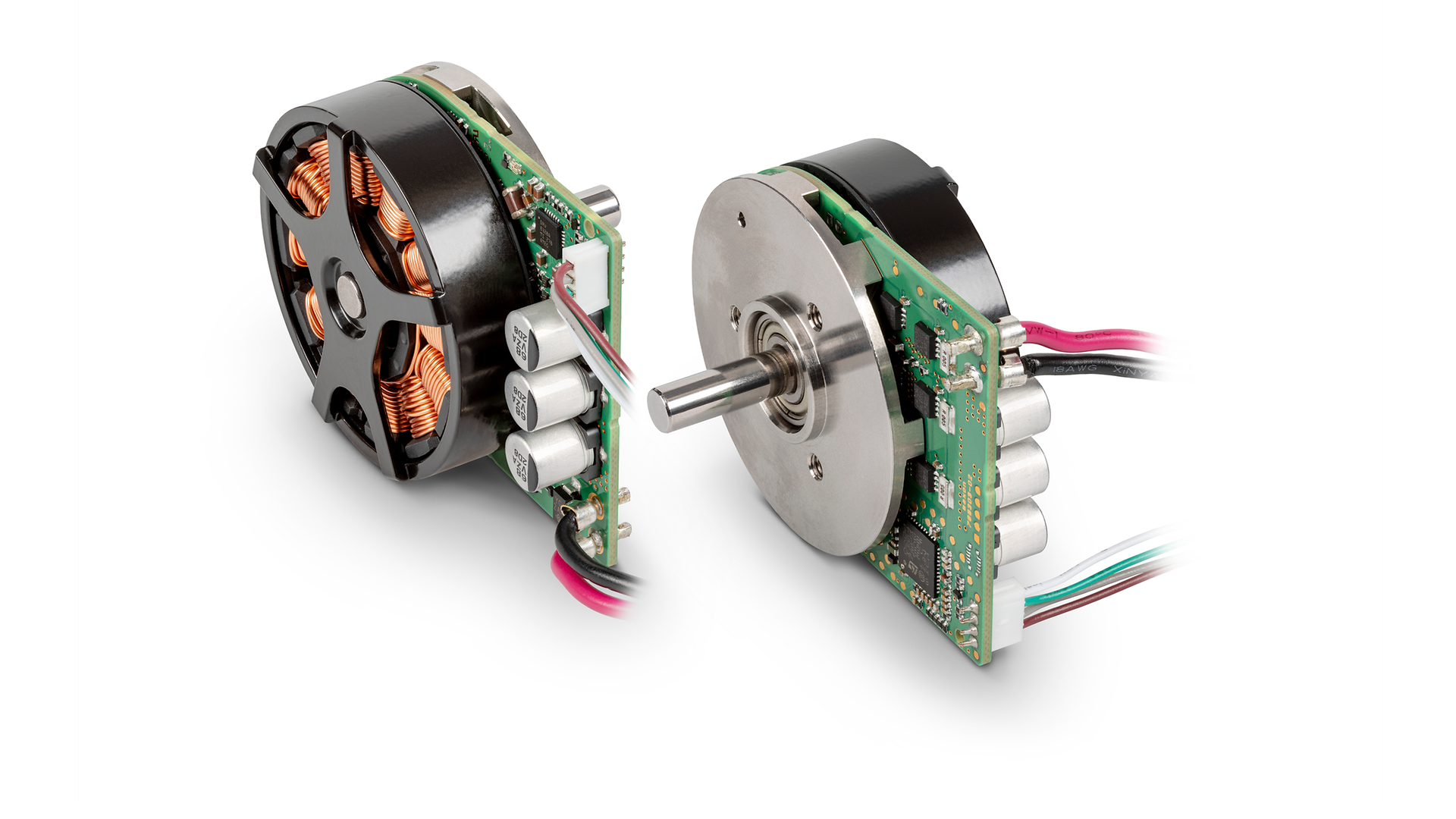
Surveying and maintaining underground pipes can be complex and resource intensive. To streamline the process, construction and facility management teams are increasingly turning to robots that can provide inspection as well as repair.
To propel these robots and drive their tools, all within a space-constrained environment, compact and reliable multi-axis motion systems are essential. maxon engineer, Tamas Hertelendi, explains.
Inspecting underground pipework where human access isn’t possible, techniques using manually inserted rods or probes are time consuming and expensive. Challenges in access can mean that a comprehensive survey covering the whole system is difficult to achieve. And, if repair is required, approaching the specific section usually requires entry by digging from above.
Capabilities of Pipe-Based Robotic Systems
Across pipe networks involved in construction projects, as well as already installed builds and infrastructure, survey teams and maintenance contractors are increasingly turning to robots to achieve more in-depth reports. Not only can robots survey pipe installations significantly faster than a conventional approach, but with an automated capability, they can also free up the need for a skilled operator.
To achieve a survey, mobile robots integrate a variety of sensors, such as high-resolution cameras to provide visual inspection, laser profiling to confirm pipe geometry, acoustic sensors to detect leaks, and ultrasonic sensors to measure pipe wall thickness. These mini vehicles can also integrate sonar to survey into the ground beyond the pipes.
In addition to their survey role, pipe-based robots can also perform maintenance tasks. In combination with a sensor array, these mobile machines can host tools to clean pipework or prepare specific areas for repair, alongside cutters and grinders, as well as welding equipment. In future projects, we could also see these robots use their tools as part of the actual construction process, such as digging outside of their host pipe and deploying concrete to build supporting structures.
The reliance on motion
A variety of mobile robots can be used within pipes, depending on the intended environment of operation and pipe architecture, with common designs including rail-mounted robots, crawlers that operate with tracks, as well as wheeled robots. To propel the robots through a pipe network, control the movement of their sensor apparatus, and actuate their tools, a capable motion system is an essential requirement across all robot designs.
Central to the coordination of these motion requirements is a multi-axis motion controller. Mobile robots can have independently driven wheels or a differential system to calculate wheel speed based on turning radius, so real-time coordination of independent motor axes is crucial. Tools might also need to coordinate with the motion of the robot, while robotic arms hosting end effectors integrate multiple joints that need to operate in concert.
These requirements mean that in addition to a multi-axis capability, a motion controller must integrate a real-time, deterministic communications protocol, such as CANopen or EtherCAT, to achieve the necessary speed and precision in motion coordination.
Space constraints
Yet a key challenge for designers of these mobile robots is the confined environment of a pipe network. The space constraints demand a robot with a compact footprint that must also reach the desired level of operational performance and reliability.
The need to meet both these requirements was presented during a recent project to develop a tunnel-based inspection and maintenance robot. The initial prototype integrated an industry-scale motion controller to coordinate the wheels, which were driven by four, standard DC motors. The design also featured two further DC motors to actuate its robot arm that would host various tools.
The footprint of this set-up, which was sufficiently compact for a factory cabinet yet oversize for a mobile robot, limited the size of battery the robot could accommodate. This meant relatively frequent battery recharge replacement, increasing the overall time the robot would spend on a task.
While aiming to minimise space, lower torque, smaller motors were also used on the prototype. However, the hard-run motors were liable to overheat within just minutes of operation, forcing the robot to cease operation for an interval – or risk failure.
The robot development team engaged maxon for a solution, which would be based around the maxon MiniMACS6 multi-axis motion controller. At 140.5mm wide and 109.5mm long, the freely programmable master motion controller instantly achieved a significant size reduction, as well as reducing mass down to just 370g.
As the robot arm was only used when the robot was stationary, maxon’s engineers proposed that the wheel-driving motors could also be switched to control the robot arm. As a result, the six, standard DC motors were replaced by just four, high-torque versions of maxon’s ECX flat brushless DC (BLDC) motors, paired with maxon GPX gearheads.
Optimising energy and thermal efficiency
With a 32mm diameter, the ECX flat motor design reduced dimensions and mass while achieving the required torque output. The developer also revealed that in real-world conditions, the robot could encounter pipes set a gradient, which would increase the load faced by the drive system. This demand would be handled by the motor’s 34.1 mNm maximum continuous torque, achieved thanks to its winding design and high-performance magnets which would help to optimise torque density.
Crucially for the robot designer, the total reduction in size and mass enabled them to integrate a larger battery. Moreover, upgrading the original motors with a high efficiency BLDC design reduced the demand on the power source. Drive system efficiency was further enhanced by the GPX gearhead, designed to optimise power transfer and minimise losses. These advantages will enable the robot to operate for longer intervals within a pipe before requiring battery recharge, increasing the productivity rate of inspection and maintenance.
The motor is also highly thermally efficient, and the open design of the ECX flat range allows it to operate at high speed while ensuring heat dissipation, resulting in normal running temperatures, even within the robot’s compact housing. This minimises the potential of overheating and has significantly improved the reliability of the robot’s prototype - as well as removing the need for pauses to allow cooling.
Motion programming
Programming to coordinate the motion of the robot has been supported by maxon’s multi-axis motion control engineers. While offering expertise in motion development, the team is also able to draw on a vast library of applications. This portfolio of motion programming can be quickly adapted to achieve the specific coordination required for each project.
The robot designer’s in-house development team have also been able to quickly create their own motion moves through maxon’s user-friendly ApossIDE (Integrated Development Environment). As the interface for programming and debugging, Aposs IDE’s in-built motion control functions for positioning, speed control, and synchronisation, also reduce the need for complex coding expertise.
Development took place using ApossC, a C-based language, which the team was already familiar with. As the motion control solution is provided with a Software Development Kit, access to motion libraries, and technical support in application development, this provided the team with everything they needed to programme the robot’s motion, which further reduced the cost of the project.
Growing reliance on pipe-based robots
While R&D into the potential of mobile robotics continues, including their deployment within the confines of a pipe network, the advantages of compact, efficient, and reliable drive systems will remain vital.
To achieve these demands, development into torque-dense brushless DC motors, combined with high-performing multi-axis motion control, continues to advance.
Find out more here about maxon’s multi-axis motion control solutions.