maxon Story
Die vierte industrielle Revolution
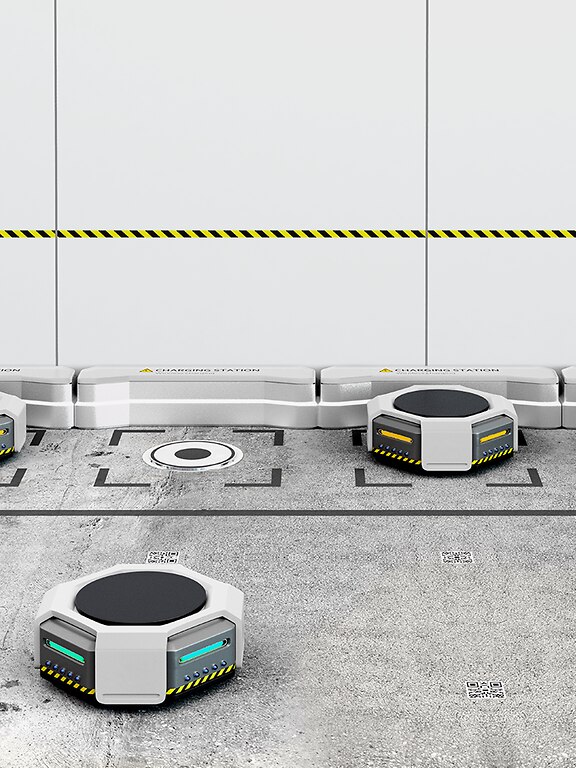
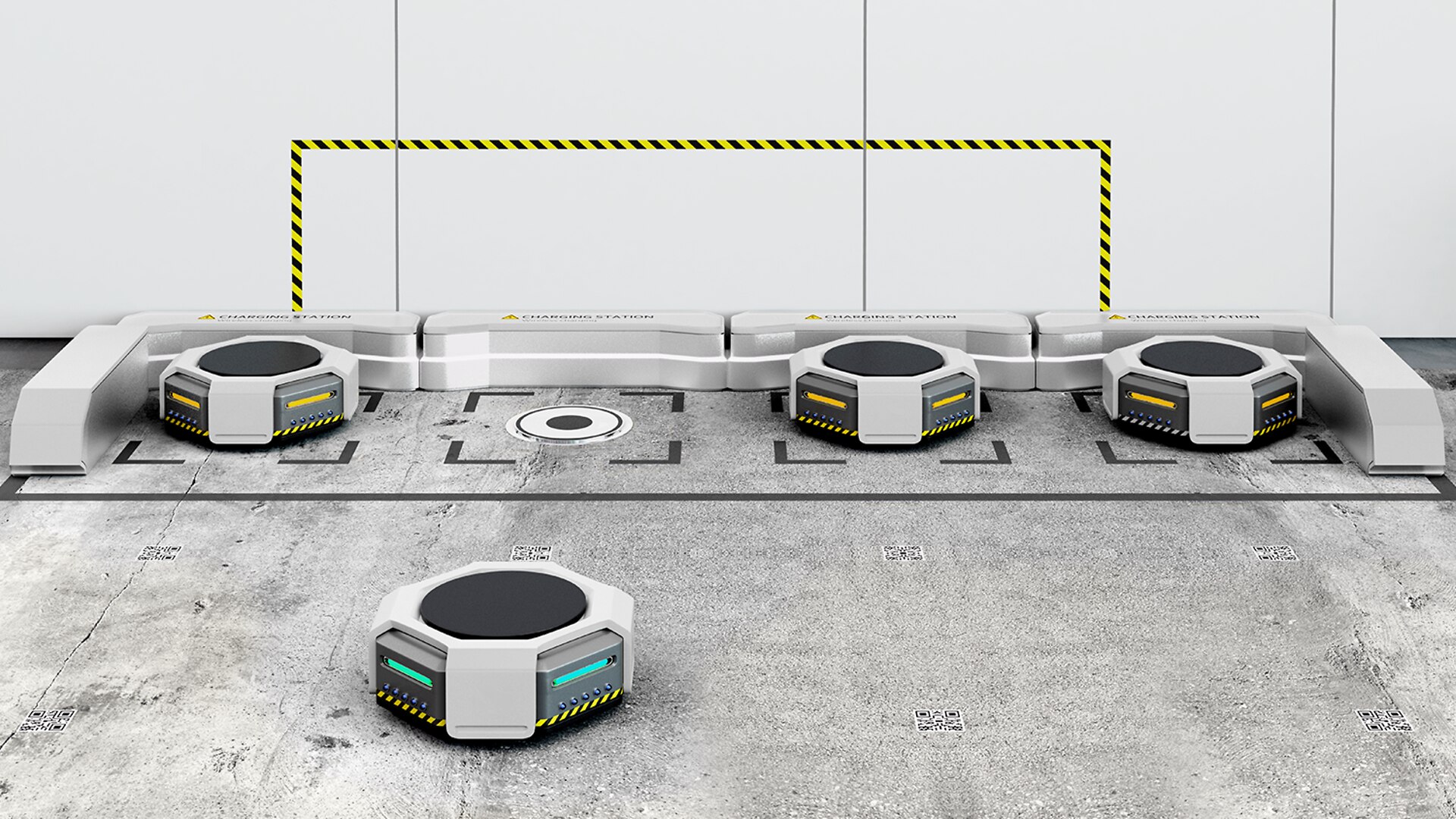
Drei industrielle Revolutionen hat die Welt seit 1760 bereits erlebt. Heute stehen wir an der Schwelle zur vierten, der Industrie 4.0, auch bekannt als digitale Fertigung. Was bedeuten diese Änderungen für Unternehmen und Belegschaft?
Zwischen 1760 und 1840 vollzog sich in der ersten industriellen Revolution der Übergang von der manuellen Fertigung zur Nutzung von Dampf- und Wasserkraft.
Ausgelöst durch den Bau von Eisenbahnen und die Elektrifizierung von Fabriken fand dann von etwa 1871 bis 1914 die zweite industrielle Revolution statt. Mit ihr nahmen auch Telekommunikationsnetzwerke ihren Anfang, beschleunigten den Ideenaustausch und führten damit zur Entwicklung der ersten modernen Produktionslinien.
Die dritte Revolution war die digitale Revolution am Ende des 20. Jahrhunderts mit der Erfindung des Computers. Diese programmierbaren Maschinen konnten sich wiederholende, mechanische Aufgaben ausführen und damit eine enorme Steigerung der Produktion und Senkung der Arbeitskosten verwirklichen.
Und nun stehen wir vor der vierten industriellen Revolution, die auch als digitale Fertigung, Industrial Internet of Things (IIoT) und Industrie 4.0 bezeichnet wird. Was ändert sich dadurch für das Geschäft und die Arbeitskräfte?
Welche Herausforderungen stellt die Industrie 4.0?
Wie bei jeder Revolution gibt es auch hier politische, wirtschaftliche, organisatorische und soziale Herausforderungen zu bewältigen. Politisch: gemeinsame Regulierung und rechtliche Fragen. Wirtschaftlich: kostenintensive Umsetzung zugunsten der Erste-Welt-Länder. Organisatorisch: Zuverlässigkeit, Sicherheit, Schutz des geistigen Eigentums, Ausbildung der Arbeitskräfte. Und schliesslich sozial: Bedenken und Misstrauen in Bezug auf Datenschutz und Überwachung, Zurückhaltung bei den derzeitigen Mitarbeitenden wegen Angst vor Veränderungen und Arbeitsplatzsicherheit.
Die jüngste Revolution automatisiert den Datenaustausch durch fortschrittliche Mensch-Maschine-Schnittstellen mit Kommunikation in Echtzeit. Hinzu kommen Big Data und digitale Verarbeitungsplattformen, die eine grössere Transparenz für Betreiber schaffen, die die Gesamtaufgabe definieren und optimieren und den Systemkomponenten Autonomie durch Selbstüberwachung einräumen. Das bietet enorme Flexibilität. Maschinen können Fehler vorhersagen und bereits bevor diese eintreten Wartungsarbeiten anpassen oder planen. Für Unternehmen bedeutet dies Kostenersparnisse, denn die Ausfallzeiten werden reduziert, die Gesamteffizienz wird gesteigert und der Personalbestand kontinuierlich verringert. Unter den Arbeitnehmenden wächst jedoch das Misstrauen und die Besorgnis, dass der eigene Arbeitsplatz verloren geht. Bei jedem Automatisierungsschritt in der Geschichte der industriellen Revolution passierte es, dass manche Arbeitsplätze überflüssig wurden. Neue Arbeitsplätze, die durch die Innovation entstehen, erfordern jedoch andere Qualifikationen und damit eine Umschulung der Belegschaft.
Wie würde das aussehen?
Es gibt enorme Chancen für alle Bereiche, aber sehen wir uns einmal an, wie die Fabrik von morgen aussehen könnte.
Maschinelles Lernen
Autonome mobile Roboter (AMR) arbeiten an verschiedenen Tagen auf unterschiedlichen Routen. Dabei können sie ihre Route je nach Bedarf in der Lagerhaltung und Intralogistik eigenständig anpassen und ändern. Mit einer Reihe von Sensoren ausgestattet, finden sie sich zurecht, ohne einander oder der menschlichen Belegschaft in die Quere zu kommen. Sind Wartungsarbeiten nötig, stellen die AMRs selbständig eine Diagnose und besuchen die Werkstatt für präventive oder kritische Instandhaltungsarbeiten.
Smart Factory
Der Begriff «Intelligente Fabrik» ist synonym mit der Industrie 4.0. Hier werden cyber-physische Systeme (CPS) eingesetzt, bei denen ein computergestützter Algorithmus einen Mechanismus steuert. Cyber-physische Systeme sind auch mit dem Internet der Dinge verknüpft, wo mit Sensortechnik ausgestattete Geräte den alleinigen Zweck haben, Daten über das Internet auszutauschen. Selbstfahrende Autos oder Drohnen, die ihre Umgebung virtuell wahrnehmen, sind Beispiele für CPS. Anstelle von Warenlagern und Fabriken, in denen Lieferungen in einem von Menschen durchgeführten Ablauf entladen werden, liefert ein Lkw genau die Rohstoffmenge, die über eine automatische Datenerfassung ermittelt wurde. Produkte werden digital entwickelt und getestet. Die intelligente Fabrik arbeitet von der Anlieferung bis zum Endprodukt mit minimaler Aufsicht.
Unsere Kunden stehen oft an vorderster Front des industriellen Wandels und so haben wir es uns zur Aufgabe gemacht, Produkte zu entwickeln und herzustellen, die die Innovation vorantreiben.
Mit der Entwicklung einer kompletten Produktreihe kompakter und modularer Motoren bietet die maxon Group AGV- und AMR-Designer:innen maximale Gestaltungsfreiheit. Die IDX-Antriebslösungen erfüllen die anspruchsvollsten Anforderungen: Sie bieten 20 Prozent mehr Leistung als die derzeit auf dem Markt erhältlichen Lösungen.