Expert Blog
When does a DC motor need inertia?
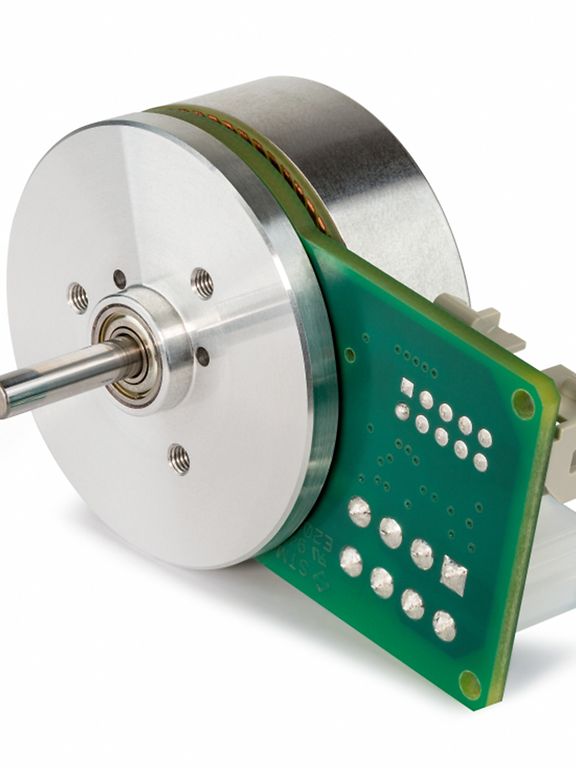
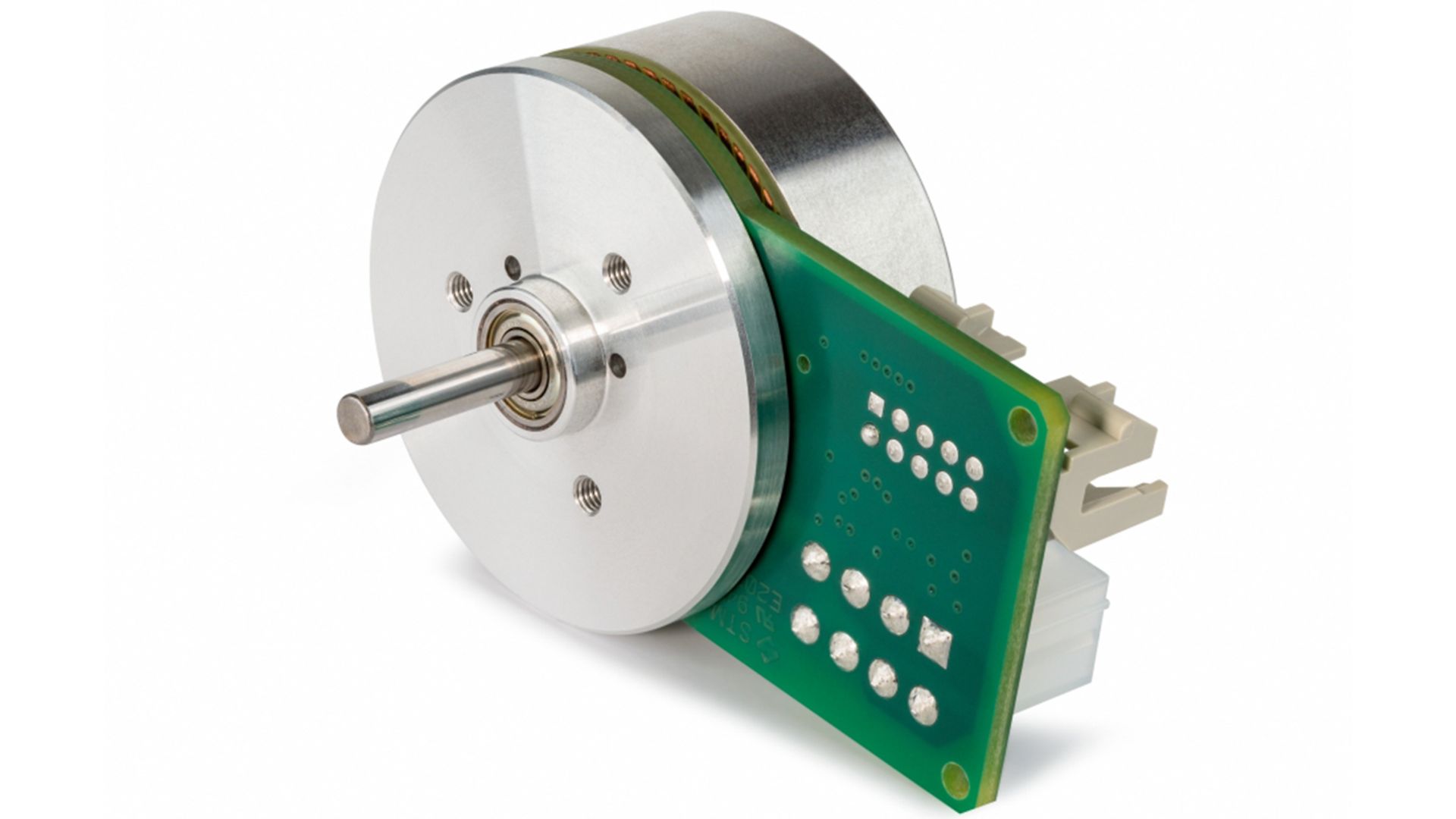
New brushless DC motor with customized inertia wheels.
Three-phase brushless DC motors are typically controlled using Hall sensor feedback, encoders, or a mixture of both. This allows the controller to apply power to the motor windings instead of using a traditional brush and commutator assembly. Within the sphere of brushed and brushless DC motor designs, there are also coreless and iron cored DC motors.
Designs with a very flat profile, often called pancake motors, with high torque density, have a magnetic detent that can sometimes lead to speed ripples. This becomes particularly evident when extremely low speeds are required, and sometimes under very light load conditions.
This is where the EC45 motor with inertia wheel can excel. Available in a selection of voltages and power levels, this 45 mm diameter 3-phase brushless DC motor can be fitted with a specially designed inertia wheel that helps to smooth speed inconsistencies caused by application influences and motor characteristics. This motor shown is a 30W 12V pancake motor with an internal 2048cpt encoder used for speed regulation and Hall sensors used for commutation.
The flywheels are pressed and laser welded to a rear shaft extending from the external rotor. The motor is perfectly suited to laboratory and instrument applications where precise speed control is necessary.