maxon Story
A new docking system for space rendezvous
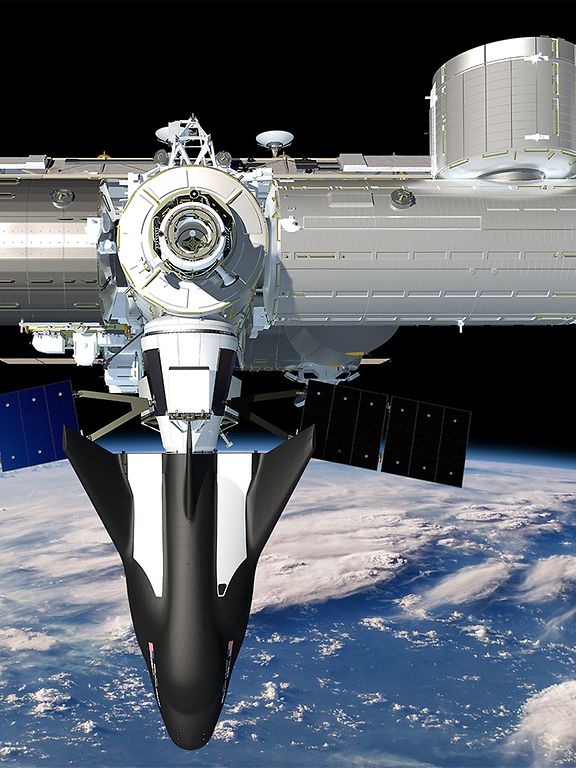
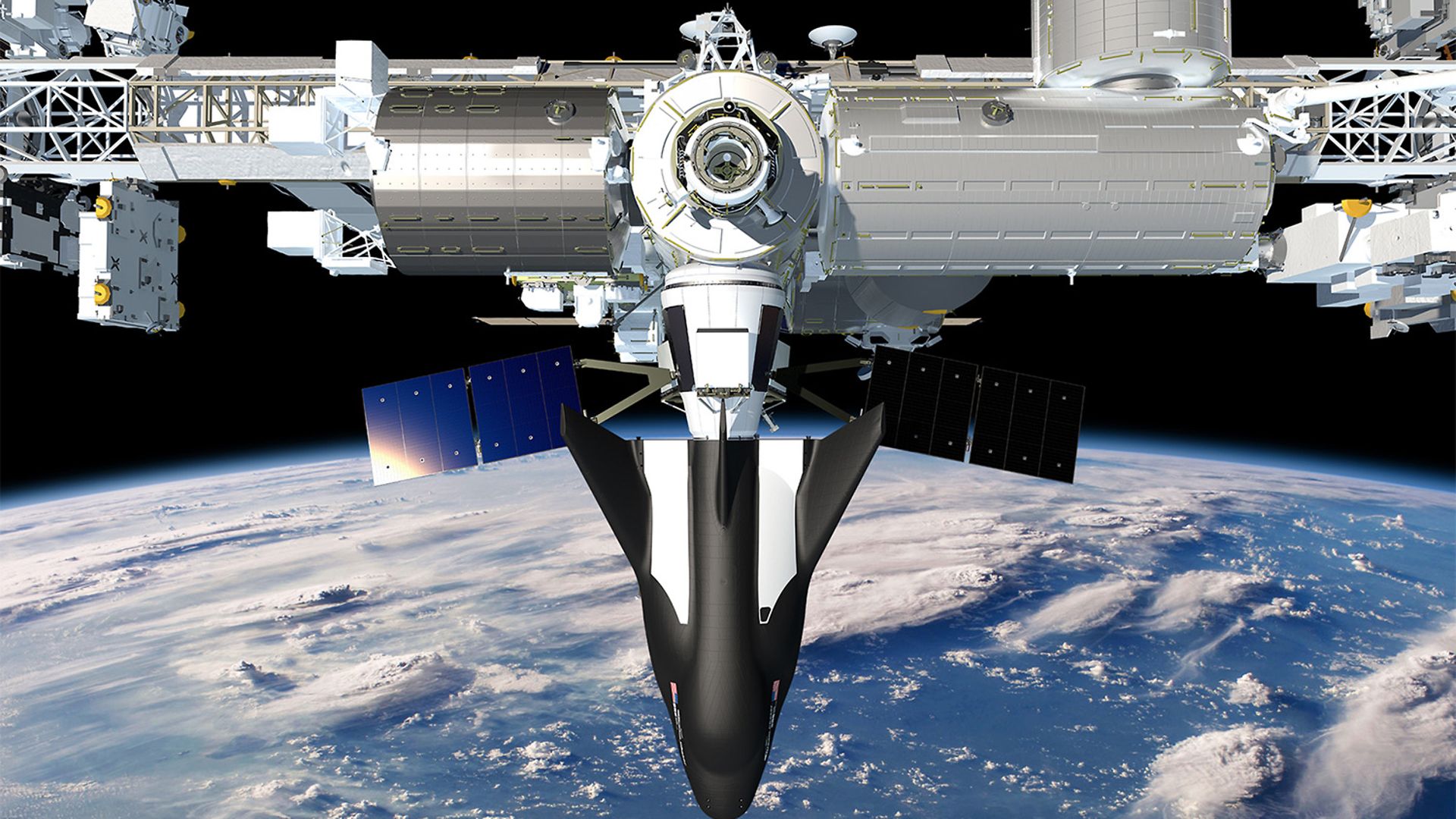
The European Space Agency (ESA) is working on a new system to enable easy docking between two spacecraft. maxon developed two special drive systems for this purpose.
Even though it's been done many times before, the docking maneuver between two objects in space is always a delicate and potentially dangerous procedure. The speed is extremely high (about 28,000 km/h in case of the ISS), and corrections are difficult. For example, when the two objects are about to meet, maneuvering thrusters can no longer be used, since their exhaust plumes can cause damage. To prevent harm, cargo transporters are caught by a robotic arm installed in the International Space Station (ISS) and berthed manually. Manned spacecraft on the other hand dock directly in a computer-controlled process.
This type of docking maneuver is going to become easier and safer in the future, so the European Space Agency (ESA) has commissioned its industry partners to design a new docking system called IBDM (International Berthing and Docking Mechanism). This conforms to the International Docking System Standard (IDSS), a standard on which the leading space agencies worldwide have agreed. The system will therefore be compatible with the ISS and most other spacecraft. The mechanism's first missions will be with the Dream Chaser, a craft that looks like a compact version of the Space Shuttle and will soon perform cargo flights to the ISS. The craft is being developed by the Sierra Nevada Corporation.
Docking energy is absorbed
The IBDM is an androgynous coupling system. This means that the connector is identical on both sides. It consist of a hard inner ring (Hard Capture System) and a soft outer ring (Soft Capture System) that has six degrees of freedom and force sensors. The outer ring first absorbs the docking energy. Then the final airtight connection is made and secured by mechanical hooks which pull the two spacecraft tightly together.
SENER is in charge of developing and installing the Hard Capture System. The company is currently working on the qualification model, which is due for testing in 2020. “Then the IBDM needs to be used as quickly as possible on a supply flight for the ISS,” says SENER's Gabriel Ybarra. One of the next steps would be to use it in NASA's Lunar Space Station, which is planned to go into orbit around the moon and could serve as a launch point for manned missions to Mars in the future.
Dual systems for maximum safety
This is a challenging project for the engineers at SENER: “We first needed to fully understand all the requirements set by ESA and NASA and figure out how to fulfill these requirements. And especially with regard to safety, because the docking mechanism can also cope with manned flights.” As well as being lightweight and delivering the required torque, the electrical drives that are used must also be extremely reliable. This is why SENER has been working with the drive specialist maxon for several years.
For the hard capture system maxon developed an EC 32 flat motor with two windings and a GPX 22 UP planetary gearhead (above). There are twelve maxon drive systems power the locking hooks. Each consisting of two brushless EC-4pole 30 motors and a GPX 42 UP gearhead (below).
maxon's engineers have developed two drives for SENER that can be used to execute a huge variety of functions. This first drive consists of two brushless EC-4pole motors and a GPX UP gearhead. Twelve of these actuators power the locking hooks in the IBDM docking mechanism. The second drive combines a flat motor with a planetary gearhead. It is used in eleven places, to manage the plug-in connections and the retaining eyes, as well as other ancillary functions.
As the IBDM docking mechanism is a flight-critical application, redundant drive systems are required. The backup must function even if the primary drive fails. This is often solved by means of a backup motor that can take over in an emergency. This is the approach used for the locking hook actuator. For the other drive system however, the maxon engineers found a different, unconventional solution: an additional stator is used instead of an extra motor. The flat motor therefore has two stators and hence two windings, each of which is capable of independently driving the rotor – an ingenuous solution, which guarantees safety while saving space.
Gabriel Ybarra praises the collaboration with maxon: “The team understands our requirements and is very quick with design modifications.” Moreover, both partners have a passion for mechatronic systems. “It feels great to be involved in the entire cycle, from design to production and testing. This makes it extremely interesting. And when the system moves for the first time, it's like watching your children take their first steps.”
Image Copyright
SENER / maxon / Sierra Nevada Corp.