maxon Story
Putting the finishing touches to boreholes.
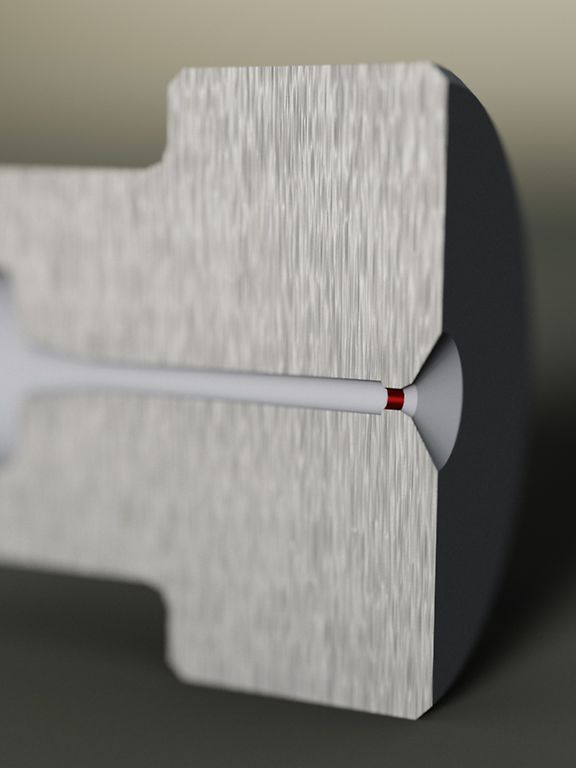
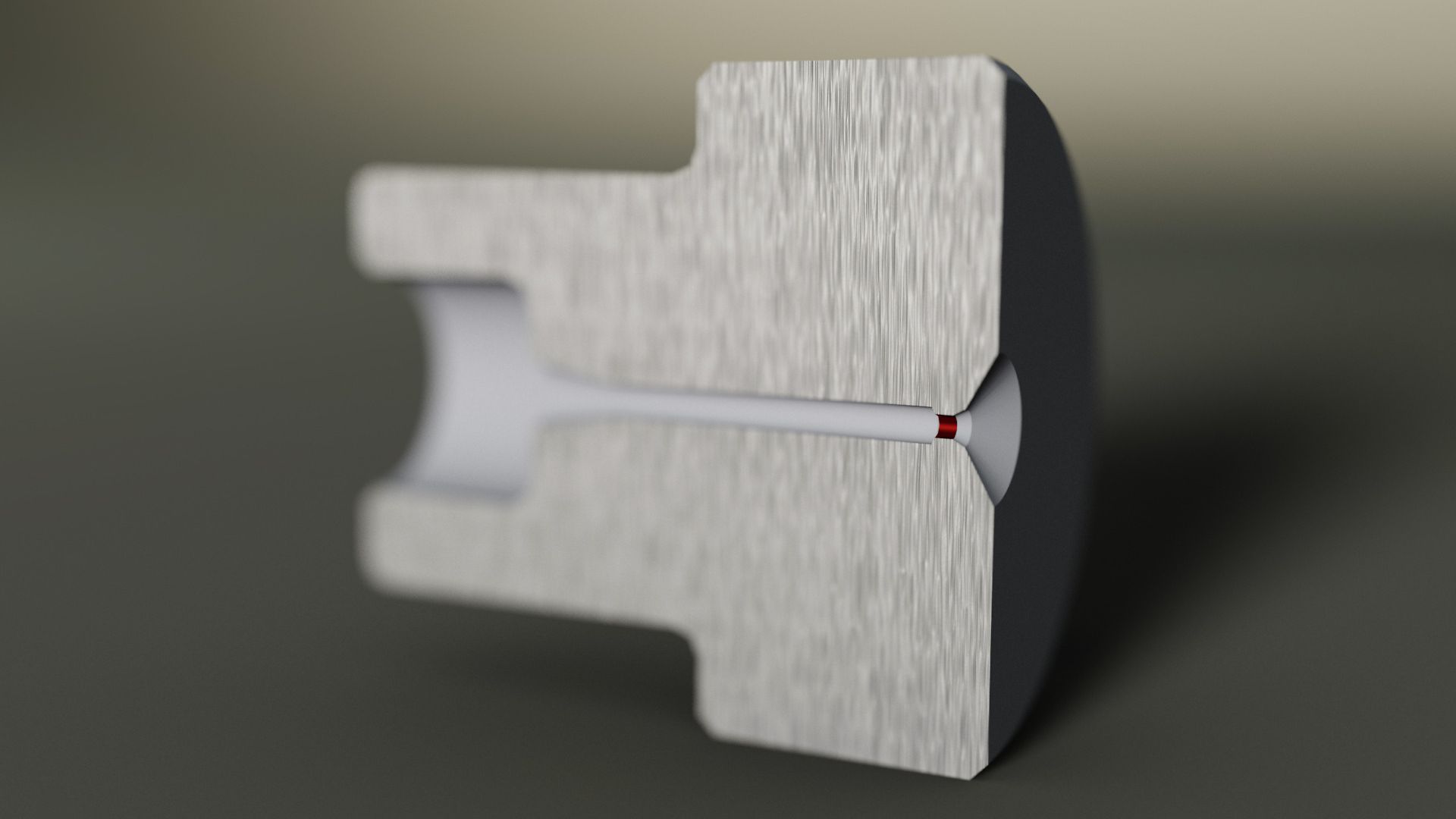
Improving minuscule boreholes: Microcut demonstrates how to suc-cessfully occupy a niche market. The engineers at the Bern-based company regularly turn to the maxon online shop to build their ma-chines.
Superfinishing boreholes doesn't immediately sound like the most spectacular busi-ness area but the team at Microcut, a Swiss company from Lengnau, have perfected a technology that has made them internationally sought-after professionals. They have named their procedure "Microcut Bore Sizing". Simply put, it's all about touch-ing up the tiniest boreholes. And when we say tiny, we mean tiny: We are talking about dimensions in the micrometer range. The smallest boreholes measure a mere 0.015 millimeters – not even a human hair could fit through them. "We don't drill any holes ourselves, we improve existing ones," explains Microcut engineer Adolf von Burg. Especially in markets such as medical technology, fiber optic technology and the automotive industry, perfect bores are in demand – think medical cannulas, mi-nuscule injection nozzles or assembly instruments for microelectronics.
In simple terms, the machining process can be considered a kind of grinding pro-cess. In technical jargon, it's called honing. As an example, cylinders in car engines are commonly treated using honing technology. Only if the cylinders are perfectly round and smooth on the inside can the pistons travel smoothly up and down. Mi-crocut does exactly that – just on a much smaller scale. Depending on the diameter of the bore, a needle-like rod or wire coated with ultra-fine diamond grains or cov-ered in a liquid diamond suspension is guided through an existing borehole. High-precision rotation and longitudinal movement of the wire in the opening enlarges, centers, rounds or polishes the borehole.
The small company processes the workpieces on its own machines in Lengnau ac-cording to customer specifications. The main business, however, is the development and sale of such machines to customers all over the world. "First and foremost, we are mechanical engineers," states Adolf von Burg. Microcut produces and supplies around 5 to 10 customer-specific systems per year. "We can't complain. There is a lot of demand, especially as our technology is also becoming increasingly popular for larger boreholes of several millimeters."
Microcut prefers to use motors made by maxon in the machines they have devel-oped in-house. "We have a long tradition of using maxon components," says devel-opment engineer Thomas Kohler, explaining that in terms of durability, reliability and precision, maxon's brushless DC motors are unsurpassed. Microcut also sources gearboxes, encoders and controllers from maxon, Swiss drive specialists. For some time now, buyer and engineer Adolf von Burg has been using maxon's online shop for this purpose. "A big advantage is that I can see the availability and prices of the products. The shop is very convenient and clearly structured." Microcut engineers have also made frequent use of the possibility of configuring and combining compo-nents online. "A very helpful tool!"
Incidentally, maxon is not only a supplier but also a customer of Microcut. The Bern-based company processes boreholes in small ceramic parts produced by maxon motor in Sexau.