maxon Story
Perseverance & maxon
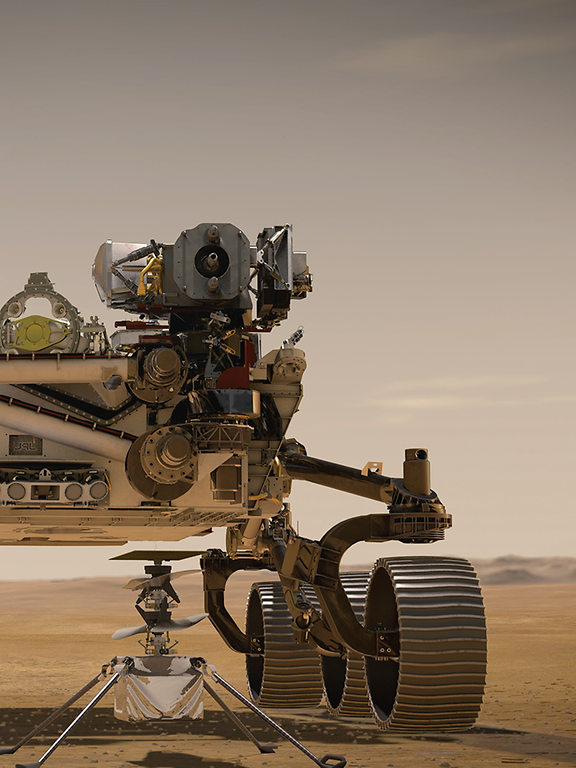
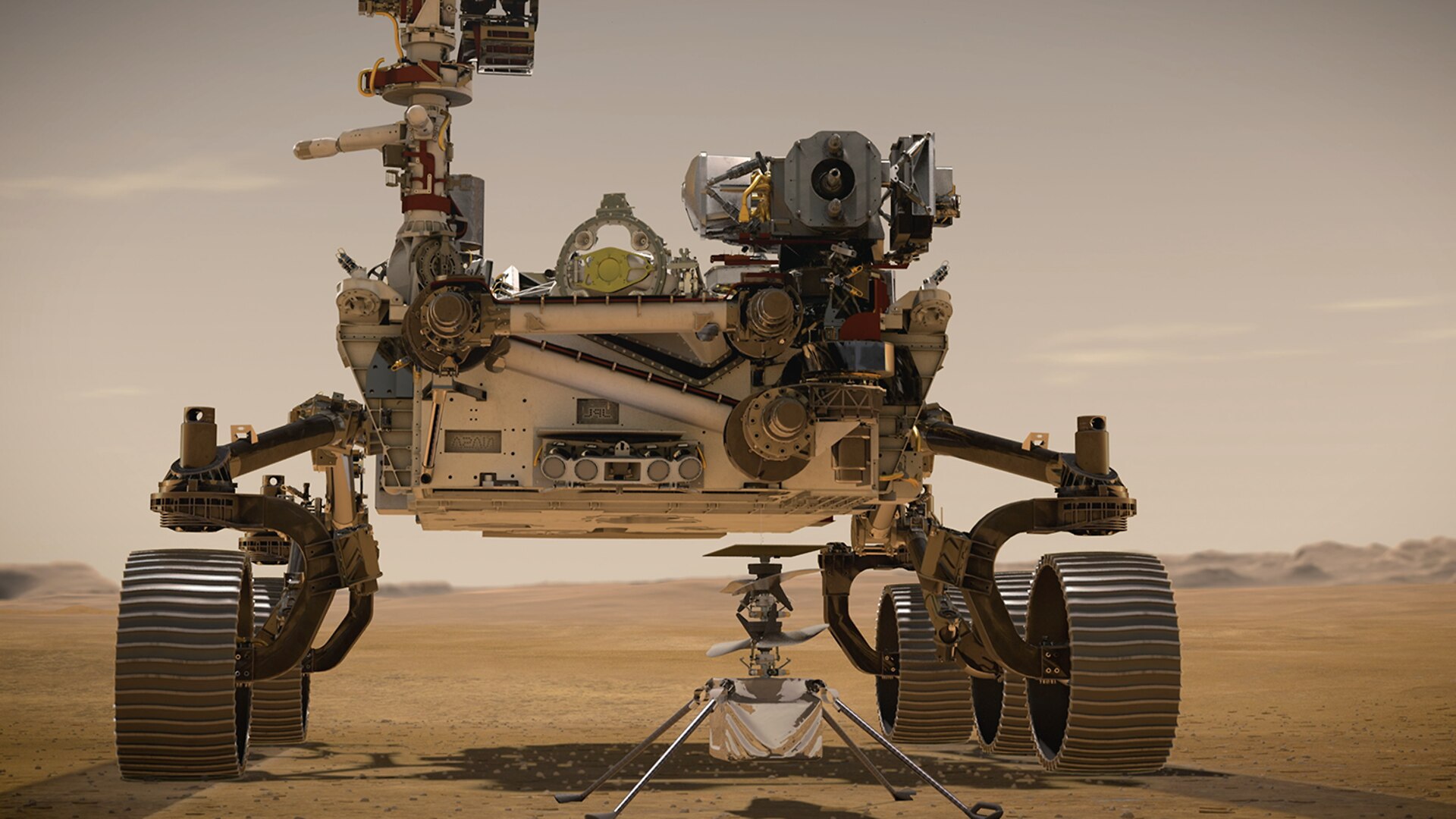
Press release, February 11, 2021
Swiss precision motors handle the valuable Mars soil samples
On February 18, the NASA rover Perseverance will land on the surface of Mars. Was there life on Mars in the past? This is the question that one of the most complex robotic systems ever built by humankind has set out to answer. Several of maxon’s electric drives are used for handling soil samples and for control of the first Mars helicopter.
The excitement is palpable. Will NASA, the US space agency, successfully land a fifth rover on Mars, allowing it to start its series of missions to bring Mars soil samples back to Earth? The aptly named Perseverance rover will enter the atmosphere of the Red Planet on February 18, after traveling a distance of more than 470 million kilometers.
If everything goes according to plan, Perseverance will land in the Jezero crater, which was once filled with water, to search for traces of earlier life. The rover looks a lot like its predecessor Curiosity, but it is equipped with more sophisticated measuring instruments and systems. One of its tasks will be to take up to 30 soil samples, place each of these in a separate container, seal it, and deposit the samples ready for retrieval and return to Earth by later missions, in which maxon will also participate. This “Mars Sample Return” project is by far the most complex series of missions in the history of unmanned space exploration.
NASA’s Jet Propulsion Laboratory (JPL) is responsible for Perseverance and is counting on technology from maxon to handle the samples. There are ten electric drives in the rover. These are responsible for moving the robotic arm that moves the samples from one station to the next. The motors will also be used for sealing and positioning the sample containers.
Drives responsible for mission-critical tasks
Just like the more than 100 maxon drives that have been reliably performing their duties on Mars, the motors for Perseverance are based on standard catalog products: nine brushless DC motors of the EC 32 flat type and one of the EC 20 flat type in combination with a GP 22 UP planetary gearhead.
Working closely with JPL specialists, maxon engineers developed the drives over several years, subjecting them to rigorous testing. After all, a lot depends on the drives functioning properly. Robin Phillips, head of maxon’s SpaceLab, said, “We are involved in absolutely critical applications. If the robotic arm on which our BLDC motors are mounted doesn’t move, or if the gripper doesn't work, then the mission will be a failure.”
maxon is also on board the first Mars helicopter
The helicopter drone Ingenuity is attached to the underside of the rover. Ingenuity will perform the first flights on Mars in the history of space exploration. It is solar powered and weighs only 1.8 kilograms. Six brushed DCX motors from maxon with a diameter of 10 millimeters control the tilt of the rotor blades and thereby the direction of flight. The drives have high energy efficiency, and are dynamic and very light. “In the development phase, we performed extensive tests to make sure that the motors work as intended under the extreme conditions on Mars,” explained Florbela Costa, the project manager at maxon.
With this experiment, NASA wants to test the concept for future drone flights. Flying on Mars is a real challenge. The atmosphere is extremely thin, roughly comparable to the conditions on Earth at an altitude of 30 kilometers. The first drone flights are scheduled for May.
Space applications constitute only a small portion of maxon’s orders, but the stringent requirements push maxon to the next level. This is evident in higher quality standards, as well as new testing methods and processes, which also benefit customers from other areas, such as medical technology. “Apart from this, such space missions are simply incredibly fascinating,” said Eugen Elmiger, CEO of the maxon Group. “Time and time again, I feel honored and proud that our drives are used in these technically groundbreaking Mars missions.”