maxon Story
Laboratory instruments & reliability.
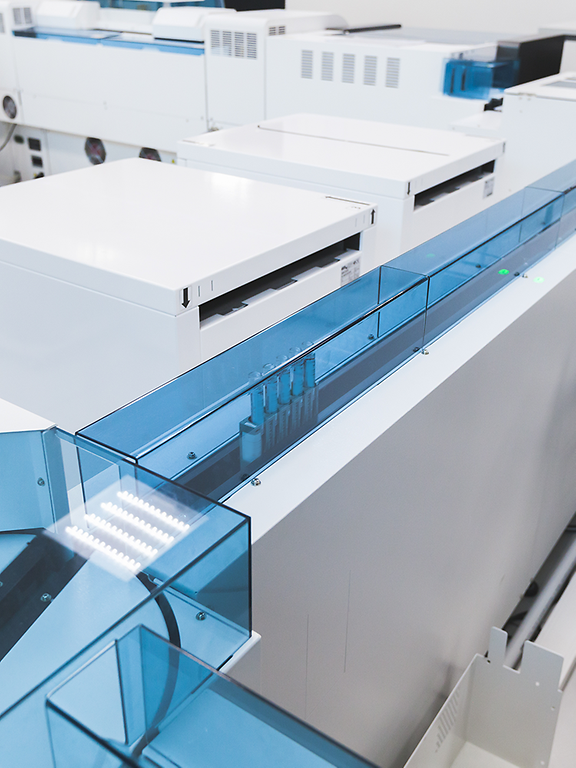

When it comes to laboratory tests, reliability plays a key role. To keep up with the required pace, laboratory equipment must not only be perfectly reliable from a functional perspective, it must also have a long service life. As for the results it delivers, repeatability and precision are essential for perfectly reproducible results. To design laboratory testing machines that are reliable in these two aspects, particular attention must be paid to design choices and motor selection. Explications.
Reliability: a crucial factor for laboratory instruments
To be cost-effective and in line with market expectations, a laboratory machine must provide extremely high throughput. It is not uncommon for this type of equipment to run 24/7. That’s one reason why operation must be optimal, simply to prevent production downtimes. The slightest malfunction would compromise the entire testing process and precious operating time would be lost. The key to good design is therefore to base your device on reliable components that have a long service life and a good level of quality.
Operating temperatures, traceability and cleanliness of supplies, equipment sealing, quantity precision when pipetting—these are just a few of the elements that have to be considered to ensure the repeatability and reproducibility of motions, and the reliability of tests. More specifically, close attention must be paid to the subassemblies used to deliver the test result. These subassemblies perform all the motorized motions required to bring the analyzed sample in contact with the chosen reagents. These motions essentially involve conveying and pipetting.
Reliability of laboratory instruments: good design practices
- Observe the assembly specifications for each component. Even if you may be tempted to stray from the specifications to keep costs down, sub-optimal assembly quality can lead to repeatability deviations between the various products manufactured, which must be avoided for reliability.
- Eliminate operator-dependent settings that are subject to interpretation. Including human intervention during setup runs the risk of discrepancies in the results from one person to another. The operator might not enter the settings properly, or the instructions might not be sufficiently clear. Likewise, if the mechanical parts include a setting option, there is a risk that they will lose their setting over time, and require readjustment.
- Do not skimp on precision, both in the components themselves and the interfaces between the components.
- Keep the entire quality chain under control, in regard to both supplier quality and part acceptance testing prior to assembly.
Do you need assistance with a customized mechatronics project?
Contact our experts
Design choices: how to keep tight control on motion precision
The key challenge in design is to achieve the right level of quality at the right cost, by making the best technical choices for the desired function and the machine’s intended service life. When it comes to motion precision, you have several options:
- Limit switches and stepper motor. If the motor is correctly sized, this combination allows you to control position, but without any feedback.
- Encoders and stepper motor. This combination ensures that you have instant information on the exact position. If you want to maximize motion precision, this is the best option. However, encoders are generally more expensive than limit switches.
Instead of a stepper motor, you can also choose an EC motor (also called a BLDC motor) which will go even further in terms of control capacity and servo-control of motions.
With their onboard intelligence, BLDC motors provide feedback on the motor’s operation, which greatly simplifies control. However, BLDC motors are more expensive than stepper motors. So sometimes it is preferable to use stepper motors combined with limit switches or encoders.
In any case, when it comes to maximizing service life, brushless technologies are the best option, because the inclusion of brushed motors could lead to a limited service life.
Service life and wear items
To provide outstanding reliability, a laboratory instrument’s motors and assemblies must provide long service life. Choices therefore have to be made among the various product ranges available, because not all motors allow you to meet this challenge. Some motor technologies only offer 3,000 hours of operation, whereas others allow you to reach up to 20,000 hours.
Moreover, if there are assembly defects or if the motors end up operating outside their nominal range, this will reduce their service life. It is therefore highly advisable to follow the manufacturer’s recommendations. The same rule applies to all components involved in motion: bearings, pinions, belts, and switching. With these components, you must also think carefully about wear items.
With over 20 years of experience in the medical field, maxon France identifies the most suitable mechanical components and motor types for customers’ specifications, to guide you toward the best and most cost-effective option.
Why trust maxon France?
Because maxon goes beyond acting as a mere supplier of components. As a motion specialist, we work on all aspects of motion, offering motorized modules that match your requirements and preferences, not limiting ourselves to mere motor selection. That’s real added value when it comes to reliability! Our teams provide you with advice to optimize your system architecture and thus improve your machine’s reliability.
A single supplier for the entire subassembly
In order to speed up supplier sourcing and project development, and also enhance the quality of the final subassembly, you can count on the expertise of our specialists in motor systems, who will help you identify the best components for your equipment.
This systems approach enables maxon to develop and manufacture functional modules that you can simply plug into your machine. Are you looking to produce an extremely reliable laboratory machine?