Expert Blog
CAN: What is it and Why use it?
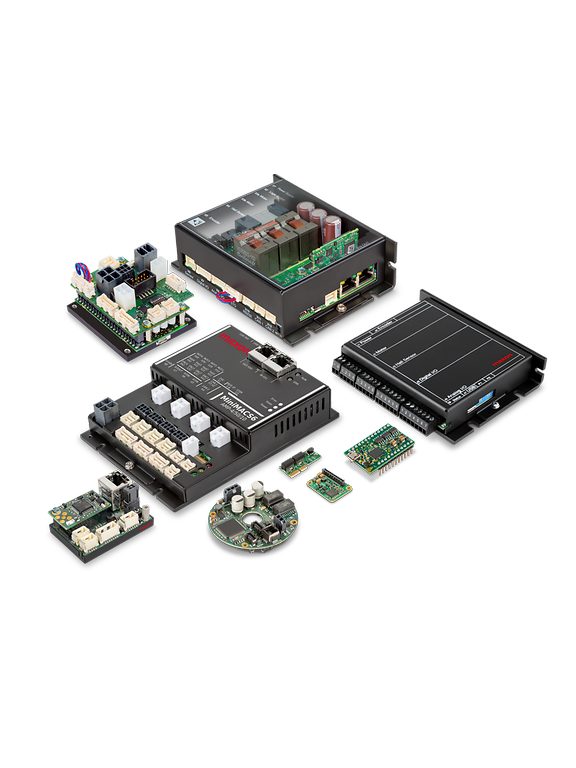
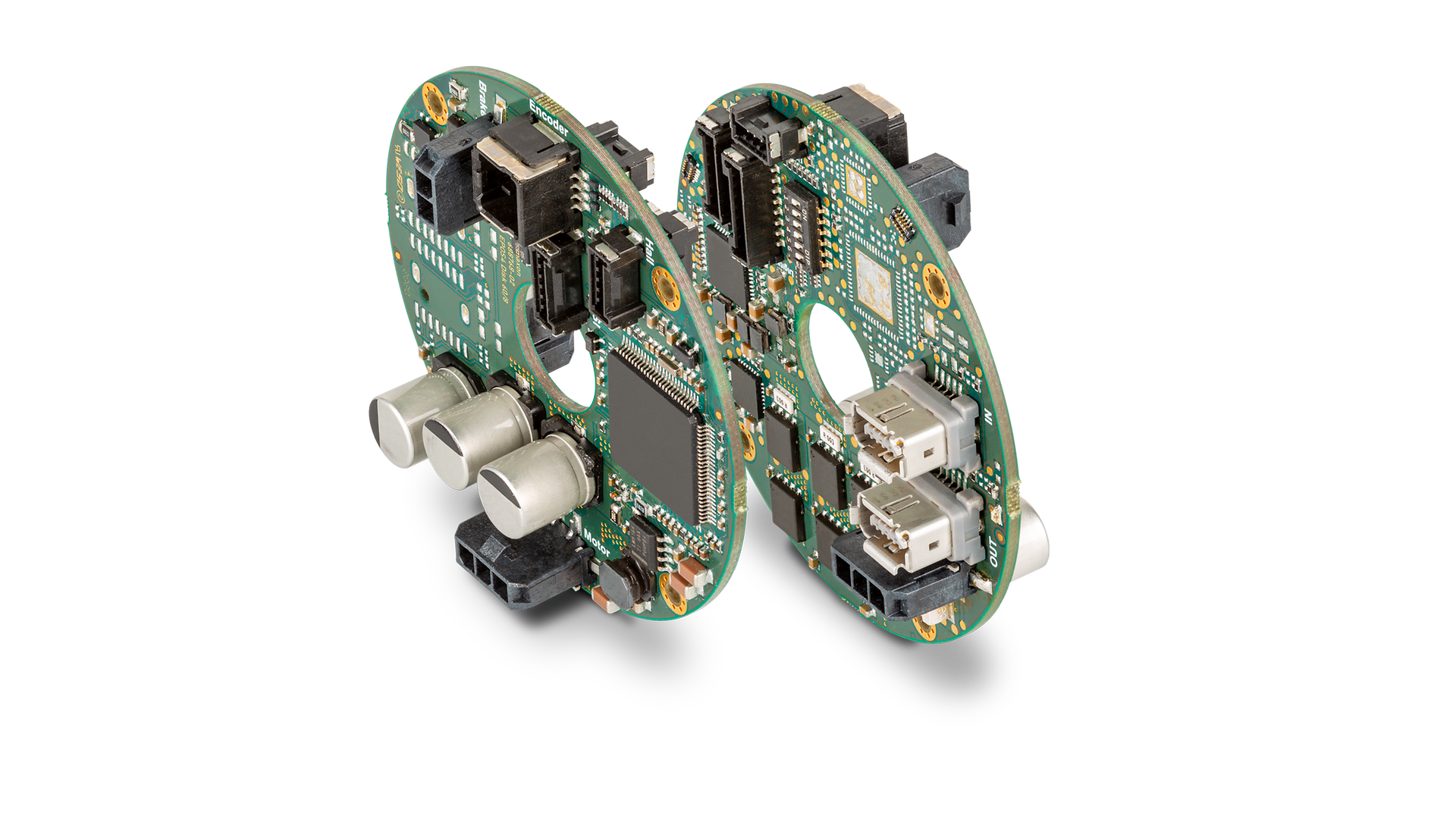
A Controller Area Network (CAN bus) is a bus standard, designed to allow microcontrollers and devices to communicate with each other. It is a message-based protocol, designed originally for a smart and reliable electrical wiring and data exchange of an increasing numbers of actuators and sensors within automobiles. Originally designed as a fieldbus with line lengths of several metres, the CAN-bus today is increasingly accepted as a communication bus within compact machinery and devices.
CANopen is a standardized communication protocol and device profile specification for embedded systems used in automation. There is one CANopen master present in such a network to configure and command all so-called CANopen slave devices (e.g. sensors, actuators, or motion controllers). PCs with a plug-in CAN card or an external USB/CAN gateway, a PLC with CAN interface, or even just a simple microcontroller chip with a CAN interface can act as the CANopen master in such a network. This enables the engineer to choose the best master for his application based on selection criteria like performance, preferred hardware, programming environment, and finally his own experience.
maxon motor’s EPOS4 controllers are industry-proven with more than 1000,000 installations in use worldwide for position, velocity and current/torque control.
CAN offers a number of key benefits to engineers designing for limited spaces, such as the following:
- Compact: Fieldbuses such as CAN-bus enable greater numbers of sensors and actuators to be used with minimal cabling.
- Cost Effective: CAN is known as a low-cost bus, this is due to the high availability of microcontrollers and processors with integrated CAN controllers. The use of the standardized CANopen protocol according to CiA 301 and device-specific profiles such as CiA 402 also significantly reduces the development cost of control software.
- Standardized & compatible: CANopen is a proofed and widely accepted industry standard. CANopen devices exchange data all the same way and the handling of device specific features is described in the device profile standards too. Therefore, it is quite simple to exchange or add devices to such a network. This gives device and machine builders full flexibility to improve the performance of a machine or offering upgrade features without the big effort of a redesign.
For example: If a stepper motor with relevant controller is replaced by a DC motor with another manufacturer’s controller, the control software hardly changes, as both drive systems appear almost the same on the CANbus when using CANopen-profiles. - Easy Synchronization: Even for smaller devices, requirements placed on performance and functional range are increasing all the time and it is becoming important to synchronize individual drives with each other to produce more complex motion processes.
maxon motor’s EPOS4 controllers are CANopen slaves according to the CiA301 and CiA402 standard. These controllers are industry-proven with more than 1000,000 installations in use worldwide for position, velocity and current/torque control. Keeping development and integration smart for developers, maxon provides programming libraries and high-quality support for different kinds of master systems like PLCs, PCs, and Linux-based controllers.